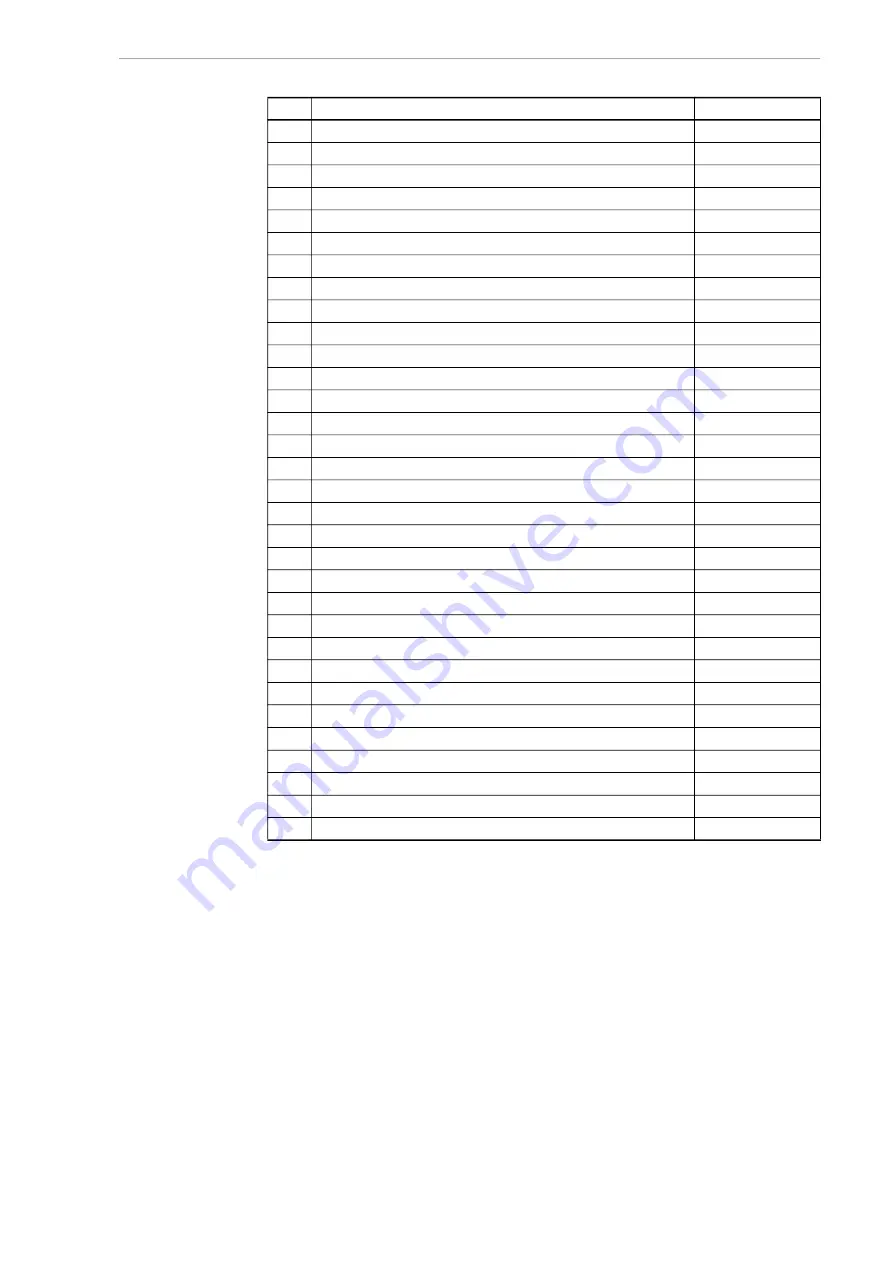
inoMIG 350/400/500
20 Spare parts list
BA-0014 • 2020-06-05
EN
-
49
Tab. 19
Spare parts list for DVK3-MC-R
Pos.
Name
Item no.
A
Hood DVK3 – 2010
715.042.206
B
Right side panel DVK3 – 2010
715.042.207
C
Knob 21 mm (optional)
305.020.050
Cover for knob (optional)
305.020.051
D
Front panel MC-R
715.011.061
Knob 28 mm (optional)
305.042.010
Cover for knob (optional)
305.042.011
E
7-pole Tuchel plug
410.007.111
F
Quick-action coupling DN 5– G 1/4 I
355.014.007
PVC washer, red
101.011.047
PVC washer, blue
101.011.048
G
Plastic lock (seal)
303.625.007
H
Complete wire feed unit: Drive plate and motor/encoder
455.042.120
Wire feed motor 110 W, 42 V solo with encoder SE22-150
455.042.500
Wire feed roller 0.8/1.0 for steel
455.037.001
Wire feed roller 1.0/1.2 for steel
455.037.002
Wire feed roller 1.0/1.2 for aluminium
455.037.003
I
Solenoid valve DN 2.5/42 V G 1/8
465.018.009
J
Connection plate for internal connection
715.042.041
K
Current connection plate
703.011.006
L
Control board MC-R
600.044.045
M
Gas test trigger
441.507.009
N
Guide castor D75 × 22 mm
301.075.007
O
Case holder
715.042.014
P
Wire-holding arbor
306.050.001
Q
Insulating flange for central connection socket
455.042.011
R
Left flap DVK3 – 2010
715.042.204
S
Plastic handle, small
05.044.002
Torx screw PT60
271.060.001
T
Protective glass pane, small handles
705.042.260
U
Handle, plastic part
305.235.002
Handle tube DVK3 – 2010
715.042.220
Summary of Contents for inoMIG 350
Page 51: ...inoMIG 350 400 500 21 Schaltpläne BA 0014 2020 10 15 DE 51 Abb 27 Maschine mit Koffer ...
Page 52: ...DE 52 BA 0014 2020 10 15 21 Schaltpläne inoMIG 350 400 500 Abb 28 Kompakt Maschine mit Koffer ...
Page 55: ...inoMIG 350 400 500 Notizen BA 0014 2020 10 15 DE 55 Notizen ...
Page 105: ...inoMIG 350 400 500 21 Circuit diagrams BA 0014 2020 06 05 EN 51 Fig 27 Machine with case ...
Page 109: ...inoMIG 350 400 500 Notes BA 0014 2020 06 05 EN 55 Notes ...
Page 110: ...EN 56 BA 0014 2020 06 05 Notes inoMIG 350 400 500 Notes ...
Page 111: ...inoMIG 350 400 500 Notes BA 0014 2020 06 05 EN 57 Notes ...