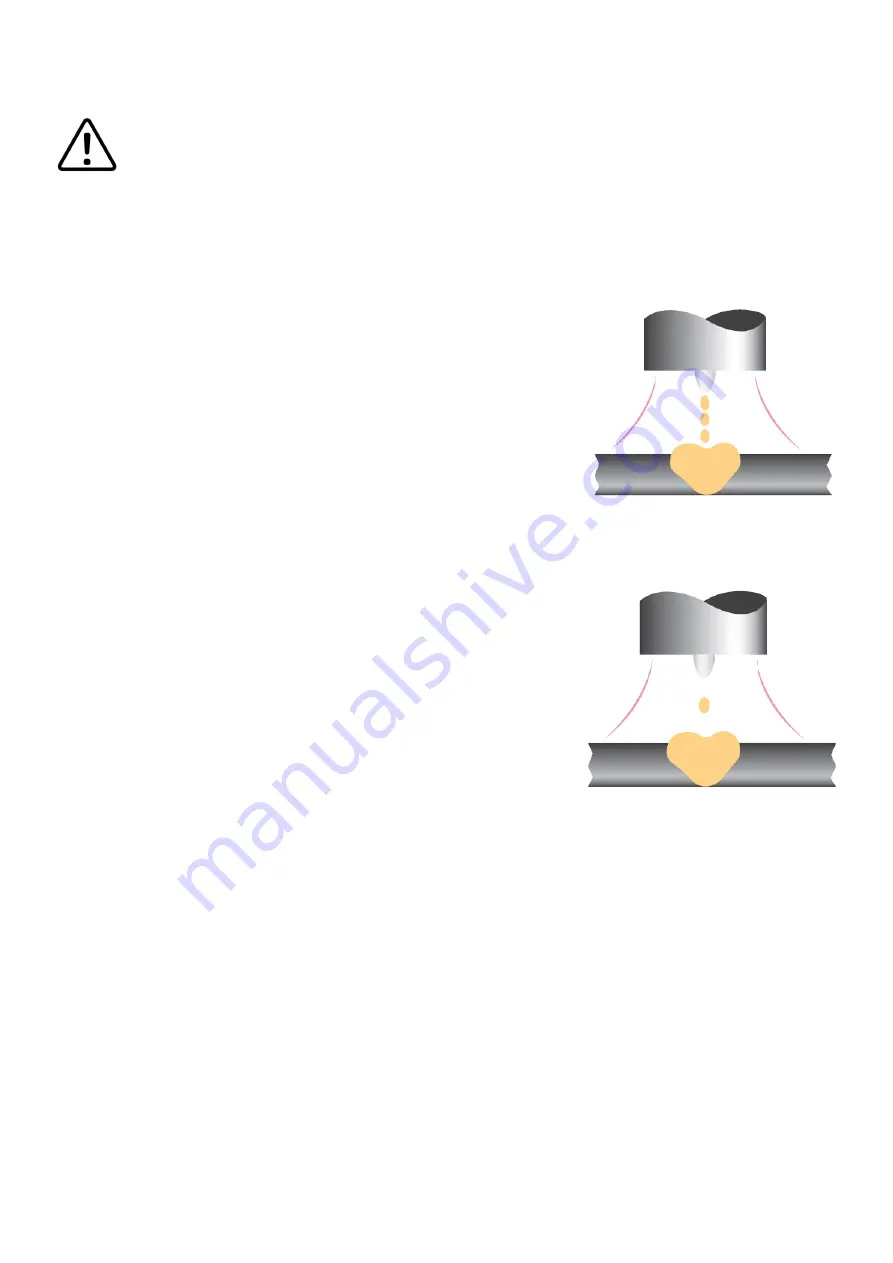
42
GUIDE TO MIG/MAG WELDING
Before starting any welding activity ensure that you have suitable eye protection and
protective clothing. Also take the necessary steps to protect any persons within the welding
area.
Modes of Transfer
Spray Arc Mode
The Spray arc mode is used with high voltage and current. Metal is projected in the form of a fine spray
of molten droplets of the electrode, propelled across the arc to the
work piece by an electromagnetic force without the wire touching the
weld pool.
Its advantages include high deposition rates, good penetration, strong
fusion, excellent weld appearance with little spatter as no short circuits
are occurring.
The disadvantages of the spray arc mode are mainly due to the high
heat input which can cause problems on thinner material and the
limited range of welding positions where the mode can be used.
Generally, the minimum thickness to be welded will be around 6mm.
Pulsed Arc Mode
Pulsed MIG is an advanced form of welding that takes the best of all the other forms of transfer while
minimizing or eliminating their disadvantages.
Unlike short circuit, pulsed MIG does not create spatter or run the risk
of cold lapping. The welding positions in pulsed MIG are not limited as
they are with globular or spray and its wire use is definitely more
efficient. By cooling off the spray arc process, pulsed MIG is able to
expand its welding range and its lower heat input does not encounter
the problems on thinner materials.
In basic terms, pulsed MIG is a transfer method where material is
transferred between the electrode and the weld puddle in controlled
droplet form. This is achieved by controlling the electrical output of the
welding machine using the latest control technologies.
The pulsed MIG process works by forming one droplet of molten metal at the end of the wire electrode
per pulse. When ready the pulse of current is used to propel that one droplet across the arc and into the
puddle.
Welding Mode
-
Synergic
When a welding machine is referred to as synergic it means that when a single setting is adjusted
(most commonly voltage or material thickness) other settings
like current or wire speed
also change.
There are current and voltage settings for all wire types, wire diameters and shielding gases.
The same current settings will have different wire feed speeds, workpiece material thickness and synergic
voltages for different wire diameters.
After setting the current or wire feed speed and workpiece thickness, the system will have predetermined
settings via it
’
s software to match the welding voltage and the other welding parameters.
After choosing
“
synergic
”,
the machine panel
’
s left display will show preset current (wire feed speed or
workpiece thickness dependent on the parameter selected). The right display will show the preset volt-
age.
The wire feeder control panel left display will show preset current and right display will show preset arc
length. Both wire feed unit controls can both set current and voltage. Standard arc length is
“0”;
adjust-
ment is based on the synergic voltage plus or minus 3.0V.
Summary of Contents for EVO 2.0 EM-200CT
Page 1: ...1 ...
Page 74: ...74 UKCA Declaration of Conformity ...
Page 75: ...75 EC DECLARATION OF CONFORMITY ...
Page 77: ...77 SCHEMATIC ...
Page 80: ...80 ...