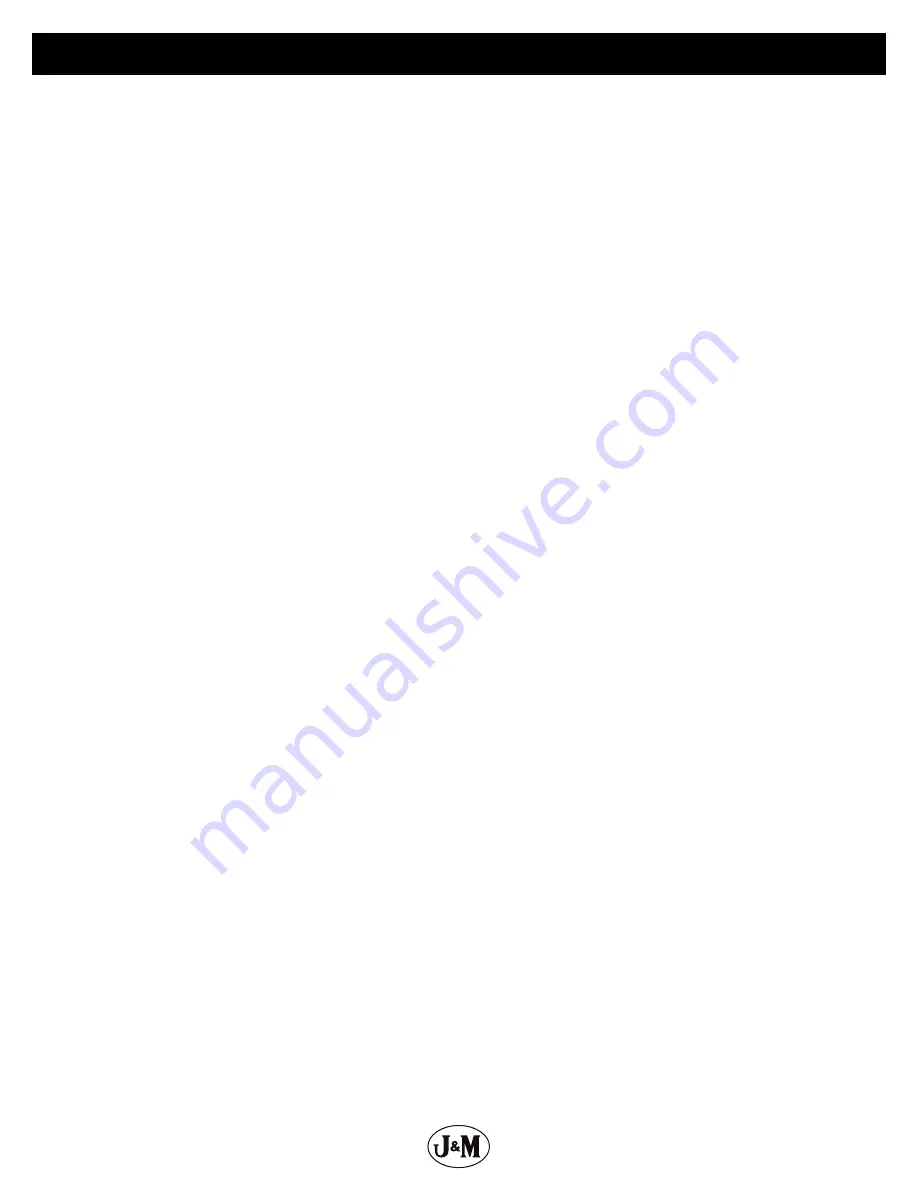
4
TO THE DEALER
Read manual instructions and safety rules. Make sure all items on the Dealer’s Pre-Delivery and Delivery Check Lists are completed
before releasing equipment to the owner.
The dealer must complete the Warranty Registration found on the Dealer Portal website located at dealer.jm-inc.com and return it to J&M
Mfg. Co., Inc. at the address indicated on the form. Warranty claims will be denied if the Warranty Registration has not been submitted.
EXPRESS WARRANTY:
J&M Mfg. Co., Inc. warrants against defects in construction or materials for a period of ONE year. We reserve the right to inspect and
decide whether material or construction was faulty or whether abuse or accident voids our guarantee.
Warranty service must be performed by a dealer or service center authorized by J&M Mfg. Co., Inc. to sell and/or service the type of
product involved, which will use only new or remanufactured parts or components furnished by J&M Mfg. Co., Inc. Warranty service will
be performed without charge to the purchaser for parts or labor based on the Warranty Labor Times schedule. Under no circumstance
will allowable labor times extend beyond the maximum hours indicated in the Warranty Labor Times schedule for each warranty
procedure. The purchaser will be responsible, however, for any service call and/or transportation of the product to and from the dealer
or service center’s place of business, for any premium charged for overtime labor requested by the purchaser, and for any service and/or
maintenance not directly related to any defect covered under the warranty. Costs associated with equipment rental, product down time,
or product disposal are not warrantable and will not be accepted under any circumstance.
Each warranty term begins on the date of product delivery to the purchaser. Under no circumstance will warranty be approved unless (i)
the product warranty registration card has been properly completed and submitted to the equipment manufacturer, and (ii) a warranty
authorization number has been issued by the equipment manufacturer. This Warranty is effective only if the warranty registration card is
returned within 30 days of purchase.
This warranty does not cover a component which fails, malfunctions or is damaged as a result of (i) improper modification or repair, (ii)
accident, abuse or improper use, (iii) improper or insufficient maintenance, or (iv) normal wear or tear. This warranty does not cover
products that are previously owned and extends solely to the original purchaser of the product. Should the original purchaser sell or
otherwise transfer this product to a third party, this warranty does not transfer to the third party purchaser in any way. J&M Mfg. Co.,
Inc. makes no Warranty, express or implied, with respect to tires or other parts or accessories not manufactured by J&M Mfg. Co., Inc.
Warranties for these items, if any, are provided separately by their respective manufacturers.
THIS WARRANTY IS EXPRESSLY IN LIEU OF ALL OTHER WARRANTIES OR CONDITIONS, EXPRESS, IMPLIED OR STATUTORY, INCLUDING ANY
IMPLIED WARRANTY OF MERCHANTABILITY OR FITNESS FOR PARTICULAR PURPOSE.
In no event shall J&M Mfg. Co., Inc. be liable for special, direct, incidental or consequential damages of any kind. The exclusive remedy
under this Warranty shall be repair or replacement of the defective component at J&M Mfg. Co., Inc’s. option. This is the entire agreement
between J&M Mfg. Co., Inc. and the Owner about warranty and no J&M Mfg. Co., Inc. employee or dealer is authorized to make any
additional warranty on behalf of J&M Mfg. Co., Inc.
The manufacturer reserves the right to make product design and material changes at any time without notice. They shall not incur any
obligation or liability to incorporate such changes and improvements in products previously sold to any customer, nor shall they be
obligated or liable for the replacement of previously sold products with products or parts incorporating such changes.
SERVICE:
The equipment you have purchased has been carefully manufactured to provide dependable and satisfactory use. Like all mechanical
products, it will require cleaning and maintenance. Lubricate the unit as specified. Observe all safety information in this manual and
safety signs on the equipment.
For service, your authorized J&M dealer has trained mechanics, genuine J&M service parts, and the necessary tools and equipment to
handle all your needs.
Use only genuine J&M service parts. Substitute parts may void warranty and may not meet standards required for safety and satisfactory
operation. Record the model number and serial number of your equipment in the spaces provided:
Model No:
6018 or 6026 NitroGro Applicator
Serial No:
________________________
Date of Purchase:
____________
Purchased From:
________________________________________________________________________________
Provide this information to your dealer to obtain correct repair parts.
To The Dealer
Summary of Contents for 6018
Page 2: ...2...
Page 12: ...12 NitroGro Components...