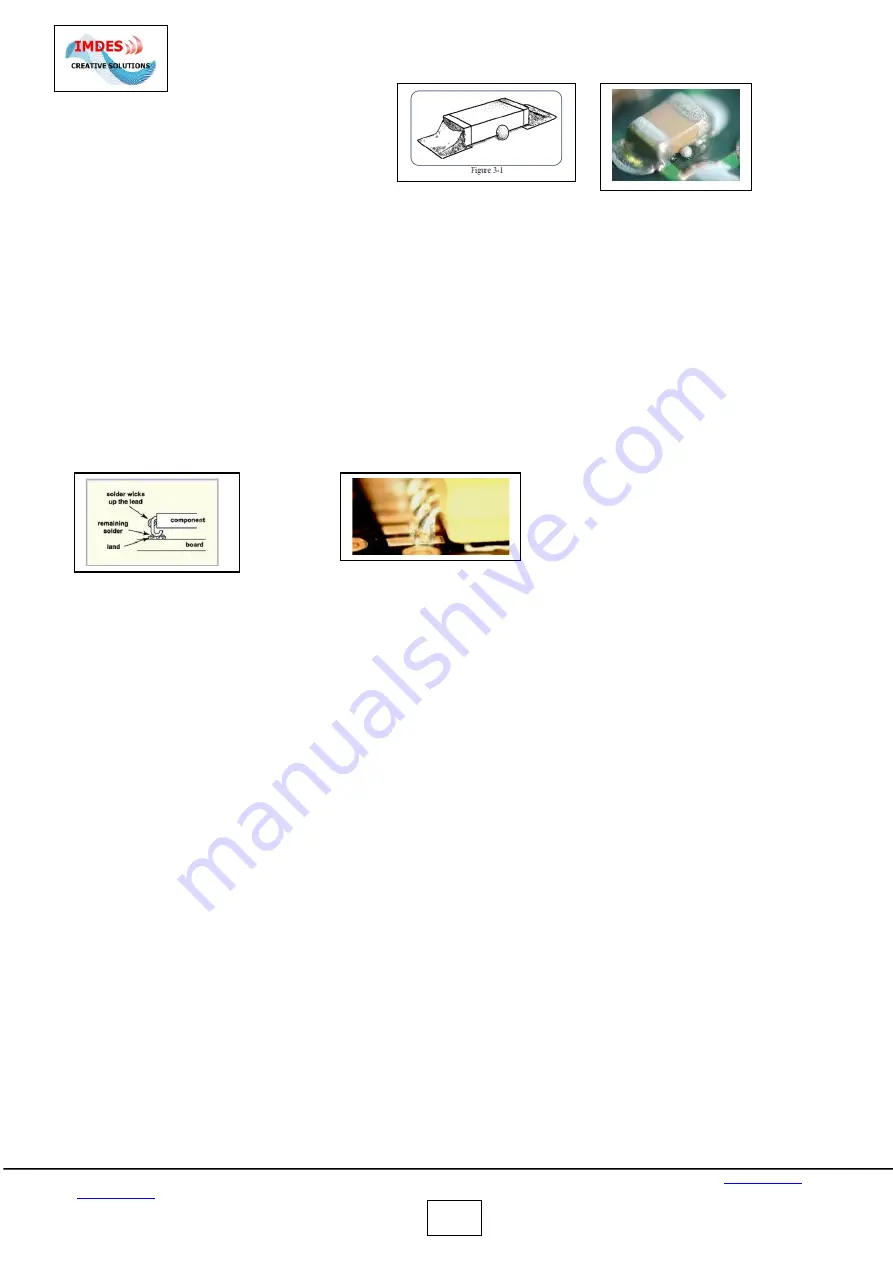
IMDES CREATIVE SOLUTIONS Schulstrasse 21 D-48455 Bad Bentheim /Gildehaus Germany T:+49(0)5924-997337 E:
© 2019
IMDES CREATIVE SOLUTIONS
25
4.0 Tips for reflow soldering.
4.1 Soldering errors
Random Solder Balls
4.1.1
Solder Balls The causes for solder balls are different:
• The temperature gradient in pre-heating is too high, which causes the solvent in the paste to evaporate violently,
ripping out solder paste balls from the print of the paste.
• The paste print rests on the solder resist. (Wrong pressure or mask too large). Good results are obtained if the
print of the paste is reduced by approx. 10 to 15 %).
• The applied solder paste is too old or of bad or unsuitable quality.
• The bottom side of the stencil or the screen is not clean, thus depositing paste residues on the assembly surface.
• Due to a bad wetting of the pad or component the wetting is incomplete. Some paste remains on the assembly in
the form of balls.
• The amount of paste relative to the available pad size is too high. Generally, due to the careful heating with
vapor-phase soldering the solder ball formation is greatly reduced.
4.1.2 Wicking-Effect
The wicking effect is the rise of the molten solder on component leads. This disrupts the soldering to the contact
pad below. The wicking effect is known mostly with infrared or convection machines with very high pre-heating
speeds. Lately it is found rather frequently with backplane SMD connectors, due to an extremely large amount of
energy flowing across the pin-area into the metal. Thus the pins reach soldering temperature much faster than the
pad below.
1. The wicking effect is mostly caused by bad solder ability of the contact pads on the assembly.
2. The component leads reach the flow point temperature much faster than the metallization of the substrate. This
causes the paste to melt and to rise along the leads. In this case, the so-called ‘top heat‘ is too high. The formation
of the wicking effect may be controlled via the machine technology by lowering the temperature gradient starting
at approx. 150° C.
With vapor-phase soldering the wicking effect is practically unknown, because of
the negligible temperature differences on the printed circuit boards and the components
.