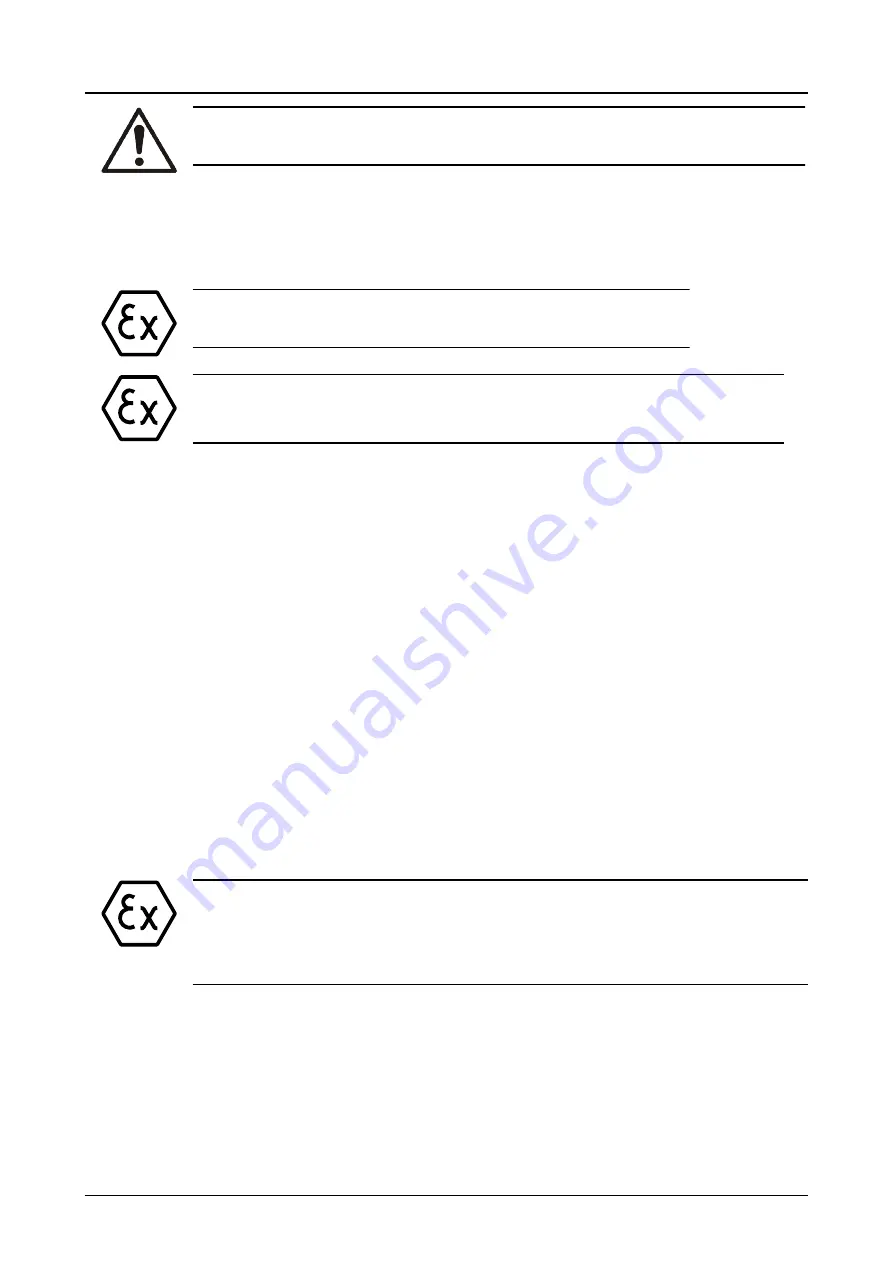
WARNUNG:
Operation of the unit without proper lubrication will cause bearing failure and pump seizure.
3.
Alignment - As described in the Alignment section, alignment is normally built-in and need not
be rechecked.
4.
Stuffing Box - Pumps are shipped without packing, lantern ring or split gland installed. These
are included with the box of fittings shipped with the pump and must be installed before start-
up.
WARNUNG:
Packed stuffing boxes are not allowed in an ATEX classified environment.
WARNUNG:
The mechanical seal used in an ATEX classified environment must be properly certified.
1.
Packing - Stuffing box packing, lantern ring and gland are in the box of fittings sup-
plied with the pump. Install 3 rings of packing, the two piece lantern ring (notched si-
des facing), 2 more rings of packing and the gland. Twist rings sideways instead of
straight out when putting them on the shaft to avoid damaging them. Seat each ring
firmly as it is installed, and stagger the joints 90°. Gland should be drawn up only fin-
ger tight.
Packing must not run dry. If the pumped liquid is clean, gland leakage of 40-60 drops
per minute is satisfactory. If the liquid is dirty, connect a clean liquid flush to the lan-
tern ring connection to keep solids out of the packing.
Occasionally, the stuffing box is below atmospheric pressure (suction under vacuum,
etc.). Under these conditions, supply sealing liquid through a line from the discharge
of the pump to the lantern ring connection. Leakage from the box can be piped away
through the ½ inch drain connection in the casing.
2.
Mechanical Seals - When mechanical seals are supplied, they are installed in the
pump. Mechanical seals must not run dry, or in abrasives. Connect recirculation, flush
and/or cooling flows as required, following instructions on the seal print supplied for
the order.
5.
Stuffing Box Lubrication/Cooling - Check to be sure that any required auxiliary piping is instal-
led and functioning. If cooling and/or flushing from an outside source is being used, establish
these flows.
6.
Check Impeller Clearance -
WARNUNG:
The impeller clearance setting procedure must be followed. Improperly setting the clea-
rance or not following any of the proper procedures can result in sparks, unexpected heat
generation and equipment damage.
Prior to starting the pump, the impeller clearance must be checked. The pump efficiency is
maintained when the proper impeller clearance is set. The optimum hydraulic performance is
attained by setting the impeller front clearance at the factory to predetermined limits which
are consistent with service conditions.
The maximum impeller setting should not be set more than .005 inch | 0.13 above values in
the table below or significant performance degredation will result.
4.1 Preparation for Startup
3996 Installation, Operation and Maintenance Instructions
25