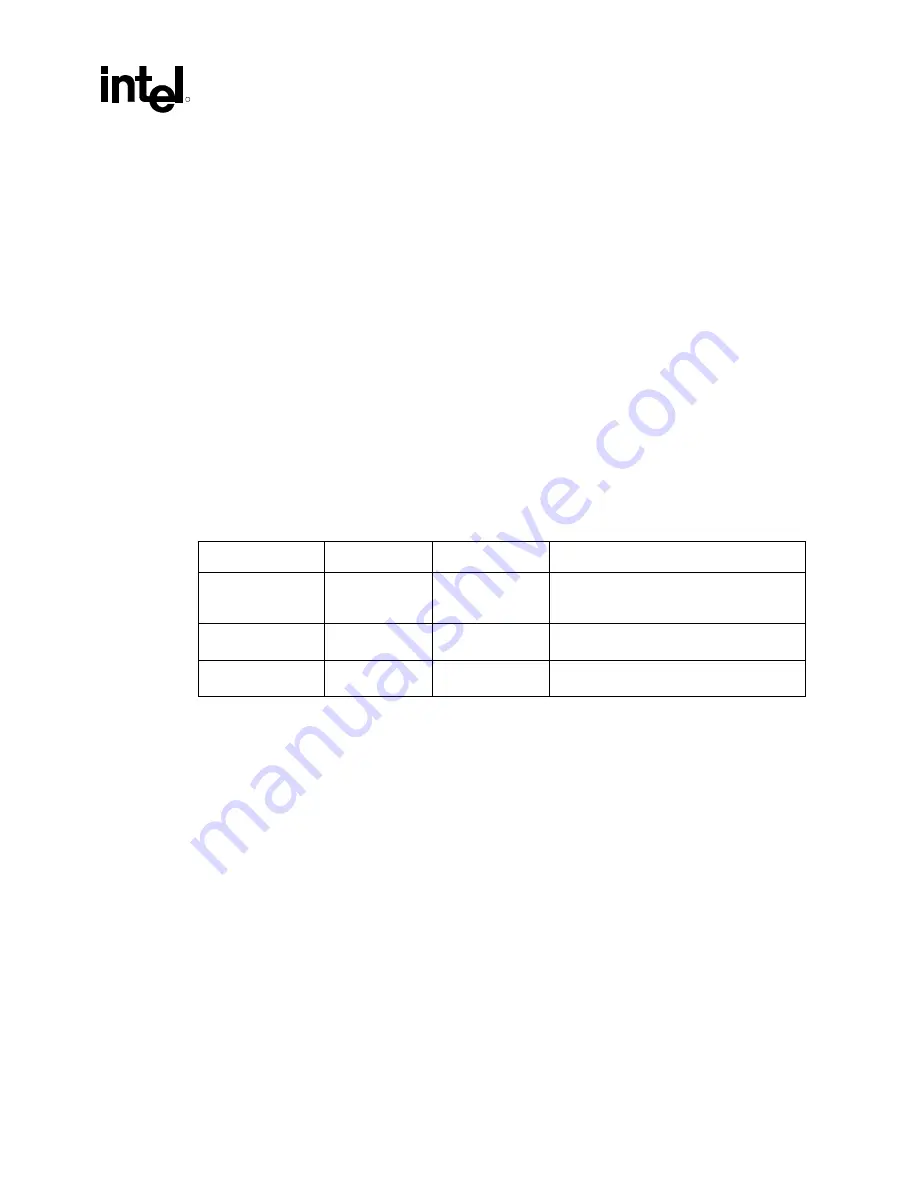
Reference Thermal Solution
R
Intel
®
848P Chipset Thermal Design Guide
23
4.3.1
Alternate WSHS for Non-Rotated MCH
The WSHS can be modified into an alternate configuration for a non-rotated MCH. Customers that
want to develop an alternate design should work with their suppliers and implement the following
recommendations:
•
Create an extrusion die that will create two parallel rails matching the rails shown in the heatsink
drawing (Appendix B, Figure 16), but at a 0° rotation relative to the heatsink. The extruded rails
should use the same width, height, and spacing as shown in the drawing. The tolerances shown
should be replicated in the extrusion.
•
Omit the dado cut from the manufacturing process.
4.3.2
Manufacturing with the WSHS
This section describes manufacturing related considerations for WSHS use in an HVM setting.
4.3.2.1
Assembly Process Settings
Table 6 provides recommended wave solder process settings for installation of the WSHS.
Table 6. Wave Solder Recommended Settings for WSHS
Setting Minimum
Maximum
Notes
Board Temperature
on Pre-heat Region
Exit
90 °C [194 °F]
120 °C [248 °F]
Recommend not exceeding 120 °C
[248 °F] due to flux dry out
Dwell Time
2.1 s
As Required
Not to exceed 160°C [320 °F] board topside
temperature
Solder Bath
Temperature
240 °C [464 °F]
As Required
Not to exceed 160°C [320 °F] board topside
temperature using the minimum dwell time
In addition, the recommended solder type is standard eutectic 63/37 Sn/Pb. No “top hat” plungers
should be used to hold down the WSHS during the wave solder process since it may increase the risk
of heatsink tilt. For best results, the WSHS should be left in a “floating” condition as it passes
through the wave solder.
4.3.2.2 Inspection
Criteria
After the WSHS is installed and exits the wave solder process, it should be visually inspected to
ensure there are no gross tilt issues. Any gross tilt in the WSHS will impact the thermal performance
of the heatsink. The recommended allowable observed tilt is approximately 0.36 mm [0.014 in]
variation between pin gaps on opposite sides of the heatsink (~16% difference in gap, nominal gap is
~2.2 mm [0.086 in]). The pin gap is defined as the distance between the bottom of the heatsink base
and the top of the motherboard. This amount of gap is easily detectable by trained inspectors. Gross
tilt inspection results can allow for closer inspection and measurement of tilt.
To establish the initial wave solder process, a more detailed inspection may be used to confirm the
process is robust and does not induce heatsink tilt. A detailed inspection may include the use of
“feeler” gauges to measure the pin gap more precisely and assess the presence of heatsink tilt. The
recommended allowable tilt can be used as criteria for determining the success of the wave solder
process. Once a successful wave solder process is in place, the manufacturer may choose to use
visual gross tilt inspection in an HVM setting.