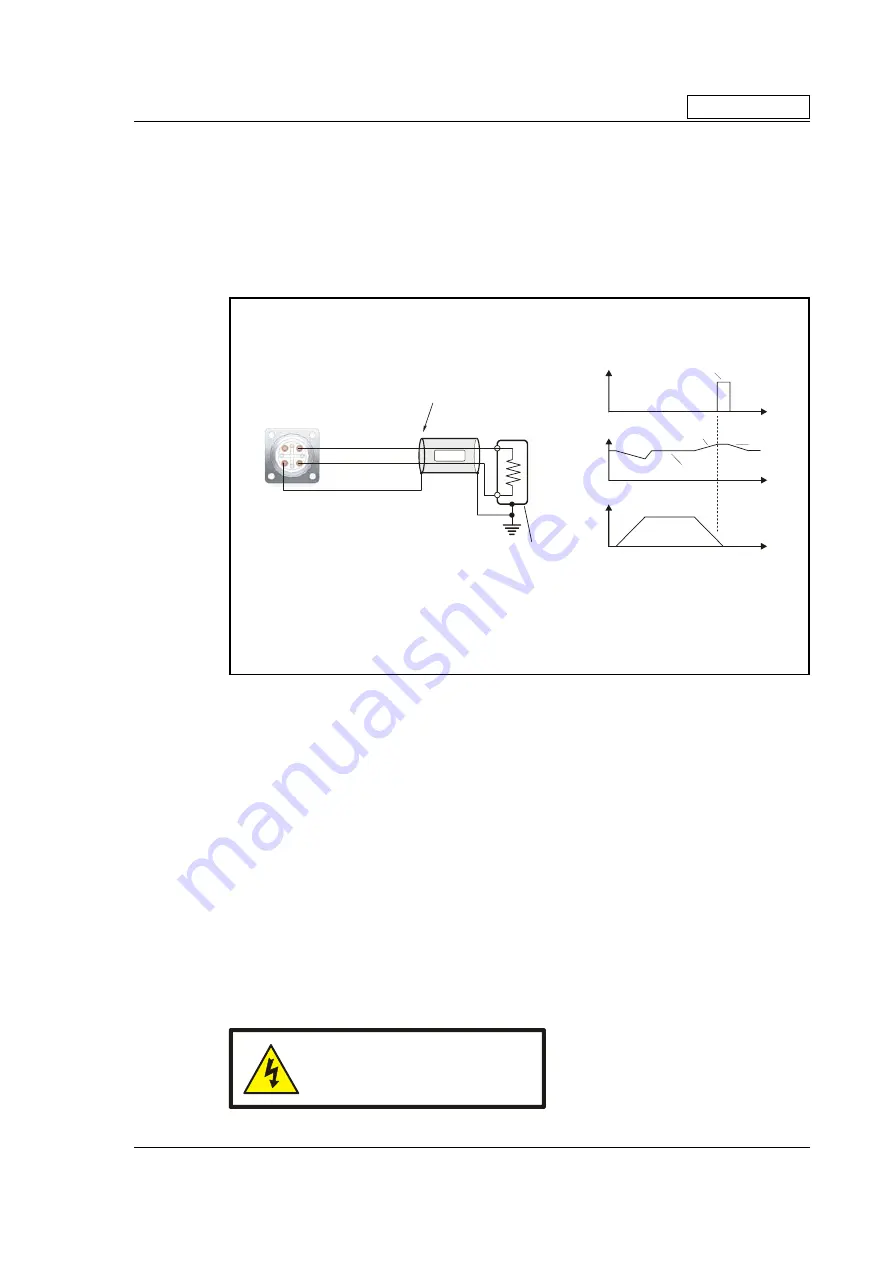
JVL Industri Elektronik A/S - User Manual - Integrated Servo Motors MAC050 - 800
63
3.2.9
Sizing the external fuse (Prefuse).
When using
115V
supply voltage:
To met UL requirements, the prefuse must be a class RK5 such as the type FRN-R-10
(10Amp.) from manufacturer: Cooper Bussmann INC.
When using
230V
supply voltage:
Prefuse T6.3A@230VAC type gG, Do or Dz in the phase line Rated for600V/150kA.
3.2.10
Connecting an external power dump resistor
The internal power dump can absorb up to 6W continuously and 1.4kW peak, which is
considered as appropriate for most applications.
However should a situation occur in which the connected load inertia is too large or the
deceleration too fast, the internal power dump will not be able to absorb all the returned
energy and will report the error message “regenerative overload”.
In this situation the only possible solutions are as follows:
1. Decrease the acceleration/deceleration parameter.
2. Lower the attached load inertia.
3. Connect an external power resistor.
The drawing above shows how to connect an external power resistor. A wirewound
type is recommended since it will be able to absorb higher peak power than other types
of resistors.
Warnings
: Ensure that the resistor value is between 33 to 68 Ohm/50W since the out-
put otherwise can be damaged. Also avoid short-circuit of the output.
Only MAC400
MAC400 with external power dump connection.
TT1173GB
Velocity
Time
Time
Time
Voltage (V)
BO-PD (V)
R
Use a value of 33
to 68 Ohm/50W
Wirewound
Nom. 325VDC
400V
Energy fed back from
the motor to the DC bus
PD activated
when voltage
exceeds 400V
Shielding/housing must
be connected to earth
Note ! : Its only necessary to
connect screen to signal source.
Screen
Common. Is internally connected to the ground of the DC bus.
Is only intended to be used if multiple motors share DC-bus.
Bus output. The internal DC bus is connected to this terminal.
Power Dump output. Behind this terminal is placed a switch
(IGBT transistor) which connect the terminal to the internal
bus ground if the voltage become higher than 400VDC.
Terminal description for the “Dump” connector.
CM =
BO =
PD =
BO
PD
CM
PE
C A U TIO N
- R isk of electric
shock. D isconnect all pow er and
w ait 5 m in. before servicing
Summary of Contents for MAC050
Page 2: ......
Page 4: ......
Page 6: ...2 JVL Industri Elektronik A S User Manual Integrated Servo Motors MAC050 800 ...
Page 7: ...JVL Industri Elektronik A S User Manual Integrated Servo Motors MAC050 800 3 1 Introduction ...
Page 20: ...16 JVL Industri Elektronik A S User Manual Integrated Servo Motors MAC050 800 ...
Page 80: ...76 JVL Industri Elektronik A S User Manual Integrated Servo Motors MAC050 800 ...
Page 112: ...108 JVL Industri Elektronik A S User Manual Integrated Servo Motors MAC050 800 ...
Page 254: ...250 JVL Industri Elektronik A S User Manual Integrated Servo Motors MAC050 800 ...
Page 255: ...JVL Industri Elektronik A S User Manual Integrated Servo Motors MAC050 800 251 5 Appendix ...
Page 300: ...296 JVL Industri Elektronik A S User Manual Integrated Servo Motors MAC050 800 ...
Page 306: ...6 Index JVL Industri Elektronik A S User Manual Integrated Servo Motors MAC050 800 302 ...