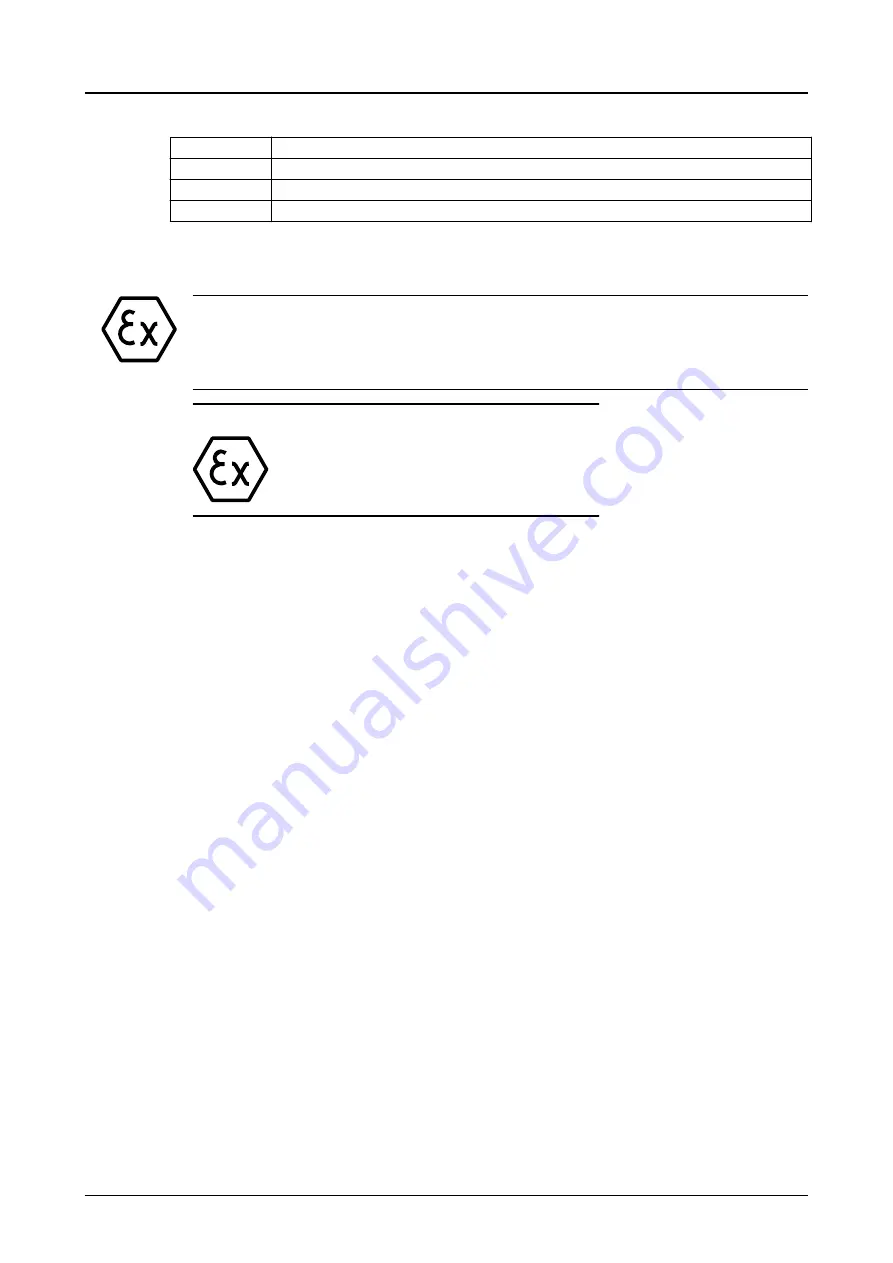
Tabellennummer 2: Piping Flange Alignment
Type
Criteria
Axial
Flange gasket thickness ± 0.8 mm | 0.03 in.
Parallel
0.001 mm/mm | 0.001 in./in. of flange diameter to a maximum of 0.8 mm | 0.03 in.
Concentric
Flange bolts should easily install by hand.
6.
Bottom of casing should be supported by a solid foundation or casing feet should be used.
3.2.1 Suction Piping
WARNUNG:
NPSHA must always exceed NPSHR as shown on Goulds performance curves received
with order. (Reference Hydraulic Institute for NPSH and pipe friction values needed to eva-
luate suction piping).
HINWEIS:
Pump must never be throttled from suction side.
Properly designed and installed suction piping is a necessity for trouble-free pump operation. Suction
piping should be flushed BEFORE connection to the pump.
1.
Use of elbows close to the pump suction flange should be avoided. There should be a mini-
mum of two (2) pipe diameters of straight pipe [five (5) pipe diameters is preferred] between
the elbow and suction inlet. Where used, elbows should be long radius.
2.
Use suction pipe one (1) or two (2) sizes larger than the pump suction, with a reducer at the
suction flange. Suction piping should never be of smaller diameter than the pump suction.
3.
Reducers, if used, should be eccentric and located at the pump suction flange with sloping
side down.
4.
A suction screen should be installed prior to initial start-up and when suction system has be-
en opened for work. The screen should be of the cone type with a net area equal to at least
three (3) times the cross sectional area of the suction pipe. The mesh of the screen should be
sized to prevent particles larger than 1.6 mm (1/16 in.) from entering the pump and should be
installed in a spool piece to allow removal for cleaning. The screen should remain in the sys-
tem until periodic inspection shows system is clean.
5.
Separate suction lines are recommended when more than one pump is operating from the
same source of supply.
Suction Lift Conditions
1.
Suction pipe must be free from air pockets.
2.
Suction piping must slope upwards to pump.
3.
All joints must be air tight.
4.
A means of priming the pump must be provided.
Suction Head/Flooded Suction Conditions
1.
An isolation valve should be installed in the suction line at least two (2) pipe diameters from
the pump suction to permit closing of the line for pump inspection and maintenance.
2.
Keep suction pipe free from air pockets.
3.
Piping should be level or slope gradually downward from the source of supply.
4.
No portion of the piping should extend below pump suction flange.
3.2 Piping
20
3996 Installation, Operation and Maintenance Instructions