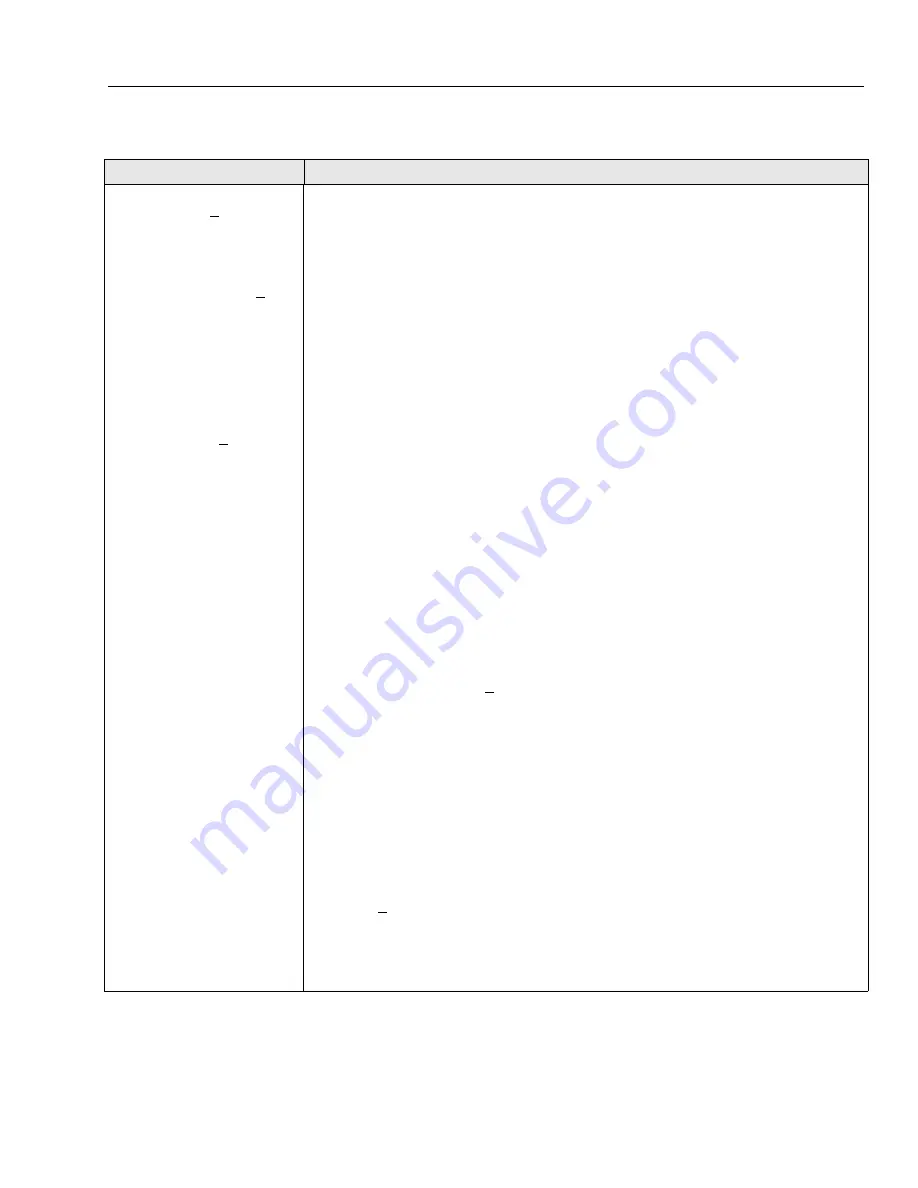
SECTION 6 - LSS SETUP/CALIBRATION/SERVICE
31215079
6-9
Table 6-8. LSS Troubleshooting Chart - Measurement Performance
DIFFICULTY
POSSIBLE RESOLUTION
Empty Platform Weight (DIAGNOSTICS,
PLTLOAD) is not 15lbs (±7kg) of
zero.
or
Platform Load readings (DIAGNOTICS, PLT-
LOAD) are unstable by more than +2lbs
(±1kg) (without the influence of vibration
or wind).
or
There are large variations in Platform Load
(DIAGNOSTICS, PLTLOAD) based on the
location of the load. Tolerance to variations
is 40lbs (18kg) for an evaluation using the
technician’s weight, and +5% of Rated
Load when using calibrated weights.
The LSS Module is unable to properly measure the platform weight.
1. One of the Shear Pin Load Cells is not properly plugged into the LSS Module. Since the connectors seal with an O-ring
and are located in a crowded area, it is possible that the connectors are threaded together, but poor electrical contact
is made. Attempt to wiggle the molded portion of each connector on J5-J8. If properly tightened, the molded portion
should not move. Also, examined each Shear Pin Load Cell’s readings via the JLG Analyzer. Proceed to the DIAGNOS-
TICS, CELL 1-4, LOAD displays and determine if the readings are reasonable. Note that it is possible to have only two
sensors carrying all of the platform load due to fit between the platform and support structure (this is normal).
2. Wiring leading to one of the Shear Pin Load Cells is damaged. Examine each sensor’s reading using the JLG Analyzer.
Proceed to the DIAGNOSTICS, CELL 1-4, LOAD displays and determine if the readings are reasonable and responsive to
slight downward pressure above the sensor being viewed. Carefully inspect sensor wiring where it passes through
cable clamps for signs of damage. Inspect wiring where damage to the channel is apparent. If damage to the sensor’s
cordset is found, replace the appropriate Shear Pin Load Cell since the cordset is not serviceable (connector is molded
for moisture resistance; cordset is soldered into sensor beneath welded stainless steel cover). If damage to the sen-
sors extension cordset is found, unplug both ends and fit a replacement.
3. One of the Shear Pin Load Cells was not assembled properly during installation. Examine each sensor’s reading using
the JLG Analyzer. Proceed to the DIAGNOSTICS, CELL 1-4, LOAD displays and determine if the readings are reasonable.
It is often helpful to apply slight downward pressure above the sensor being examined and observe that its output
increases (increasing force measurement; decreasing means the sensor is mounted upside-down). Compare the
order of assembly to the detail on the Installation Drawing and ensure that the only contact between the platform
and the support is through the sensor bodies (nothing else touches except wires). Re-assemble according to print if
necessary.
4. Damage to the platform or arm structure has occurred or one of the components is out-of-tolerance.Twists in the
platform, for instance, will cause huge off-axis forces to be applied to the Shear Pin Load Cells, disturbing their pri-
mary measurement axis readings. If Lift Up / Down is noisy or not smooth, examine this issue thoroughly. Resolution
is to replace the damaged or faulty component. Watch for Shear Pin Load Cell damage (yield) as a result of this diffi-
culty.
5. One of the Shear Pin Load Cells is contaminated by debris or moisture. Examine each sensor’s reading using the JLG
Analyzer. Proceed to the DIAGNOSTICS, CELL 1-4, LOAD displays and determine if the readings are reasonable and sta-
ble (not changing by more than +2lbs (±1kg) (without the influence of vibration or wind). Lack of measurement
stability is a key indication of contamination. Unplug the appropriate connector (J5 is CELL 1, J6 is CELL 2, J7 is CELL 3,
and J8 is CELL 4) and inspect for dirt or moisture. Look carefully into the female connector on the sensor’s cordset for
evidence of contamination. Debris should be brushed away with a soft bristle brush (do not introduce any cleaners as
they will leave conductive residue). Moisture should be allowed to evaporate or accelerated with a heat-gun (use low
heat and be carefully to not melt connector materials). Moisture intrusion into the molded portion of the connector
(capillary action into the wire bundle) or the Shear Pin Load Cell itself will require replacement of the sensor.
6. One of the Shear Pin Load Cells has been mechanically damaged (yielded). Any Shear Pin Load Cell that is physically
deformed or has damage to one of the stainless steel covers should be replaced immediately. It is also possible to
have invisible mechanical damage resulting from an extreme overload (>4200lbs [>1900kg] for 1.25 in diam.;
>5700 lbs or 2600 KG for 2 inch diam.). This can be detected by supporting the platform with an overhead crane and
by removing the suspect sensor (no weight resting on the Shear Pin Load Cell). Examine the sensor’s reading using
the JLG Analyzer. Proceed to the DIAGNOSTICS, CELL 1-4, LOAD displays and observe whether the unloaded sensors
read with +15lbs (±7kg) of zero (individually). Replace sensors that read excessive force when physically unloaded.
7. The LSS Module is suspect. Interchange the Shear Pin Load Cell connections (J5-J8) and observe the results via the
JLG Analyzer. Proceed to the DIAGNOSTICS, CELL 1-4, LOAD displays and observe the readings. If the problem seems to
remain with a particular sensor, carefully re-examine the issues above. If the problems seems to remain with a par-
ticular LSS Module channel, substitute another module.
Go
to
Discount-Equipment.com
to
order
your
parts