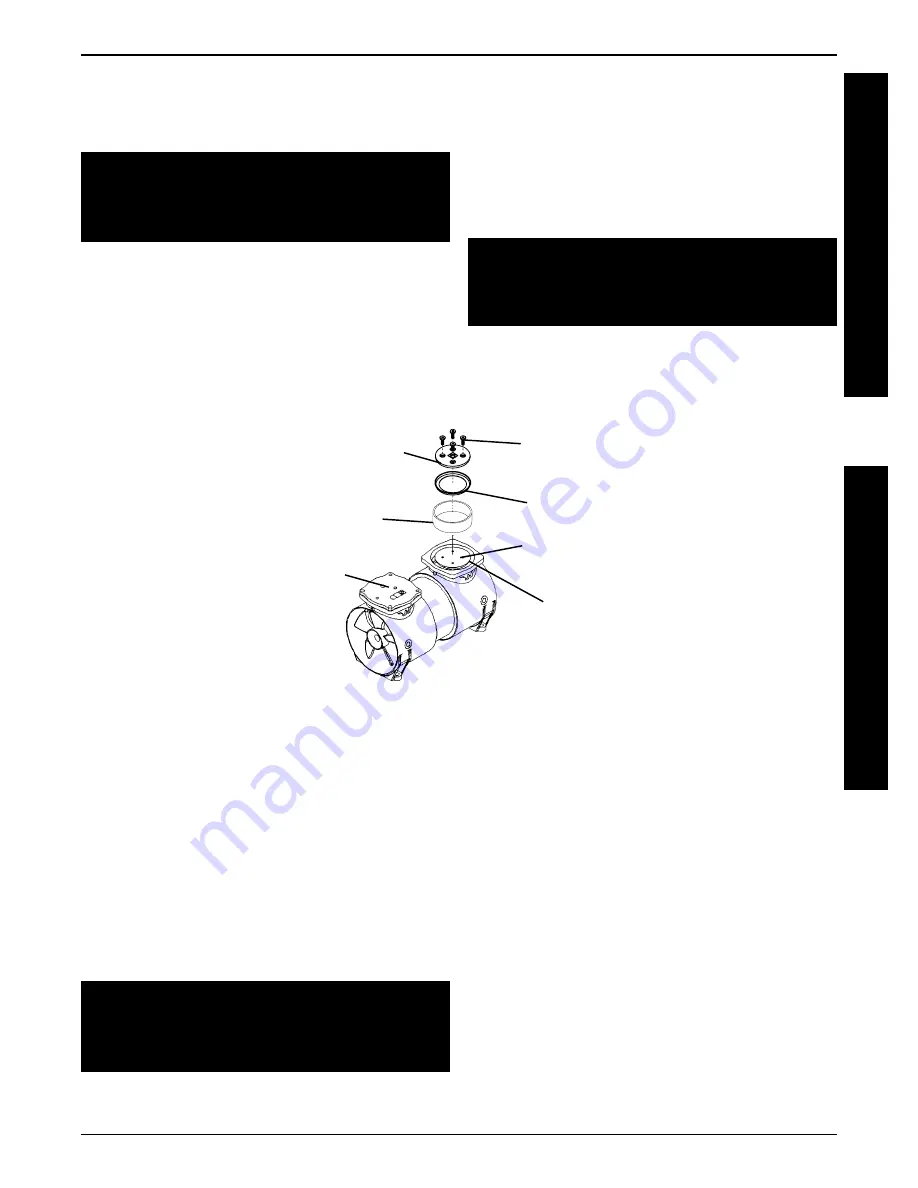
31
P
R
E
V
M
A
I
N
T
E
N
A
N
C
E
5
L
T
R
C
O
M
P
R
E
B
U
I
L
D
PROCEDURE 2 - PREVENTIVE MAINTENANCE (continued)
PREVENTIVE MAINTENANCE
PROCEDURE 2
Installing the New Teflon Rings and Piston
Heads (FIGURE 12)
4. Install and tighten the phillips head screws until
snug to align the Teflon ring with the aluminum
sleeve.
5. Once the Teflon ring is centered properly with the
piston head and aluminum sleeve, torque the
screws to 30 in. lbs.
CAUTION
Piston head MUST be rotated 90
O
when rein-
stalling. This ensures proper wear on the pis-
ton head and will prolong it's life.
1. Place the aluminum sleeve onto its mounting
position on the compressor housing.
2. Rest the new Teflon ring on the aluminum sleeve
and center the ring with the piston head.
3. Install the piston head over the piston ring and
into the aluminum sleeve.
One (1) Piston
Rebuild ONLY
SHOWN for Clarity
Phillips Head
Screws
(4 per Head)
Piston
Teflon Ring
Aluminum Sleeve
Piston Head
Valve Plate
FIGURE 12 - INSTALLING THE NEW TEFLON RINGS AND PISTON HEADS
Mounting Position for
Aluminum Sleeve
CAUTION
DO NOT force aluminum sleeve onto piston. The
Teflon ring may become damaged and
render the piston unusable.
Installing Top and Bottom Flappers (FIGURE
13)
NOTE: Ensure that new valves are facing in the
same direction that the old ones when install-
ing and that they completely cover the compres-
sion opening in the valve plate. Make sure that
no dirt or grease contacts the valves or valve
plates as this may inhibit their ability to open
and close properly and severely reduce the
compressor's ability to adequately compress the
air. Replace the top and bottom valves by doing
one side of the valve plate at a time.
CAUTION
Because of tooling of the valve keepers, ensure
that the word "UP" on the valve keeper is fac-
ing you when installing the valve keepers.
1. Use the small common (flathead) screwdriver
to remove the valve screw securing the valve
restraint, valve keeper, and valve to the top of
the valve plate.
2. Remove the valve screw, valve keeper, and valve
from the bottom side of the valve plate.
3. Reverse STEPS 1-2 to install the NEW top and
bottom valves onto the valve plate.
4. Torque valve screws to 12 in. lbs.
5. Install the head gasket in the compressor head
and the valve plate gasket into the underside of
the valve plate.
6. After the other piston has been rebuilt, install the
valve plates over the aluminum sleeves and rein-
stall the head assembly onto the valve plates not-
ing the markings made when the head assembly
and valve plates were removed.
Summary of Contents for 3LX
Page 69: ...69 NOTES N O T E S ...
Page 70: ...70 NOTES N O T E S ...