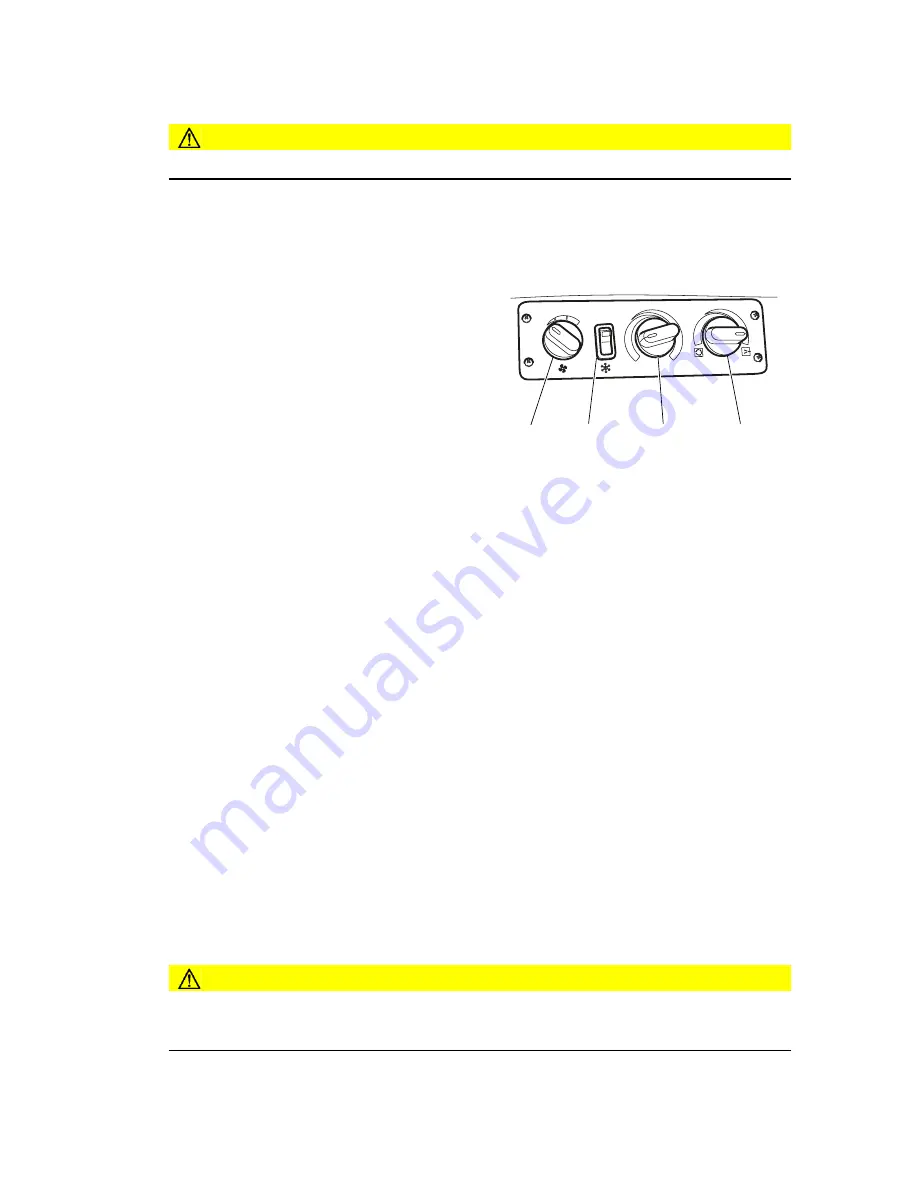
83
11
.1
4
E
N
• The air flow of the air conditioning system is controlled by discharge jets (155) and
an intake nozzle (156) in the legroom (recirculated air) and by drawing in outside
air.
CAUTION!
X
The intake nozzle (156) must always be unobstructed
The air flow in the cab is set via the discharge jets.
4.2.2 Function of the controls
Procedure
• Switch (152) to the left: Recirculated air
• Switch (152) to the right: Outside air
• Centre position of the switch (152):
Combination of recirculated air / outside
air
• Switch (153) provides additional
temperature control.
• The air flow is controlled by switch (154).
Z
Switch off the entire system before parking the truck. To switch off the entire
system, turn the fan switch (154) all the way to the left and press the rocker switch
(the green lamp goes out).
4.2.3 Air conditioning operation notes
Z
If there is a high level of air humidity in the truck, switch on the air conditioning
system. To distribute air evenly to all the discharge jets, set the fan switch (154) to
the highest level, set the temperature selector (153) as required and open the side
sliding window a notch. When the humidity has been removed from the interior of
the truck close the windows again and set the required air flow.
Z
To cool off the interior quickly, turn on the air conditioning system. To distribute air
evenly, open all the discharge jets. Set the fan switch (154) to the highest level and
open the side sliding window a notch. When the desired temperature has been
reached, close the windows again and set the required air flow.
Z
To guarantee maximum operation of the air conditioning system it must be
switched on in the cold season at least once a month for about 10 minutes
(refrigerant needs to be recirculated).
Z
When the air conditioning system is operating, condensation water may be visible
underneath the truck. This happens during the air dehumidification process, in
particular at high external temperatures and high air humidity.
CAUTION!
Regular servicing of the air conditioning system is required to ensure it can
work at a consistently high level, see "Servicing and Inspection" on page 199.
152
153
150
154
Summary of Contents for DFG 660
Page 3: ...11 14 EN 4...
Page 13: ...11 14 EN 14...
Page 26: ...27 11 14 EN...
Page 47: ...11 14 EN 48...
Page 129: ...11 14 EN 130 8 Optional equipment...
Page 141: ...11 14 EN 142 Drive the truck forward Press down on the hand lever 202...
Page 149: ...11 14 EN 150...