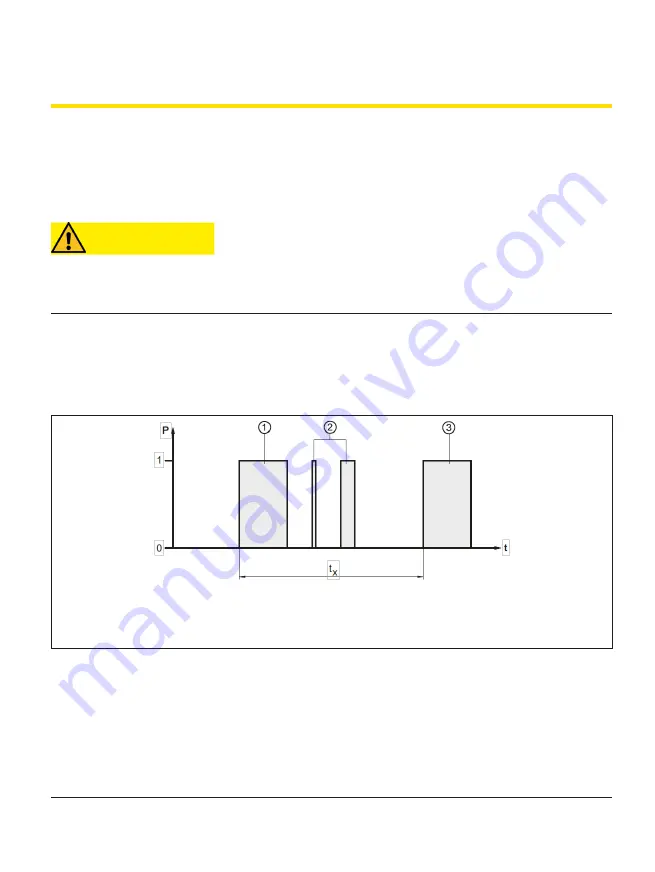
Version 2.0 (04/2019) Online
Translation of the original operating manual
17 von 54
Product information
Temperature protection
If operational conditions mean that the brake chopper is switched on so often that the upper temperature limit of
approx. 90 °C (measured internally) is reached, then the ZoneControl switches off. If temperature protection is active,
this is shown on the LED display. When the ZoneControl has cooled down, the RollerDrive restarts automatically when
a signal is pending.
CAUTION
Unintended start-up of the RollerDrive following the ZoneControl cooling down!
Danger of crushing of limbs and damage to goods!
¾
Ensure that no start signal is pending during the cooling-down process.
Lock period for signal modifications / Debouncing
The external signal inputs, the sensor connections and the DIP switches are protected by the firmware to guarantee
operation in the event of edge-unstable and bouncing input-levels. This means that after a signal status change, there
is a time gap of 20 ms in which no additional status change is accepted. The sample applies to the sensor inputs,
where signal status changes are only processed 50 ms after a signal modification.
1 Signal (with effect) and start of the lock time t
x
2 Signals with no effect, as they lie within the lock time t
x
3 The first signal that has an effect after the lock time t
x
After-run time
Once a package has left the sensor of a zone, then the RollerDrive in this zone continues to run for additional 4
seconds. At the end of 4 seconds, the RollerDrive stops, providing no new package is transferred from the upstream
zone.
This feature provides the following benefits:
• Energy-savings by switching off the RollerDrive if no further packages have to be transported.
• Avoidance of unnecessary start/stop operation if there are no gaps between the packages.