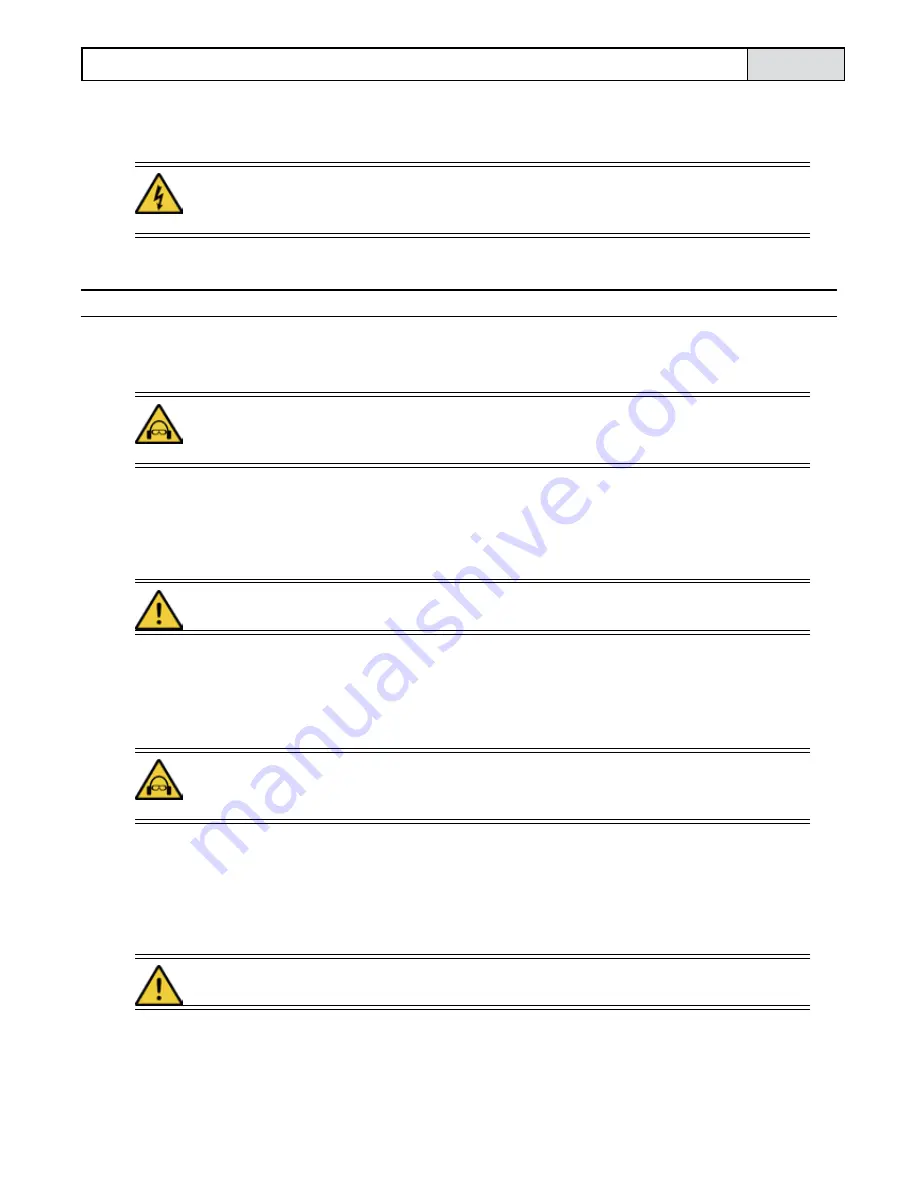
Operating Manual
S210E
5
Personnel being trained or individuals testing the equipment must always be supervised by an
experienced operator.
Work on the electrical parts of the equipment may only be undertaken by a skilled
electrician or by a trained person under the guidance and supervision of a skilled
electrician in accordance with the electrical engineering regulations.
2.4
Safety Precautions Applicable to Different Operating Conditions
Avoid any method of working that impairs safety! All precautions have to be taken. The machine must
only be used in a safe and functional condition.
Only operate the machine when all safety devices and related safety equipment,
e.g. detachable safety devices, emergency stops, and suction devices, are present
and operational!
The machine has to be checked visually at least once a day for any damage and defects.
In the event of operational malfunctions the machine must be shut down immediately and secured.
The error must be rectified before starting the machine again.
Secure the work area around the machine in public areas providing a safety
distance of at least 7 ft./ 2m around the machine.
Default must be rectified immediately!
Start up / switch off operations and control devices have to be handled in accordance with the
Operating Instructions.
All persons in the proximity of the machine must wear safety glasses with lateral
protection as well as safety shoes. Ear protection may be required. The operator is
required to wear close fitting protective clothing.
Use only extension cables for extending the main cable that are sized and marked in accordance with
the overall power consumption of the machine following valid VDE and local guidelines.
Before starting the machine ensure that no person in the job site can be endangered when the
machine starts running.
Do not switch off or remove the exhaust and ventilation devices when the machine
is running!
Summary of Contents for S210E
Page 1: ...Operating Manual S210E Your Partner for Mobile Surface Preparation IMPACTSamericas com...
Page 35: ...Operating Manual S210E 33 8 2 Circuit Diagram...
Page 40: ...S210E Operating Manual 38 10 2 Blast Wheel Drive Front...
Page 41: ...Operating Manual S210E 39 10 3 Handle Section...
Page 42: ...S210E Operating Manual 40 10 4 Separator Top Section...
Page 43: ...Operating Manual S210E 41 10 5 Abrasive Feeder...
Page 44: ...S210E Operating Manual 42 10 6 Liner Wheel Housing...
Page 45: ...Operating Manual S210E 43 10 7 Base Seal Assembly...
Page 46: ...S210E Operating Manual 44 10 8 Undercarriage...
Page 47: ......