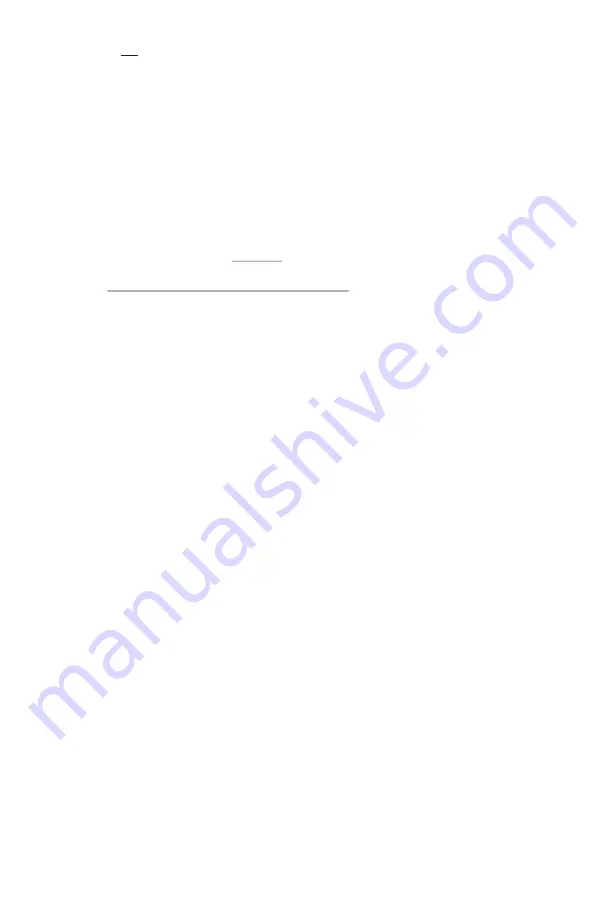
18
19
Calibrating the torque transducer:
You can not change the information on the smart chip within the transducer. If the
values on the chip need to be changed then one of two things MAY have happened:
1. The torque arm system, or the procedure, is introducing errors that when added are
creating an out of tolerance situation (SEE ACCURACY CHECKING ABOVE)..
2. The transducer has been damaged and needs repair (usually shown by significant
errors). If this is the case return the transducer for repair or re-calibration.
Bypassing the smart transducer feature.
If you want to bypass the smart chip calibration data, and use the calibration data that
you create with your torque arms, you can do so by assigning a “custom” transducer
number to the transducer and manually calibrating it using your own dead weight
system. This method stores the calibration data for the transducer in the memory of the
meter, not in the memory chip inside the transducer. In order to use the custom
transducer data you must select the custom transducer number when you power on the
unit (see selecting custom transducers below). If you do not select the custom
transducer number the meter will revert to the calibration data on the chip inside the
transducer.
You can tell if the system is using the smart chip inside the transducer if, after pressing
the transducer keys you see the words “auto Xducer”. You will see the words “custom”
transducer if you have selected the transducer manually.
To manually calibrate a “custom” transducer
1. From normal operation mode press the menu buttons
2. Press the next key until the word “CAL” is displayed. Press the save key to select
the cal option.
The current default custom transducer number (01 to 15), will show and flash (unless it
is a smart transducer in which case you must press the next key to select a custom
transducer number).
Press the next key until the desired custom transducer number is shown (mark this
number on the transducer for future reference).
Note:
The current transducer settings for the transducer number will show as you scroll
through the transducers, all default values are “9999” or “1000” and 2.000 Mv/v.
Press the save key to select the desired transducer number.
The current full-scale range will now be displayed (will default to “9999” if this number
has never been assigned) with the first number flashing (do not worry about the
position of the decimal, that will be set next).
3. Press the increase and key to make the digits read the full-scale range of the transducer
you are going to calibrate. Press the save key
4. Now set the decimal position with the next key (keep pressing until you see the decimal
point)..
Press the Save key.
5. Set the units by pressing he units key. Press Save.
6. Set the estimated clockwise (cw) Mv/v (if known, use 2.000 if not known). Press Save.
7. Set the Counterclockwise (ccw) Mv/v (if known, use 2.000 of not known). Press Save.
8. The display will now show “calc” (more on “calc” later). Press the next key until the
unit shows “cert”. which means you are going to calibrate (certify) a transducer with dead
weights.
The display will now show “CCW CAL0” This means it is ready to take a
counterclockwise zero reading.
SEE ACCURACY CHECKING PROCEDURES FOR THE PROPER METHOD TO
LOAD A TRANSDUCER.
9. Load the transducer, with a balanced arm and a slight pre-load, in the counter clockwise
direction three times to full scale with dead weights, and remove the weights but not the
arm and pre-load hanger. Wait 30 seconds or for the hanger to settle and press the Zero
buttons (even if the display shows 000.0).
The Display will now show “CCW FS” which is prompting you to apply the
F
ull-
S
cale
weights to the arm in the counterclockwise direction.. Apply the full-scale weights in the
counterclockwise direction, stabilize the weights and press the save key.
Make the display read the full-scale counterclockwise value (within tolerance) with the
increase and next keys. Press the save key.
10. The display will now read “CW CAL0”. This means the meter is ready to read the
clockwise zero reading. Load the transducer, with a balanced arm and slight pre-load, in
the clockwise direction three times to full scale with dead weights, and remove the weights
but not the arm and pre-load. Wait 30 seconds or for the hanger to settle and press the
Zero buttons (even if the display shows 000.0).
The display will now show “CW FS” which means load the arm to full scale in the
clockwise direction. Press the save key.
Make the display read as close as possible to the full scale clockwise value by pressing
the increase and next keys.
Press the save key.
You will now exit and be in the track mode with the display reading the calibrated full
scale clockwise value. The calibration data you just created will be saved in the memory of
the meter, under the custom transducer number you assigned to that transducer.
From now on, if you want to use the manual calibration values that you just entered you
Summary of Contents for TTS-1000
Page 1: ...1 TS 1000 TTS 1000 Torque Tester Operation Manual Rev 2 2008...
Page 29: ......