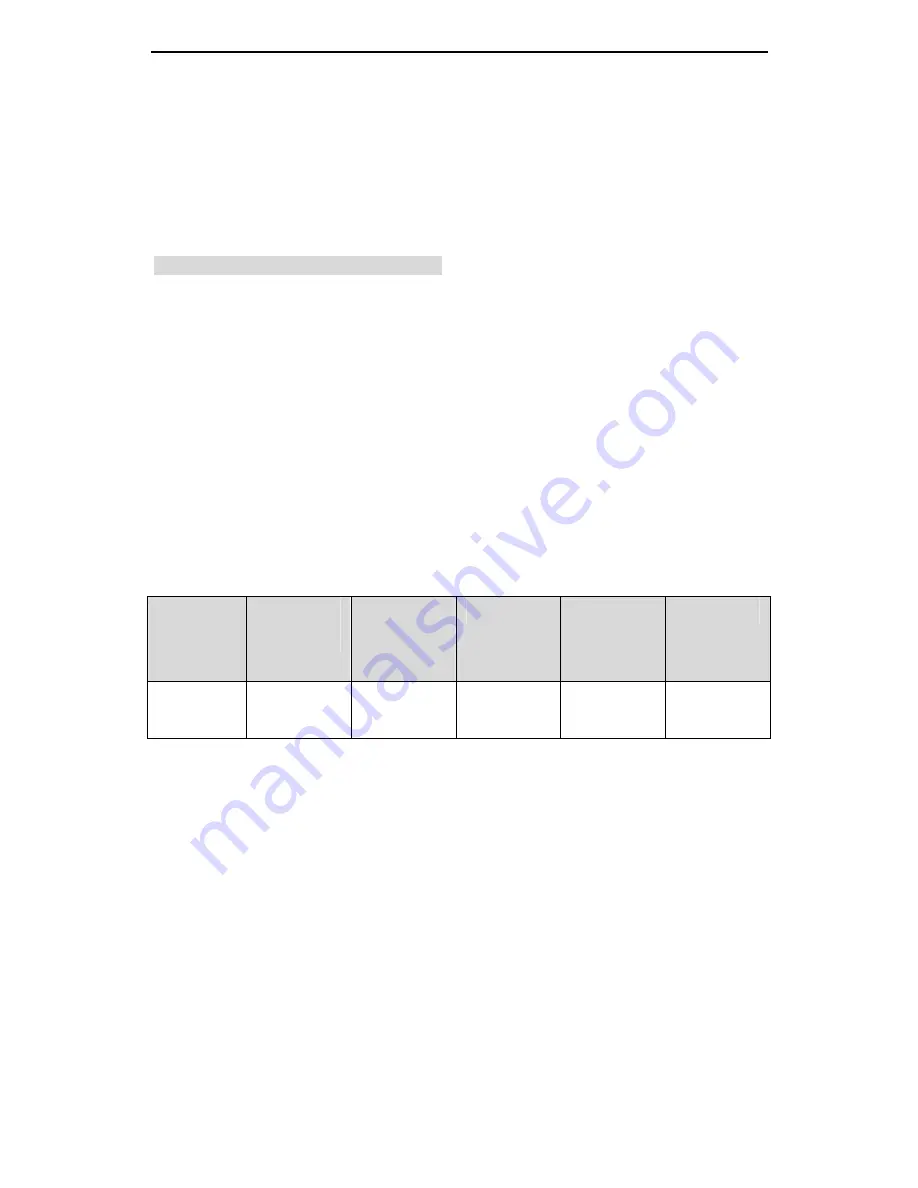
Operation Manual of INVT CHS100 AC Servo Drive 8 Communication Function
110
same communication protocol. The master can communicate with a certain salve, as
well as, send broadcast message to all slaves. For the separately-visiting
inquiry/command of the master, the slave should return a message as the response.
While for the broadcast message, the salve needs not to do so.
8.3.3 Communication Protocol Format
Modbus protocol supports both RTU and ASCII mode. The user can select whatever
they prefer as well as the serial communication parameters, such as, the baud rate and
the checkout means. All the devices on the same Modbus network should select the
same transmission mode and serial parameters during configuring each control
devices.
8.3.3.1 ASCII mode
When the control device is set as ASCII communication mode on the Modbus network,
every 8bit byte in the message is sent as two ASCII characters. The advantage of this
mode is the time interval of byte sending can achieve 1m without mistakes.
Table 8-1: The message frame in ASCII mode
The start
bit
The device
address
The
command
code
Data
LRC
checkout
The tailed
1
character
2
characters
2
characters
n
characters
2
characters
2
characters
As table 1 showed, in the message of ASCII mode, the start bit is “:” (ASCII code 3AH)
and the tailed is the line break (ASCII code 0DH, 0AH). The device on the network is
detecting “:” during the transmission. Each device decodes the next address field when
receiving a “:” to estimate the owner. The device corresponds to the address field
continues to receive other field until the line break appears. Except for the start bit and
the tailed, the transmitting characters used in other fields are 0…..9, A…..F (hex) and
the ASCII codes are also used to express characters. In the ASCII mode, LRC is used
in the message to check the error.
8.3.3.1 RTU mode
When the control device is set as RTU mode, every 8bit byte in the message frame
includes two 4Bit hex characters.