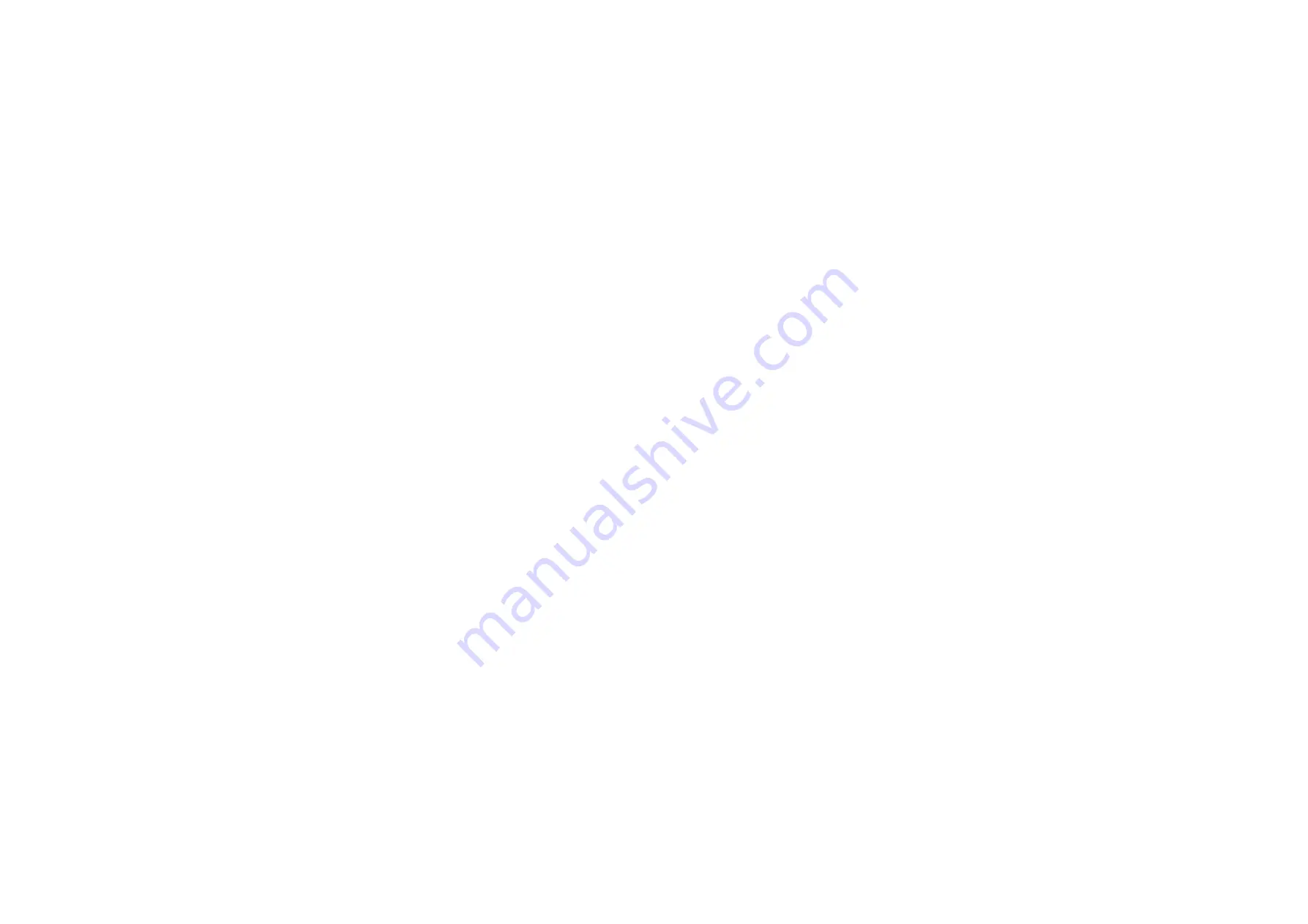
ZZ1027/3
7
14
SYMPTOM
POSSIBLE CAUSE
REMEDY
a. Pilot will not light.
i.
No gas supply to heater.
Check for gas at inlet pressure test
point on Multifunctional Control.
ii.
Gas supply pipe not purged.
Purge gas supply pipe in accordance
with BS 6891.
iii
Pilot orifice restricted.
Clear pilot orifice or replace pilot injector.
iv.
Piezo system faulty.
Check igniter, lead, and electrode.
v.
Excessive gas supply pressure.
Check that mains gas pressure is 37mbar,
and reduce if necessary.
b. Pilot lights but goes
i.
Connection between thermo-
Check connection is secure.
out on releasing START
couple and Multifunctional
button during initial
Control not secure.
light-up, or after
normal operation.
ii.
Faulty power unit on
Replace Multifunctional Control.
Multifunctional Control.
iii.
Faulty thermocouple.
Replace Thermocouple.
c. Main burner lights
i.
No voltage to fan.
Check connections from electrical panel to fan.
but fan fails to run
after approx. 3 min.
ii.
Loose electrical connection
Check connections.
Fan Delay Control.
iii.
Fan Delay Control set incorrectly.
Check for correct settings.
iv.
Faulty fan assembly.
Replace, taking care not to damage
impeller.
v.
Faulty Fan Delay Control.
Replace.
d. Main burner opera-
i.
Gas rate or burner pressure
Check gas rate and burner pressure
ting intermittently
setting high.
setting.
with fan running.
ii.
Temperature rise excessive.
Adjust fan speed or gas rate accordingly.
iii.
Air filter or return air path
Check filter is clean and air path is clear.
restricted.
iv.
Excessive number of outlets
Open additional outlets.
closed.
v.
Spillage of flue gases.
Carry out spillage test and rectify.
vi.
Spillage monitor device (TTB)
Replace Spillage device (TTB)
faulty.
e. Main burner opera-
i.
Gas rate or burner pressure
Check gas rate and burner pressure
ting with intermittent
setting too low.
setting.
fan operation.
ii.
Fan Delay Control set incorrectly.
Check for correct settings.
f. Fan runs for excessive
i.
Fan Delay Control set incorrectly.
Check for correct settings.
period or operates
intermittently after
main burner shuts down.
g. Noisy operation.
i.
Gas pressure too high.
Check burner pressure setting.
ii.
Noisy fan motor.
Replace fan assembly.
iii.
Fan speed setting too high.
Adjust fan speed.
h. Pilot alight but main
i.
Mains electrical supply not
Check mains supply.
burner not igniting.
connected to heater.
ii.
Controls not demanding heat
Check that time control and room thermostat
are operating correctly.
iii.
3A fuse failed.
Replace. If failure occurs again, check
wiring for short circuits.
iv.
Loose connection to room thermo-
Check connections.
stat, Limit Switch, Multifunctional
Control lead, Time Control, or
transformer.
v.
Transformer open circuit.
Check with test meter and replace electrical
assembly.
vi.
Multifunctional Control faulty.
Replace Multifunctional Control.
vii.
Limit Switch faulty.
Short circuit switch, and replace if necessary.
ix.
Room Thermostat or external
Fit temporary loop in heater Thermostat
wiring faulty.
socket. If heater ignites, external circuit
or room thermostat is faulty.
5.2.2
Room Thermostat and its location.
a.
The Room Thermostat should be located where there is free air circulation approx. 1.5m (5ft) from the floor.
b.
Avoid the following locations:
i)
In a room where temperature is greatly affected by the sun or any other heat source, e.g. radiant fire,
wall light fittings or TV set.
ii)
Near an outside door or windows, or on an outside wall.
iii)
Where affected by warm air ducts, diffusers, waste pipes or the heater itself.
iv)
Where subject to vibration.
c.
Connect room thermostat wires control panel terminals ‘16’ and ‘17’
5.3
GAS (SEE BS 5864 AND BS 5482)
5.3.1
An independent gas supply pipe from the meter is to be preferred wherever possible. When this is not possible, the
pipe must be capable of taking the complete input of the heater and all other gas appliances being served by this
same pipe. This supply should be suitably sized to conform to British Standards requirements of no more than 2.5
mbar (1.0 in wg) pressure drop (BS 5482 Pt. 1).
5.3.2
The
1
/
2
in union gas cock (supplied) must be fitted to the gas inlet of the heater for easy isolation during servicing.
The gas pipe should be so fitted and installed as to be durable, substantial and gas tight. To assist in determining
whether a gas connection may not be tight, a leak detection fluid should be applied around the connection. Under no
circumstances should a flame be used to locate a gas leak. Gas entry to the air heater is through either side to a Rc
1
/
2
(
1
/
2
in BSP. external [taper] thread).
5.4
DRAUGHT DIVERTER & DEFLECTOR PLATE:
5.4.1
The HI-SPEC J50P heater is supplied with a draught diverter which houses the TTB, and which requires fitting to the
rear of the heater prior to installation, using 6 x 4mm screws and lock washers (provided). Connect the TTB to the
terminal block situated on the rear upper left hand corner of the appliance.
5.4.2
The deflector plate prevents spillage from the draught diverter in the event of a leak between the air heater and the
base plemum and MUST be fitted as shown in fig 3 using the screws provided.
5.5
DEFLECTOR PLATE SAFETY CHECK:
In order to ensure that the deflector plate is preventing warm air from entering the draught diverter and therefore causing spillage,
the following test MUST be carried out BEFORE commissioning:
5.5.1
Turn on the power supply to the heater.
5.5.2
Set the summer airflow switch to “on”.
5.5.3
Using a smoke match, introduce smoke into the heat exchanger at the burner opening.
5.5.4
Ensure that the smoke is drawn into the heat exchanger and not blown back from the burner opening.
5.5.5
If smoke is blown back from the burner opening, check for air leaks between the heater and the base plenum,
paying particular attention to the rear of the heater directly beneath the draught diverter.
6.
COMMISSIONING
6.1
PREPARATION:
6.1.1
Ensure that:
a.
Gas and Electrical supplies are
OFF
.
b.
Filter, fan and fan compartments are free from obstructions.
c.
All registers or grilles are open and conform to design specifications.
d.
Return, relief and ventilation air installations are adequate.
6.2
SYSTEM BALANCING:
6.2.1
Set the heater electrical supply ON.
6.2.2
Set the SUMMER AIR CIRCULATION switch to ‘
ON
’.
6.2.3
Balance the system to provide the required volume proportions at the warm air outlets.
NOTE:
If the system includes ceiling diffusers, air velocities through these should be NOT LESS THAN 1.5m/s (300ft/min), except
for very small rooms, (i.e. bathrooms etc.). Outlet faces may require partial blanking in order to achieve this.
6.2.4
Set the SUMMER AIR CIRCULATION switch to ‘
OFF
’.