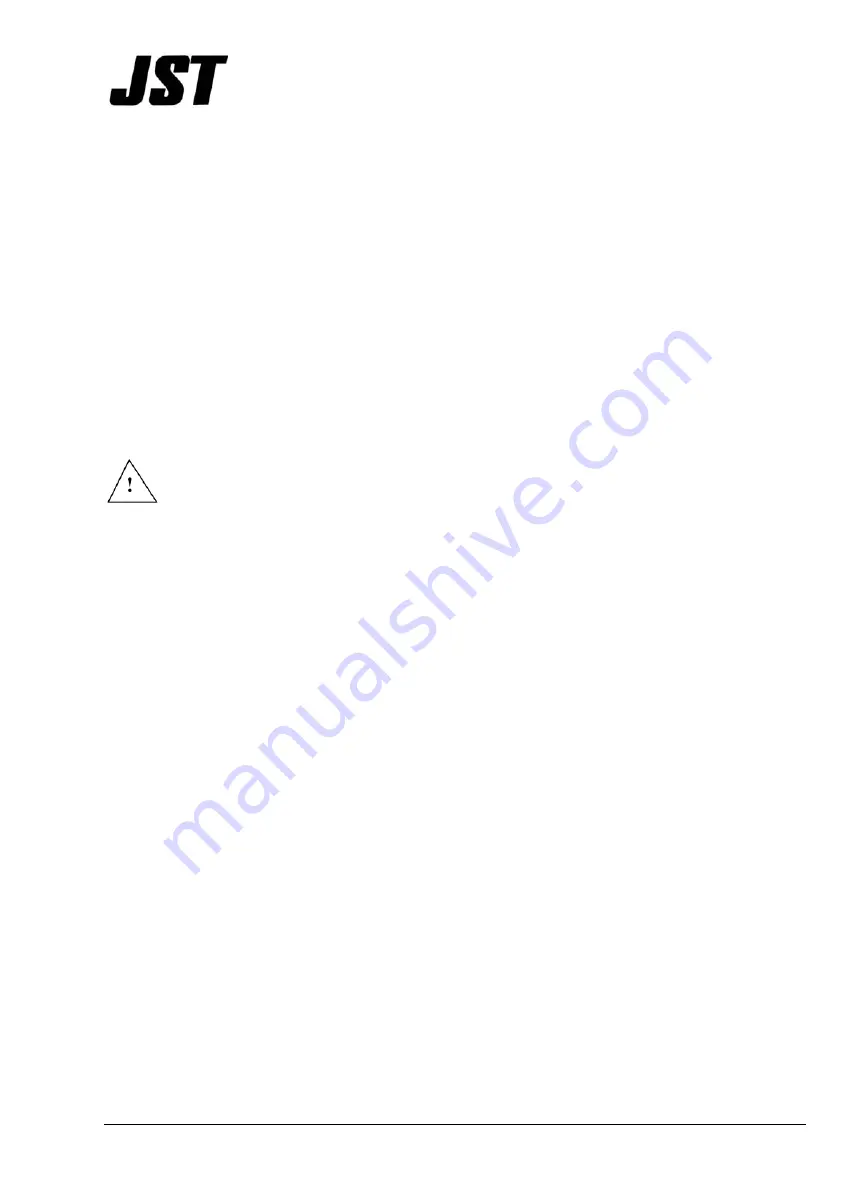
Page 26/27
The Quality Connection
10. Preventive Maintenance
fied application tooling
d and maintained in accordance with the following schedule.
solate from the electricity supply. Remove the safety
Clean all wire and terminal scrap from the tooling with the aid of a small paintbrush.
Caution
e and could either cause injury to persons nearby or be forced
to moving parts of the tooling.
10-1-3
age. If any parts are damaged, please contact JST to order replacement
10-1-4
cess grease will either drip onto the tooling or will
ng punches and that
10-1-6
safety cover with a general-purpose aerosol spray
the daily checks, the following maintenance should also be carried out on the
fer to the Dies Construction Sheet supplied with the tooling for the
10-2-2
a
ng a sawing motion, polish the form until a brilliant mirror-like finish is restored.
Quality Statement
he quality of a finished crimp is dependent on the use of the manufacturers speci
T
that has been cleane
10-1.
Daily Care
0-1-1
Turn off the crimping press and i
1
covers from the crimping press.
10-1-2
The use of a pneumatic airline to clean the tooling should be avoided. Any debris on the tool will
e blown away under great forc
b
in
Visually check the crimping dies, shear section and stripper blade for evidence of
wear or dam
parts.
Check that there is a thin film of grease on the bearing surface of the ram, if
necessary apply general-purpose grease to restore the lubrication. Do not over
grease the ram, because the ex
attract debris.
0-1-5
Check that the dial settings are aligned correctly over the crimpi
1
they are correctly set to the pre-determined reference position.
Check that the safety covers are in a good serviceable condition and replace on the
tooling. Clean the polycarbonate
cleaner to restore good visibility.
Weekly care, or when removing the applicator from the press for storage.
In addition to
10-2
tooling.
10-2-1 Remove the crimping punches from the ram (part numbers are affixed 63*** or 64***);
please note the sequence of disassembly so that the parts can be replaced in the
correct order. Re
assembly order.
Hold each crimping punch in a vice and with the aid of a piece of waste cloth apply
mall amount of a good quality metal polish into the crimp form of the punch.
s
Usi