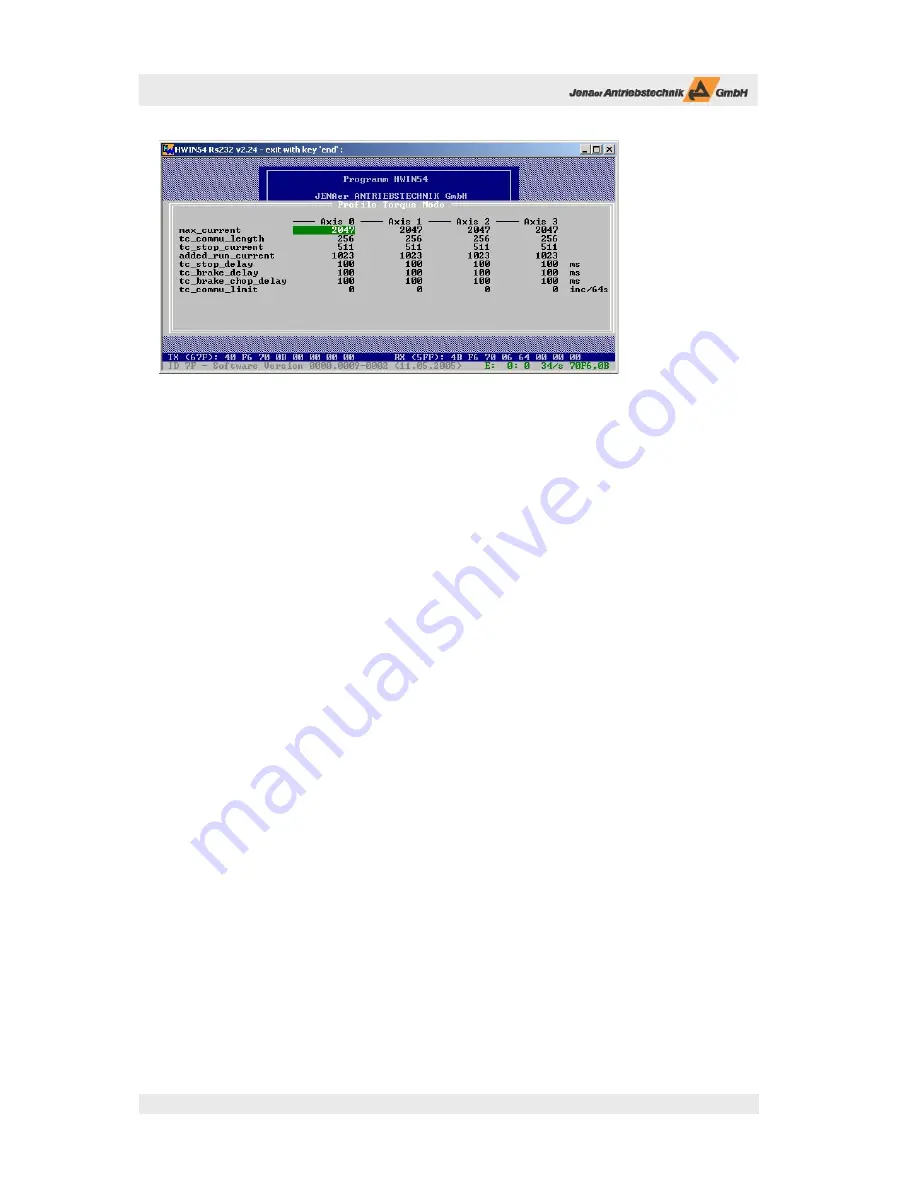
User Manual ECOSTEP®54
28
Subject to change without notice!
Fig. 7.2: Parameter settings for motor and holding brake „Profile Torque Mode“ (F7)
tc_commu_length: step resolution per motor pole -> please take from motor data sheet
(Example: step resolution 256 at 50-pole motor results in 12800 steps/resolution).
max_current: maximum motor current -> please take from motor data sheet.
tc_stop_current: phase current at standstill -> please take from motor data sheet.
added_run_current: run current eff ective in addition to the phase current at standstill
-> please take from the motor data sheet.
Note:
Th e specifi cation of all current values is scaled to the maximum phase current the
ECOSTEP54 can provide per motor output. Th is current amounts to 2.5 A und corresponds
to the value 2047. Th us, the value to be specifi ed is calculated as follows:
current value from data sheet [A]
value =
——————————————
.
2047
2,5 A
tc_stop_delay: Delay [in ms] switchover from run current to stop current
tc_brake_delay: Delay [in ms] holding brake release aft er motor current release
tc_brake_chop_delay: Delay [in ms] holding brake voltage reduction aft er holding brake re-
lease
tc_commu_limit: Speed value at which switching from sine to rectangular commutation takes
place. By switching from sine to rectangular commutation an increase of the torque value is
achieved, because at rectangular commutation the motor characteristic can be fully utilized.
Unit is inc/64s. At the value 0 sine commutation is activated. Th e value to be specifi ed is cal-
culated as follows:
speed [in rpm]
value =
————————
.
12800 inc/rev
.
64
60 s
Note:
Th e resulting motor current is limited to max_current in any case, even if the sum of
tc_stop_current and added_run_current exceeds the max_current value.