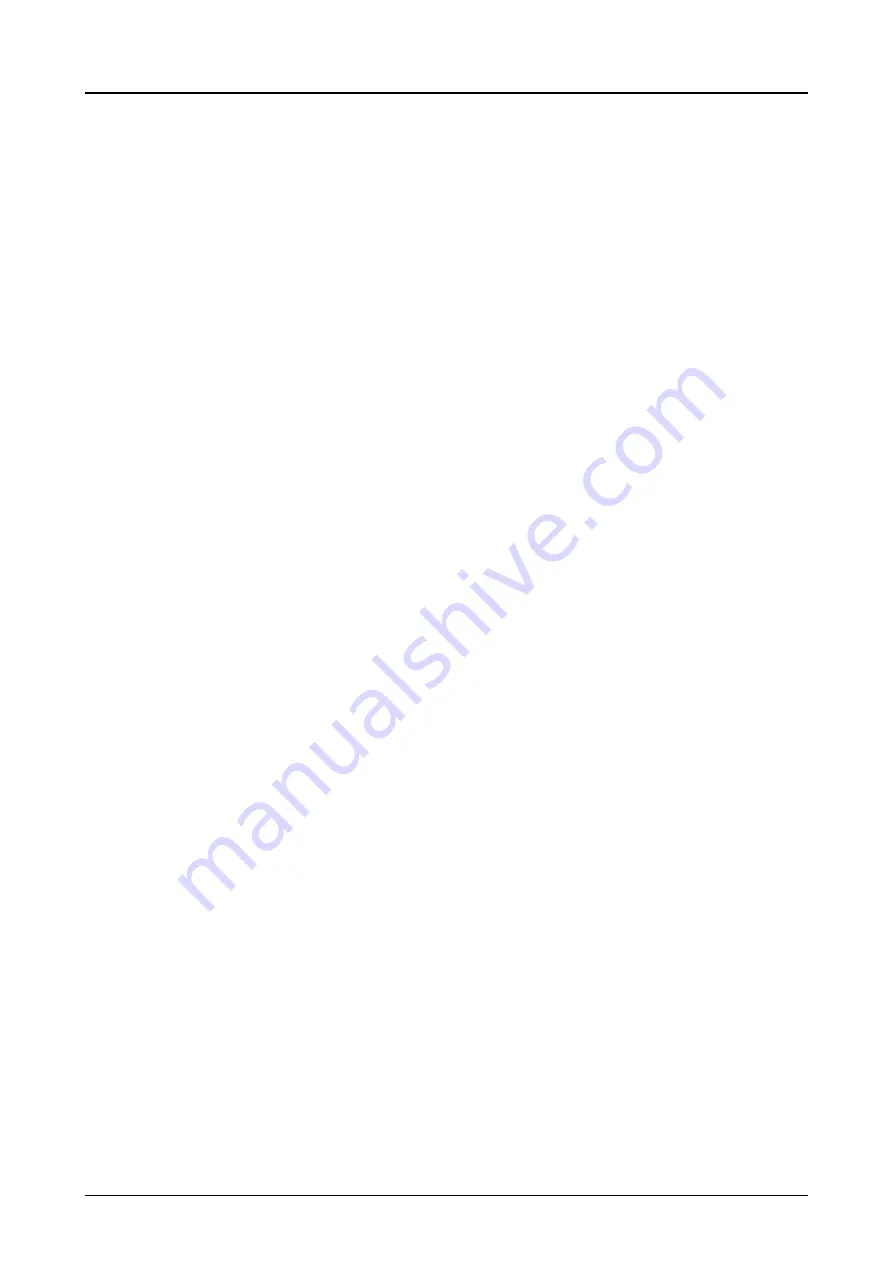
5.
The size of entrance from supply should be one (1) or two (2) sizes larger than the suction
pipe.
6.
The suction pipe must be adequately submerged below the liquid surface to prevent vortices
and air entrainment at the supply.
3.3 Discharge Piping
Properly designed and installed discharge piping is a necessity for trouble-free pump operation. Di-
scharge piping should be flushed BEFORE connection to the pump.
1.
Isolation and check valves should be installed in discharge line. Locate the check valve betwe-
en isolation valve and pump; this will permit inspection of the check valve. The isolation valve is
required for priming, regulation of flow, and for inspection and maintenance of pump. The check
valve prevents pump or seal damage due to reverse flow through the pump when the driver is
turned off.
2.
Increasers, if used, should be placed between pump and check valves.
3.
Cushioning devices should be used to protect the pump from surges and water hammer if
quick-closing valves are installed in system.
3.3.1 Bypass Piping
Systems that require operation at reduced flows for prolonged periods should be provided with a by-
pass line connected from the discharge side (before any valves) to the source of suction.
A minimum flow orifice can be sized and installed in bypass line to preclude bypassing excessive
flows. Consult nearest sales office or factory for assistance in sizing orifice.
An automatic recirculation control valve and/or solenoid operated valve should be considered if a
constant bypass (i.e. orifice) is not possible.
3.3.2 Auxiliary Piping
Auxiliary piping may be required for seal chamber cover cooling, mechanical seal flush or other spe-
cial features supplied with the pump. Consult pump data sheet for specific auxiliary piping recom-
mendations.
If seal chamber cover cooling is required, follow guidelines listed below.
1.
Flows of 4 l/min. (1 GPM) will generally satisfy cooling requirements.
2.
Cooling water pressure should not exceed 7.0 kg/cm2 (100 psig).
3.3.3 Final piping check
After connecting the piping to pump:
1.
Rotate shaft several times by hand to be sure that there is no binding and all parts are free.
2.
Check alignment, per alignment criteria outlined previously, to determine if pipe strain has affec-
ted alignment. If pipe strain exists, correct piping.
3.4 Alignment
Alignment between pump and motor is built in by use of machined lock fit between the C-face motor
and motor support. No further alignment is normally required.
There is one exception to this. The Model 3196 horizontal ANSI pump bearing frame can be used in
the Model 3996. This frame may be used in emergencies or when it is desired to minimize inventory.
The Model 3196 frame will not give built-in alignment, and normal alignment procedures must be per-
formed. The Model 3196 frame can be identified by the foot and cooling jacket on the side.
3.3 Discharge Piping
3996 Installation, Operation and Maintenance Instructions
21