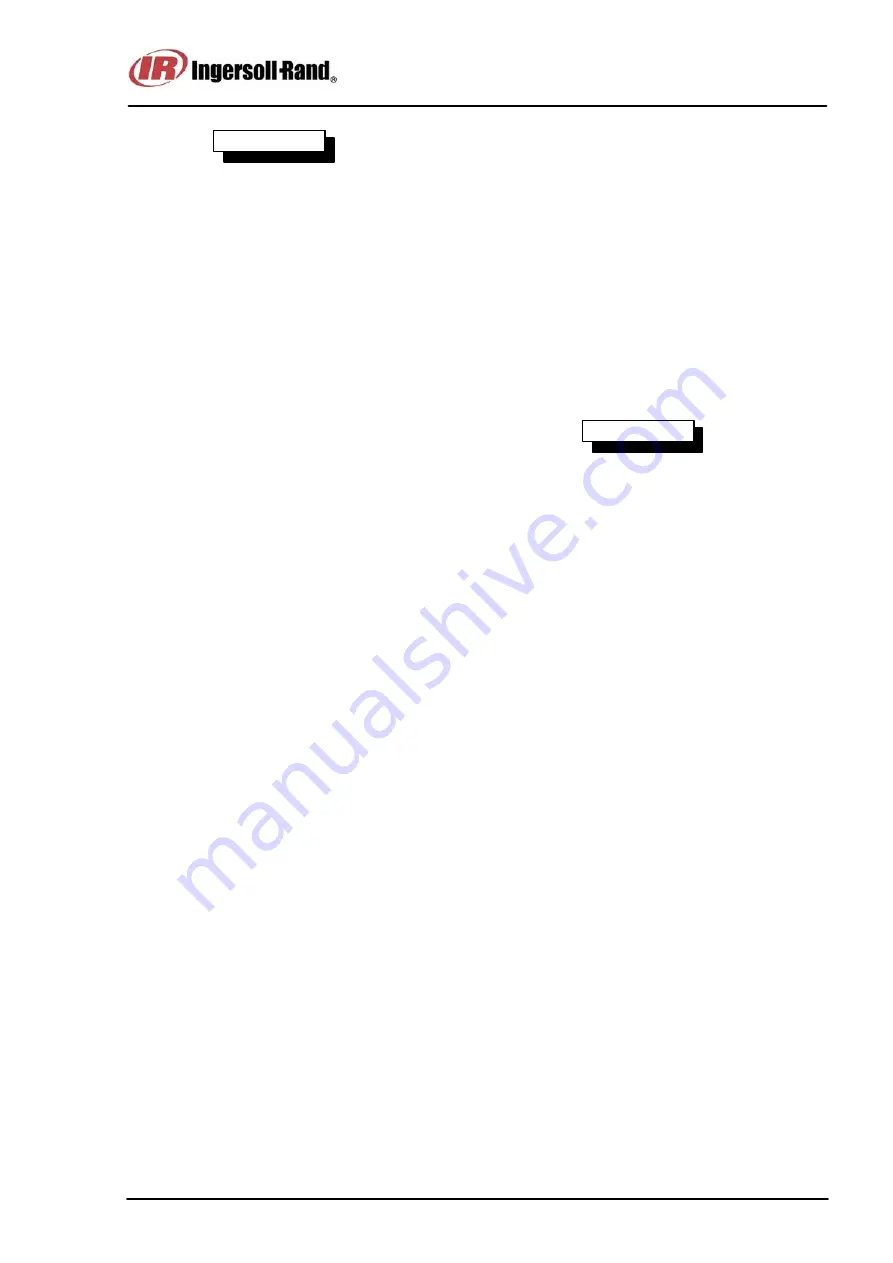
Portable Compressor 7/20
9---5
SEPTEMBER 2003
WARNING
FOLLOW THE INSTRUCTIONS PROVIDED BY THE
ANTIFREEZE SUPPLIER WHEN ADDING OR DRAINING
THE ANTIFREEZE SOLUTION. IT IS ADVISABLE TO WEAR
PERSONAL PROTECTIVE EQUIPMENT TO PREVENT SKIN
AND EYE CONTACT WITH THE ANTIFREEZE SOLUTION.
9.8.
AIR FILTER ELEMENTS
The air filter should be inspected regularly (refer to the
Table
9---1. MAINTENANCE SCHEDULE)
and the element replaced
when the restriction indicator shows red or every 6 Months (500
hours), whichever comes first. The dust collector box(es) should
be cleaned daily (more frequently in dusty operating conditions)
and not allowed to become more than half full.
A. Removal
CAUTION
NEVER REMOVE AND REPLACE ELEMENT(S) WHEN THE
MACHINE IS RUNNING.
Clean the exterior of the filter housing and remove the filter
element by releasing the nut.
B. Inspection
Check for cracks, holes or any other damage to the element by
holding it up to a light source, or by passing a lamp inside.
Check the seal at the end of the element and replace if any sign
of damage is evident.
C. Reassembly
Assemble the new element into the filter housing ensuring that
the seal seats properly.
Reset the restriction indicator by depressing the rubber
diaphragm.
Assemble the dust collector box parts, ensuring that they are
correctly positioned.
Before restarting the machine, check that all clamps are tight.
9.9.
VENTILATION
Always check that the air inlets and outlets are clear of debris
etc.
CAUTION
NEVER CLEAN BY BLOWING AIR INWARDS.
9.10.
COOLING FAN DRIVE
Periodically check that the fan mounting bolts in the fan hub
have not loosened. If, for any reason, it becomes necessary to
remove the fan or re---tighten the fan mounting bolts, apply a
good grade of commercially available thread locking
compound to the bolt threads and tighten to the torque value
shown in the
Table 9---2. TORQUE VALUES
later in this section.
The fan belt(s) should be checked regularly for wear and correct
tensioning.
9.11.
FUEL SYSTEM
The fuel tank should be filled daily or every eight hours. To
minimize condensation in the fuel tank, it is advisable to top up
after the machine is shut down or at the end of each working day
At six month intervals drain any sediment or condensate that
may have accumulated in the tank.
9.12.
FUEL FILTER WATER SEPARATOR
The fuel filter water separator contains a filter element which
should be replaced at regular intervals (see
the Table 9---1.
MAINTENANCE SCHEDULE)
.
9.13.
HOSES
All components of the engine cooling air intake system should
be checked periodically to keep the engine at peak efficiency.
At the recommended intervals, (see the
Table 9---1.
MAINTENANCE SCHEDULE),
inspect all of the intake lines to the
air filter, and all flexible hoses used for air lines, oil lines and fuel
lines.
Periodically inspect all pipework for cracks, leaks, etc. and
replace immediately if damaged.
9.14.
ELECTRICAL SYSTEM
WARNING
ALWAYS DISCONNECT THE BATTERY CABLES BEFORE
PERFORMIN ANY MAINTENANCE OR SERVICE.
Inspect the safety shutdown system switches and the
instrument panel relay contacts for evidence of arcing and
pitting Clean where necessary.
Check the mechanical action of the components.
Check the security of electrical terminals on the switches and
relays le. nuts or screws loose, which may cause local hot spot
oxidation.
Inspect the components and wiring for signs of overheating le.
discolouration, charring of cables, deformation of parts, acrid
smells and blistered paint.
9.15.
BATTERY
Keep the battery terminals and cable clamps clean and lightly
coated with petroleum jelly to prevent corrosion.
The retaining clamp should be kept tight enough to prevent the
battery from moving.
9.16.
PRESSURE SYSTEM
At 500 hour intervals it is necessary to inspect the extemal
surfaces of the system (from the airend through to the discharge
valve(s)) including hoses, tubes, tube fittings and the separator
tank, for visible signs of impact damage, excessive corrosion,
abrasion, tightness and chafing Any suspect parts should be
replaced before the machine is put back into service.
9.17.
TYRES/TYRE PRESSURE
See the
7. GENERAL INFORMATION
section of this manual.
9.18.
RUNNING GEAR/WHEELS
Check the wheel nut torque 30 km (20 miles) after refitting the
wheels. Refer to the
Table 9---2. TORQUE VALUES
later in this
section.
Lifting jacks should only be used under the axle.
The bolts securing the running gear to the chassis should be
checked periodically for tightness (refer to the
Table 9---1.
MAINTENANCE SCHEDULE
for frequency) and re---tightened
where necessary. Refer to the
Table 9---2. TORQUE VALUES
later
in this section.