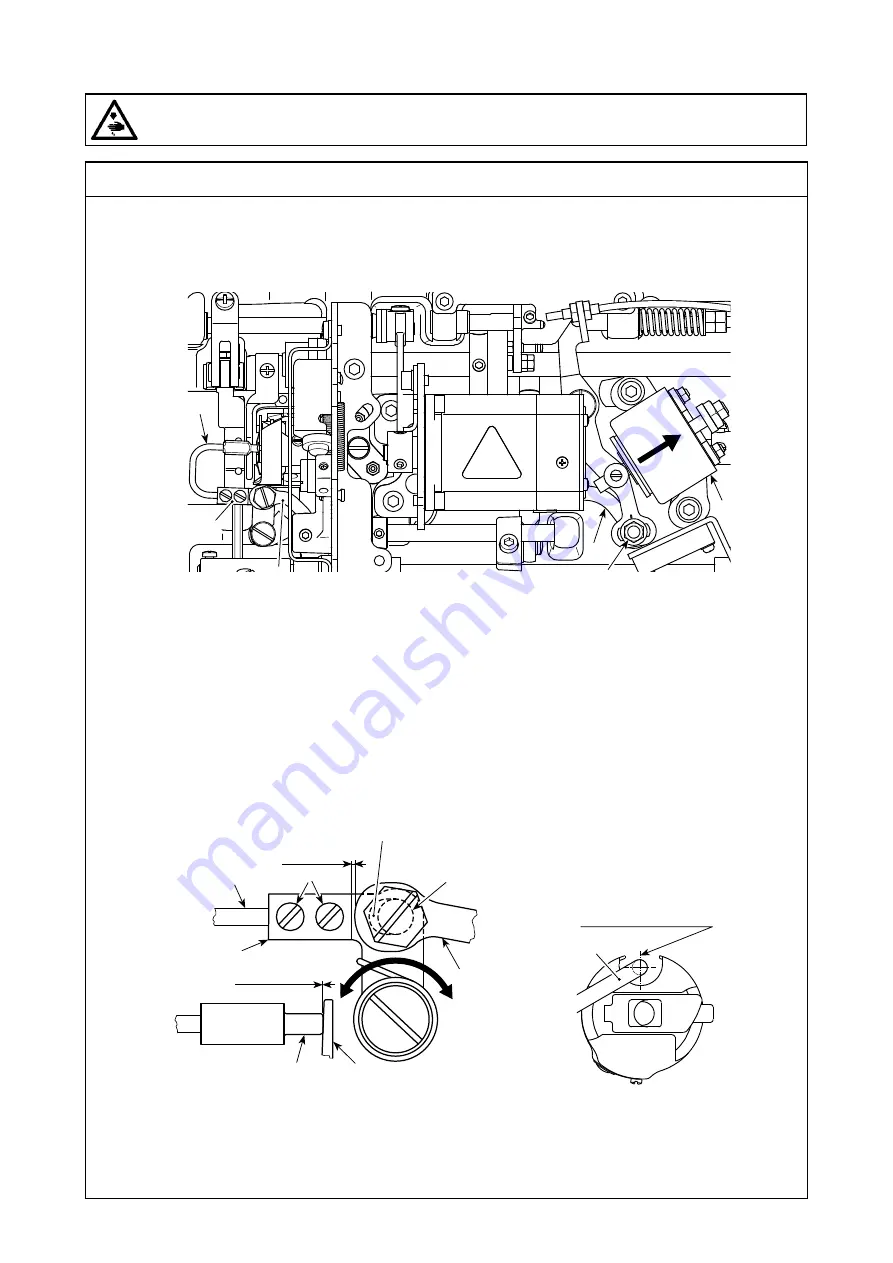
❶
❷
❸
❻
❸
❹
(9) Adjusting the thread trimming unit
WARNING :
Be sure to turn the power OFF before the following work in order to prevent personal injury due to
unintentional starting of the sewing machine.
Standard adjustment
7) Adjustment of the picker
(0.5 mm)
To be in contact
Once the standard adjustment is carried out
correctly, there is a slot-shape space in picker
link
❸
to allow the picker to make a necessary
returning action (damper function).
0 to 0.3 mm
❼
❸
❺
❻
❹
❻
❻
I n t h e s t a n d a r d
adjustment state of
the picker, the center
of picker
❻
is almost
aligned with the
center of U-shape
section of bobbin
case.
– 62 –