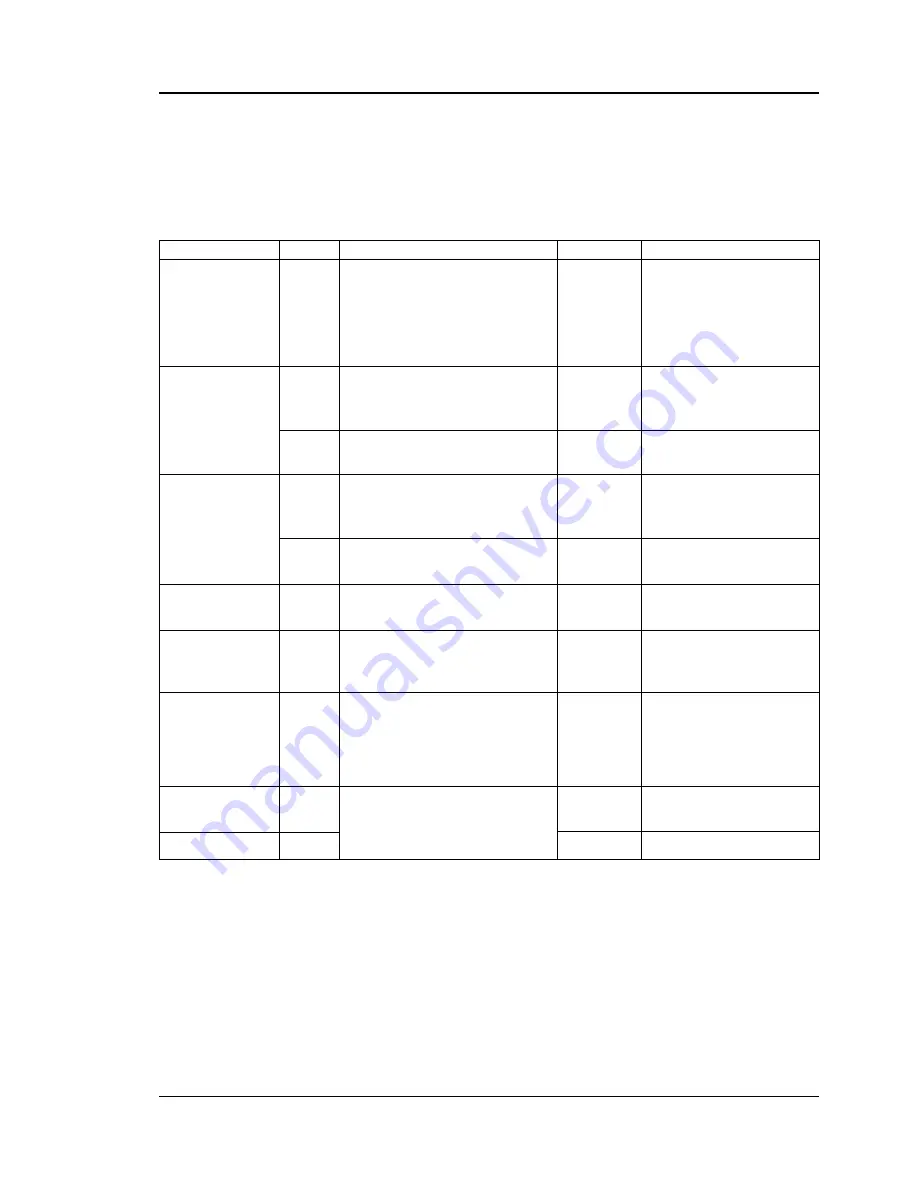
Intermec ColorCoder V4 – Service Manual Ed. 1
246
Chapter 6 Troubleshooting
Error Indication “21”
Cause
Connectors and Wir-
ing
Head Position Sen-
sor 1 (PS8)
Head Position Sen-
sor 2 (PS9)
Head drive shafts,
wires, pulleys
Motor unit
Head motor
Engine 2 PCB
Engine 1 PCB
Step
1
2
3
4
5
6
7
8
9
10
Check Point
Are the connections and wiring of the
following connectors in order?
• Engine 2 PCB: J407, J409
• Head motor: J19
• Head Position Sensor 1: J25
• Head Position Sensor 2: J26
Is the Head Position Sensor 1 (PS8)
properly attached? Is the flag properly
attached?
Is the Head Position Sensor 1 (PS8)
working properly?
Is the Head Position Sensor 2 (PS9)
properly attached? Is the flag properly
attached?
Is the Head Position Sensor 2 (PS9)
working properly?
Are the head drive shafts, wires, and
pulley in order?
Are the motor unit installation and the
gears back lush between the motor and
the PHS holder in order?
Turn OFF the power switch and discon-
nect the head motor (M3) connector.
Is the resistance between the terminals
(orange-blue, red-yellow) of the con-
nectors on the motor side about 3 ohms?
Is the problem corrected when Engine 2
PCB is replaced?
Result
No
No
No
No
No
No
No
No
Yes
No
Corrective Action
Reconnect and rewire the con-
nectors properly.
Reattach Head Position Sensor
1 (PS8) and flag properly.
Replace Head Position Sensor 1
(PS8).
Reattach Head Position Sensor
2 (PS9) and flag properly.
Replace Head Position Sensor 2
(PS9).
Replace the PHS unit.
Correct the motor unit installa-
tion and the gear back lush.
Replace Head Motor (M3).
Finished.
Replace Engine 1 PCB.
6.8 Function Troubleshooting, cont'd
6.8:A Measures to Take Against Malfunctions, cont'd.