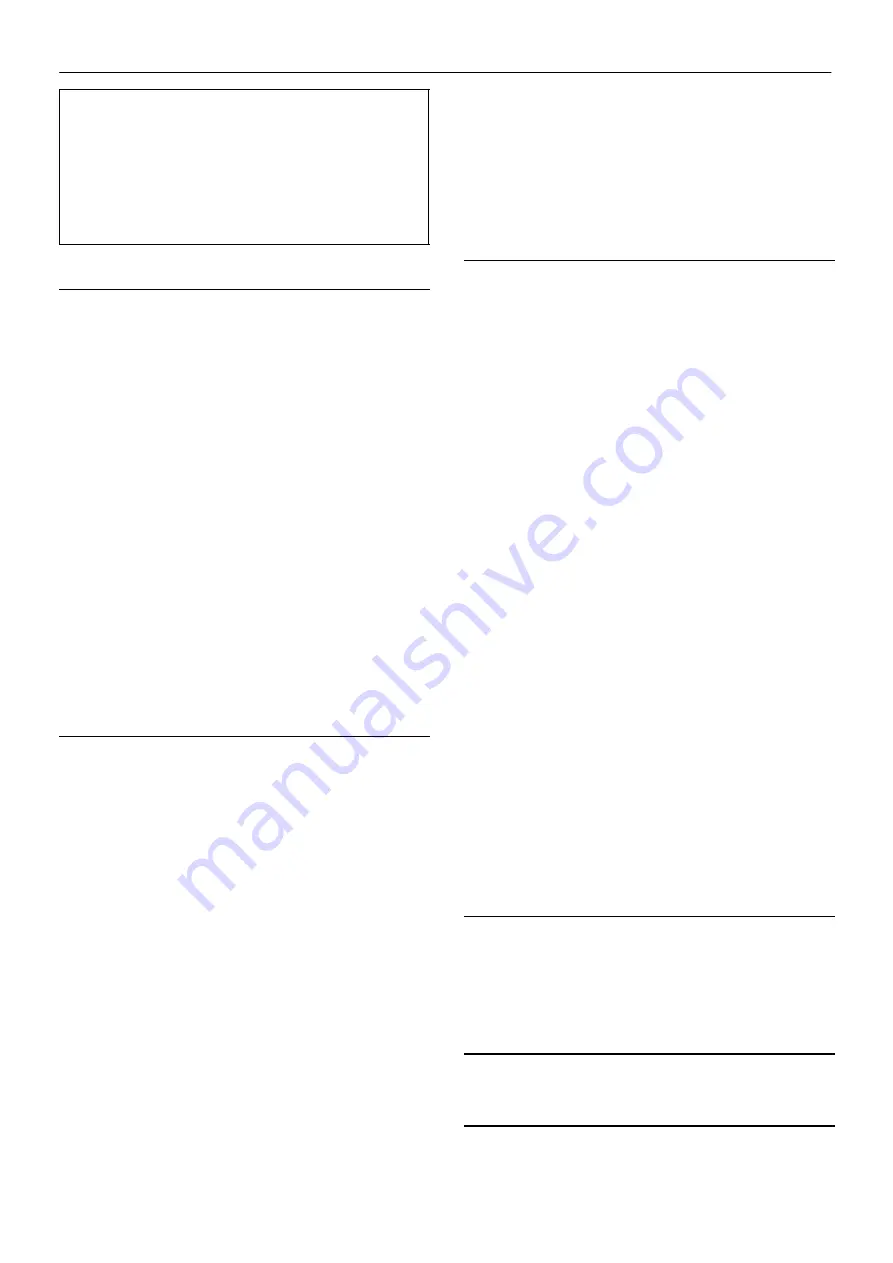
SAFETY
18
HP935, VHP750, MHP825, XHP750, XP1060
WARNINGS
Warnings call attention to instructions which must be followed
precisely to avoid injury or death.
CAUTIONS
Cautions call attention to instructions which must be followed
precisely to avoid damaging the product, process or its surroundings.
NOTES
Notes are used for supplementary information.
General Information
Ensure that the operator reads and understands the decals and
consults the manuals before maintenance or operation.
Ensure that the Operation and Maintenance manual, and the
manual holder, are not removed permanently from the machine.
Ensure that maintenance personnel are adequately trained,
competent and have read the Maintenance Manuals.
Make sure that all protective covers are in place and that the
canopy/doors are closed during operation.
The specification of this machine is such that the machine is not
suitable for use in flammable gas risk areas. If such an application is
required then all local regulations, codes of practice and site rules must
be observed. To ensure that the machine can operate in a safe and
reliable manner, additional equipment such as gas detection, exhaust
spark arrestors, and intake (shut–off) valves may be required,
dependant on local regulations or the degree of risk involved.
A weekly visual check must be made on all fasteners/fixing screws
securing mechanical parts. In particular, safety–related parts such as
coupling hitch, drawbar components, road–wheels, and lifting bail
should be checked for total security.
All components which are loose, damaged or unserviceable, must
be rectified without delay.
Compressed air
Compressed air can be dangerous if incorrectly handled. Before
doing any work on the unit, ensure that all pressure is vented from the
system and that the machine cannot be started accidentally.
Ensure that the machine is operating at the rated pressure and that
the rated pressure is known to all relevant personnel.
All air pressure equipment installed in or connected to the machine
must have safe working pressure ratings of at least the machine rated
pressure.
If more than one compressor is connected to one common
downstream plant, effective check valves and isolation valves must be
fitted and controlled by work procedures, so that one machine cannot
accidently be pressurised / over pressurised by another.
Compressed air must not be used for a direct feed to any form of
breathing apparatus or mask.
The discharged air contains a very small percentage of compressor
lubricating oil and care should be taken to ensure that downstream
equipment is compatible.
If the discharged air is to be ultimately released into a confined
space, adequate ventilation must be provided.
When using compressed air always use appropriate personal
protective equipment.
All pressure containing parts, especially flexible hoses and their
couplings, must be regularly inspected, be free from defects and be
replaced according to the Manual instructions.
Avoid bodily contact with compressed air.
The safety valve located in the separator tank must be checked
periodically for correct operation.
Materials
The following substances may be produced during the operation of
this machine:
.
brake lining dust
.
engine exhaust fumes
AVOID INHALATION
Ensure that adequate ventilation of the cooling system and exhaust
gases is maintained at all times.
The following substances are used in the manufacture of this
machine and may be hazardous to health if used incorrectly:
.
anti–freeze
.
compressor lubricant
.
engine lubricant
.
preservative grease
.
rust preventative
.
diesel fuel
.
battery electrolyte
AVOID INGESTION, SKIN CONTACT AND INHALATION OF
FUMES
Should compressor lubricant come into contact with the eyes, then
irrigate with water for at least 5 minutes.
Should compressor lubricant come into contact with the skin, then
wash off immediately.
Consult a physician if large amounts of compressor lubricant are
ingested.
Consult a physician if compressor lubricant is inhaled.
Never give fluids or induce vomiting if the patient is unconscious or
having convulsions.
Safety data sheets for compressor and engine lubricants should be
obtained from the lubricant supplier.
Battery
Batteries contain corrosive liquid and produce explosive gas. Do
not expose to naked lights. Always wear personal protective clothing
when handling. When starting the machine from a slave battery ensure
that the correct polarity is observed and that connections are secure.
DO NOT ATTEMPT TO SLAVE START A FROZEN BATTERY
SINCE THIS MAY CAUSE IT TO EXPLODE.
Radiator
Hot engine coolant and steam can cause injury. Ensure that the
radiator filler cap is removed with due care and attention.
Engine starting fluid (ether)
Use and recharge system only with suppliers instructions and
replacement parts.
Some machines are fitted with an ether cold starting aid.