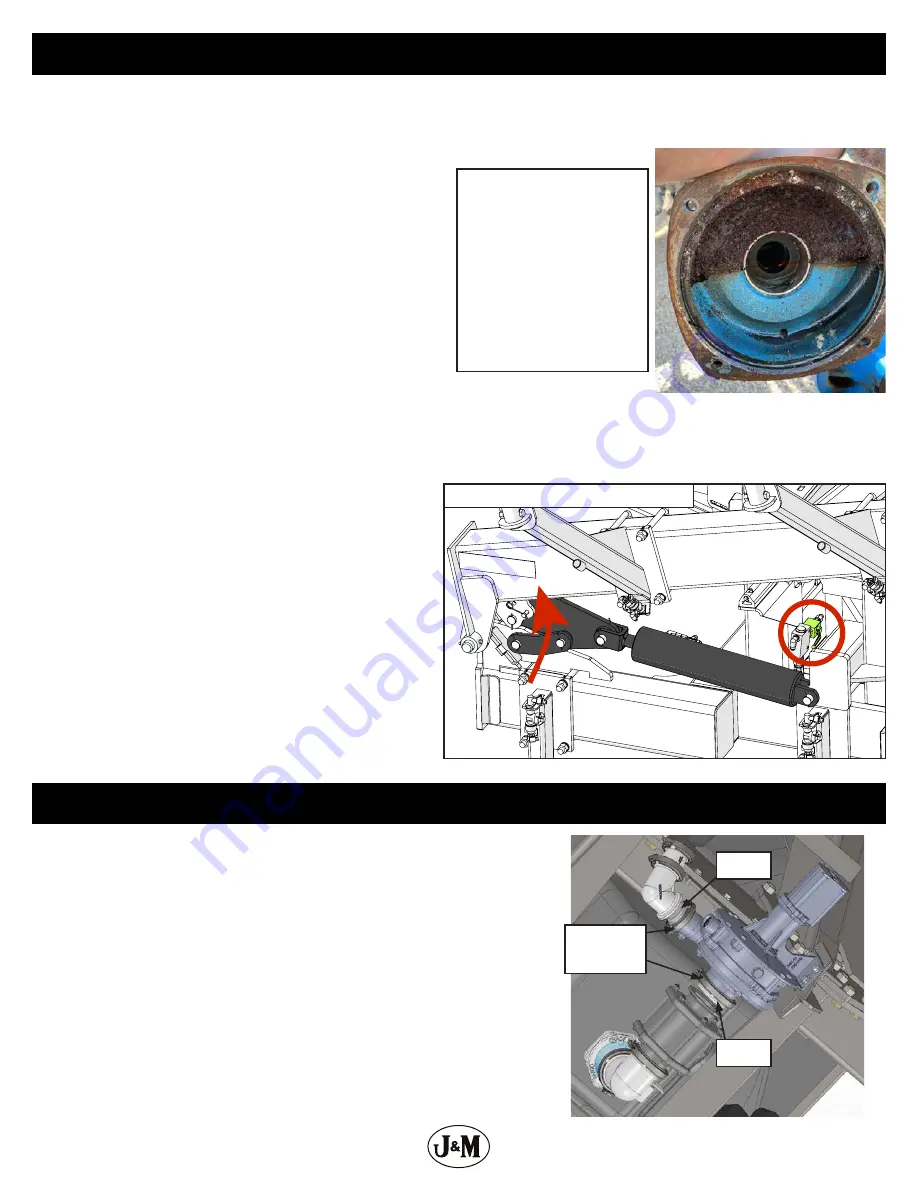
25
Removing Pump Safety Plugs
To prolong the life of your NitroGro applicator, hook the applicator to a tractor, unfold it, and perform the following before placing the
implement in storage:
1. Pressure wash the NitroGro applicator to remove dirt and
debris that may cause rusting.
2. Repaint any areas where the paint has been chipped,
scratched or worn away.
3. Coat all earth-moving surfaces with a suitable rust
preventative.
4. Inspect for damaged or worn parts and replace before next
use. Examine all hydraulic hoses and fittings for wear and
replace or tighten as necessary.
5. Grease coulter hubs.
6. Replace all worn, torn, or faded decals and reflectors.
7. Flush all fertilizer from the system and winterize the applicator
if kept in cold storage.
IMPORTANT - To winterize your NitroGro drain the tank and all fertilizer hoses. Once the system is drained add
approximately 50 gallons of RV antifreeze. Run the antifreeze thru the strainer, valves, check valves, and orifices until
antifreeze comes out of all knives/orifices.
8. Cover flow monitors from the sunlight. If flow monitors are
exposed to the sun for a long period of time they will turn
cloudy and become difficult to see through.
9. Store the implement inside and sheltered from inclement
weather on an area that is dry, level, and clear of debris.
10. Fold up applicator and unhook from tractor.
11. When not in use, lock the stub wing in place by turning the
shut-off valve off on the stub wings. This will keep the stub
wings from unfolding when temperatures fluctuate and
cause thermal expansion in the hydraulic system.
Storage
Do NOT use anything
except RV antifreeze
to winterize.
Using anything
else can cause
severe damage to
fertilizer distribution
components and will
VOID warranty.
Loosen the stainless clamps shown below and remove the safety plugs. Then, attach
the pump fittings using the stainless clamp, ensuring the gasket is seated correctly
between the pump and pump fittings. Failing to remove these plugs can cause the
pump to run dry and cause damage. Once the pump safety plugs are removed,
the applicator will need to be winterized before freezing temperatures occur. See
“Storage” on page 25.
Plugs
Plugs
Stainless
Clamps
Shut-off valve on Stub wing
Summary of Contents for 6018
Page 2: ...2...
Page 12: ...12 NitroGro Components...