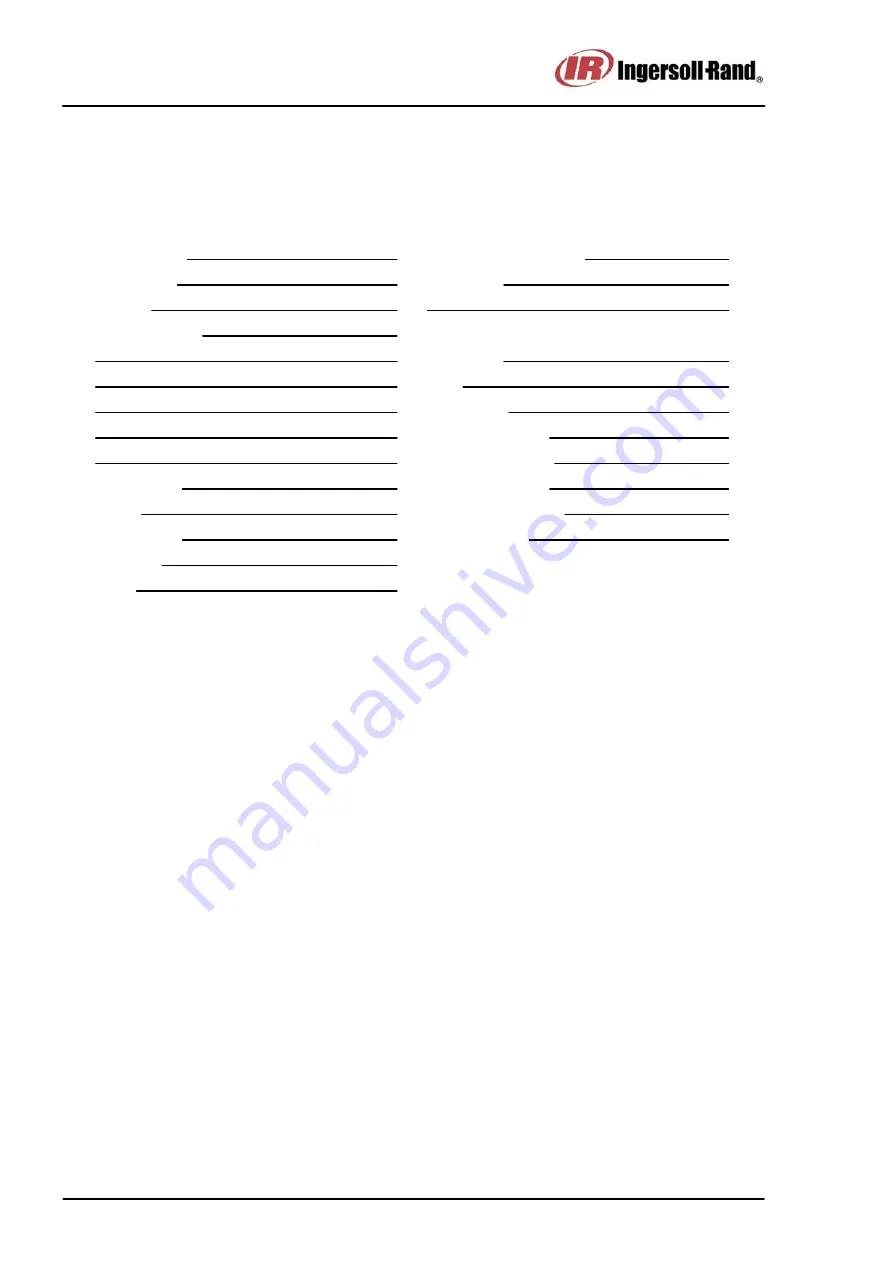
Portable Compressor 7/20
3---6
SEPTEMBER 2003
PORTABLE POWER
EXTENDED WARRANTY REGISTRATION FORM
Customer Details
Company Name:
Contact Name:
Signature:
Company Address:
Post / Zip Code:
Country:
Phone Number:
Service Provider Details
Service Provider / Distributor:
Branch Office:
Machine Details
Serial Number:
Model:
Date of start up:
Fax Number:
e---mail:
Product Type:
Engine Serial Number:
Engine Model Number:
Airend Serial Number:
Alternator Serial Number:
SAMPLE
Figure 3-- 1.
WARRANTY REGISTRATION