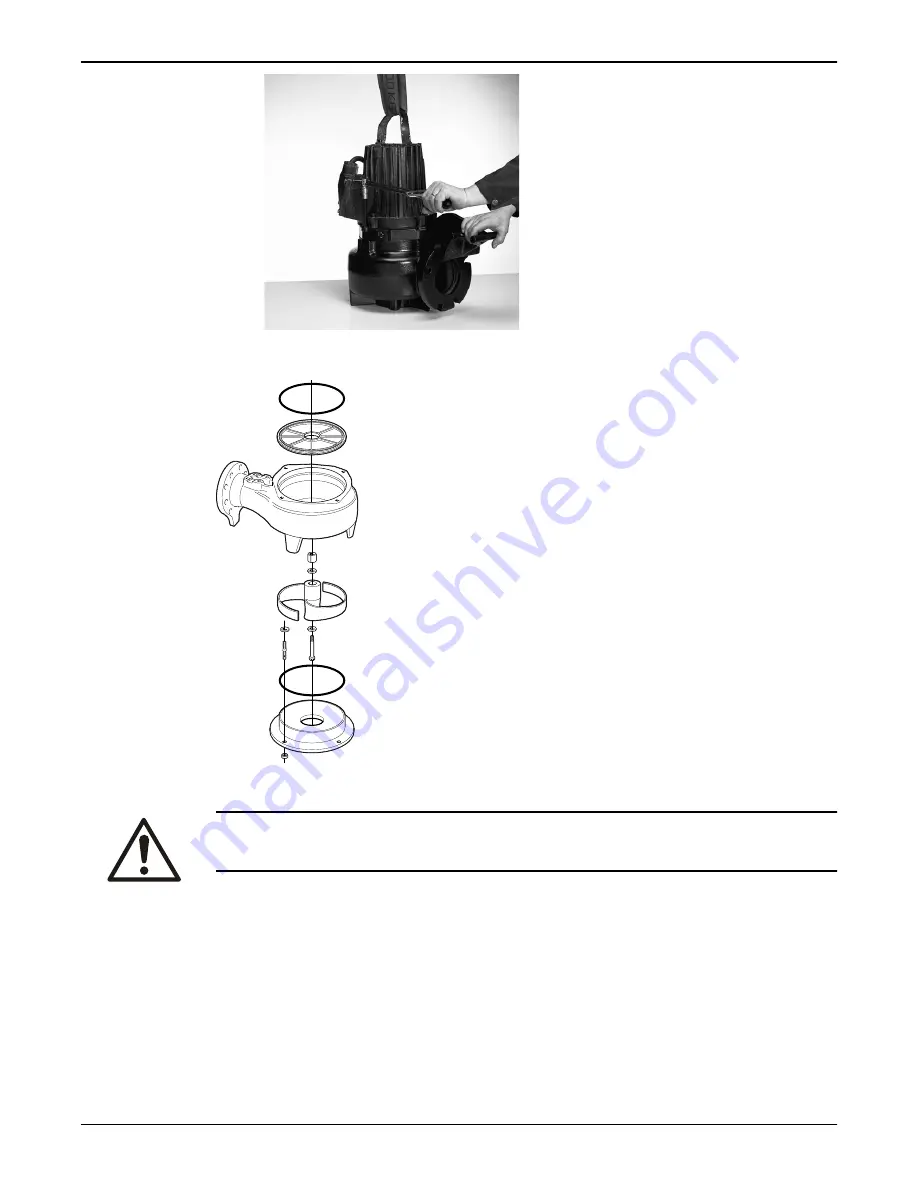
Replace the F-impeller
Remove the F-impeller
CAUTION:
A worn impeller and/or pump housing can have very sharp edges. Wear protective gloves.
1. Remove the suction cover.
2. Remove the impeller screw, the ring, and the washers.
If applicable, use the rod.
Maintenance (Continued)
46
Flygt 3102 Service and Repair Instructions