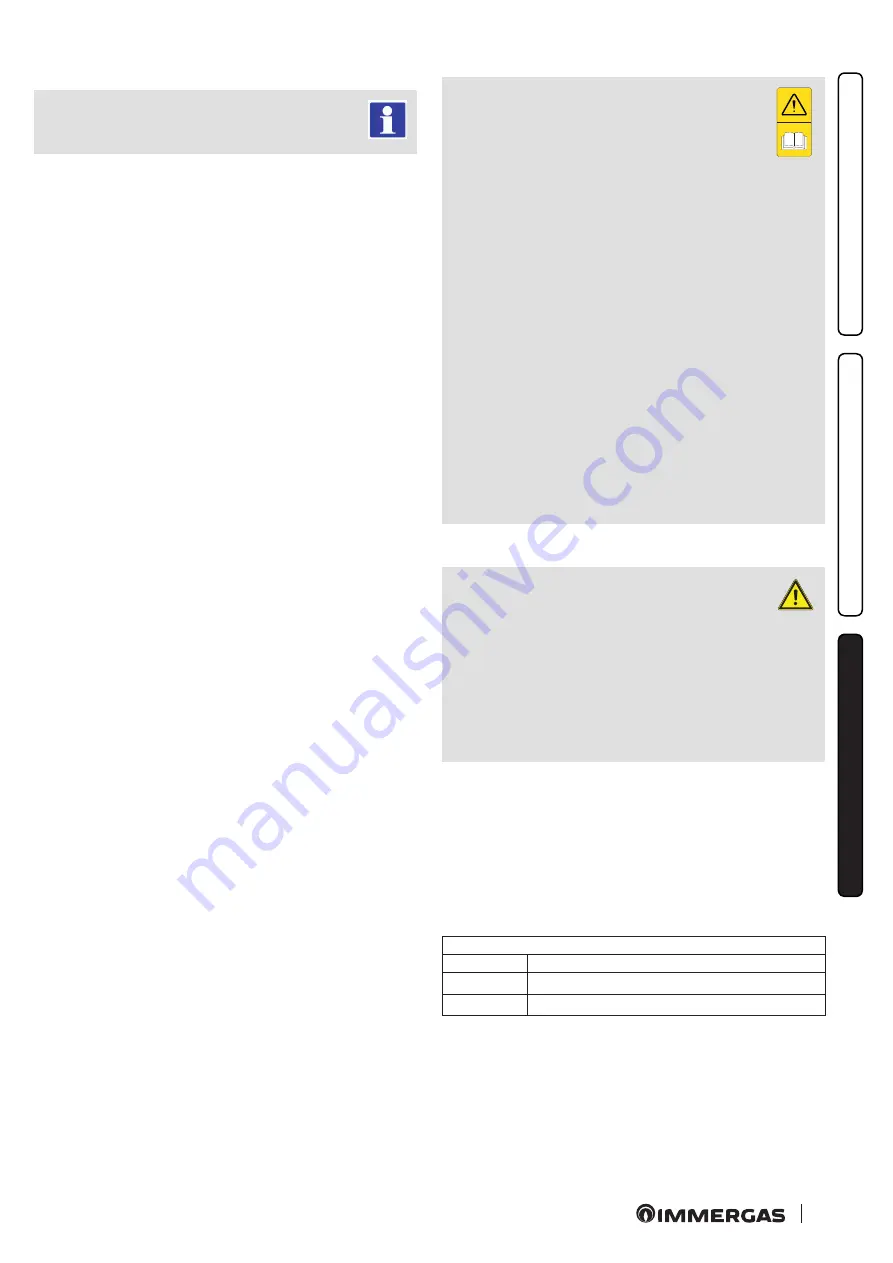
67
INS
TALL
AT
O
RE
U
TENTE
MANU
TENT
O
RE
3.7 TROUBLESHOOTING.
Maintenance interventions must be carried out by an
authorised company (for example contact the Author-
ised Technical Service Centre).
Red pump LED.
There can be three possible causes for this anomaly:
- Low power supply voltage.
When the minimum voltage is
reached after about 2 seconds, the LED switches from green to
red and the pump stops. Wait for the power supply voltage to
rise; when the pump restarts, the LED will turn green again with
a delay of about one second.
Note: obviously the flow rate decreases as the supply voltage
decreases.
- Rotor seized.
Powering the pump with the rotor seized, after
about 4 seconds the LED switches from green to red. Carefully
act on the screw in the middle of the head to manually release
the crankshaft; circulation starts up immediately after the rotor
is released and the LED switches from red to green after about
10 seconds.
- Electrical error.
Pump, wiring or P.C.B. fault. Check the indi-
cated components.
- Smell of gas.
Caused by leakage from gas circuit pipelines. Check
sealing efficiency of gas intake circuit.
- Repeated ignition blocks.
Check the presence of pressure in
the network and that the gas adduction cock is open. Incorrect
adjustment of the gas valve, check the correct calibration of the
gas valve.
- Irregular combustion or noisiness.
It may be caused by: a
dirty burner, incorrect combustion parameters, intake-exhaust
terminal not correctly installed. Clean the above components
and ensure correct installation of the terminal, check correct
setting of the gas valve (Off-Set setting) and correct percentage
of CO2 in flue gas.
- Frequent interventions of the safety thermostat function
(delegated to flow probe and system return probe).
It can de-
pend on the lack of water in the boiler, little water circulation in
the system or blocked pump. Check on the pressure gauge that
the system pressure is within established limits. Check that the
radiator valves are not closed and also the functionality of the
pump.
-
Siphon blocked.
This may be caused by dirt or combustion
products deposited inside. Check that there are no residues of
material blocking the flow of condensate.
-
Heat exchanger blocked.
This may be caused by the drain trap
being blocked. Check that there are no residues of material
blocking the flow of condensate.
-
Noise due to air in the system.
Check opening of the special air
vent valve cap (Part. 18 Fig. 39). Make sure the system pressure
and expansion vessel pre-charge values are within the set limits;
The factory-set pressure values of the expansion vessel must be
1.0 bar, the value of system pressure must be between 1 and 1.2
bar.
3.8 CONVERTING THE BOILER TO OTHER
TYPES OF GAS.
If the boiler has to be converted to a different gas type
to that specified on the data nameplate, request the
relative conversion kit for quick and easy conversion.
The gas conversion operation must be carried out by
an authorised company (e.g. Authorised After-Sales Centre).
To convert to another type of gas the following operations are
required:
- remove power from Victrix Hybrid;
- replace the nozzle located on the upper fitting of the gas valve
(Part. 8 Fig. 39), taking care to disconnect the indoor unit
during this operation;
- restore power to Victrix Hybrid;
- calibrate the number of fan revolutions (Parag. 3.8);
- adjust the correct CO2 value (Parag. 3.9);
- seal the gas flow rate devices (if adjusted);
- after completing the conversion, apply the sticker, contained
in the conversion kit, on the data plate in the area relating to
the type of gas.
These adjustments must be made with reference to the type of
gas used, following that given in the table (Par. 4.2).
3.9 INDOOR UNIT FAN REVS NUMBER CALIBRATION.
ATTENTION:
verification and calibration are necessa-
ry, in the case of transformation to other
types of gas, in the extraordinary maintenance
phase with replacement of the PCB, air/gas cir-
cuit components or in the case of installations
with flue extraction systems, with horizontal
concentric pipe measuring more than 1 metre.
The indoor unit heat output is correlated to the length of the air
intake and flue exhaust pipes. This decreases with the increase
of pipe length. The indoor unit leaves the factory adjusted for
minimum pipe length (1m coaxial).
- activate flue test (Parag. 3.16);
- detect the flue signal ∆P (Ref. 12 and 13 Fig. 50);
- compare the signal ∆P and, if necessary, correct the S1 operating
parameters with the following table:
Victrix Hybrid
∆P > 200 Pa
G20
S1 = 126 (6300 rpm)
G31
S1 = 121 (6050 rpm)