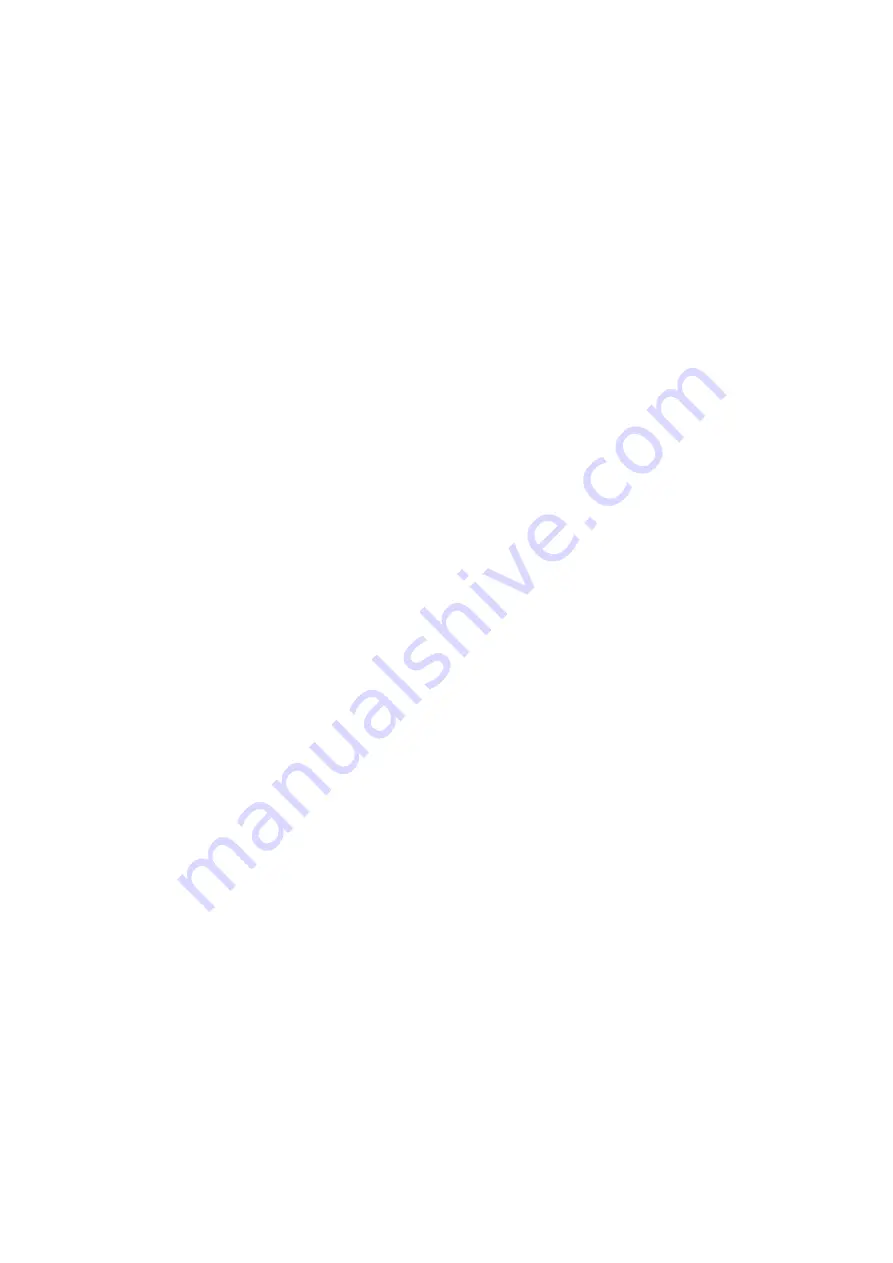
Table of Contents
1.
Head Unit .................................................................................................................1
2.
X-Y Unit ....................................................................................................................3
3.
Board Transport Unit................................................................................................5
4.
ATC (Auto Tool Changer) Unit ................................................................................8
5.
VCS (Vision Centering System) Unit ......................................................................9
6.
CAL Block ..............................................................................................................10
7.
HOD (Handled Operating Device) Box ................................................................11
8.
Vision Monitor.........................................................................................................11
9.
Signal Light.............................................................................................................12
10.
Keyboard Bracket Assembly.................................................................................13
11.
Feeder Relay Cable of the Connector Bracket......................................................14
12.
Safety Cover.........................................................................................................15
13.
Filter Regulator (Air Assembly)...............................................................................16
14.
Replacement Table (Optional) ..............................................................................17
List of Supplied Parts to Be Packed ......................................................................20
15.
Hand disk ...............................................................................................................24