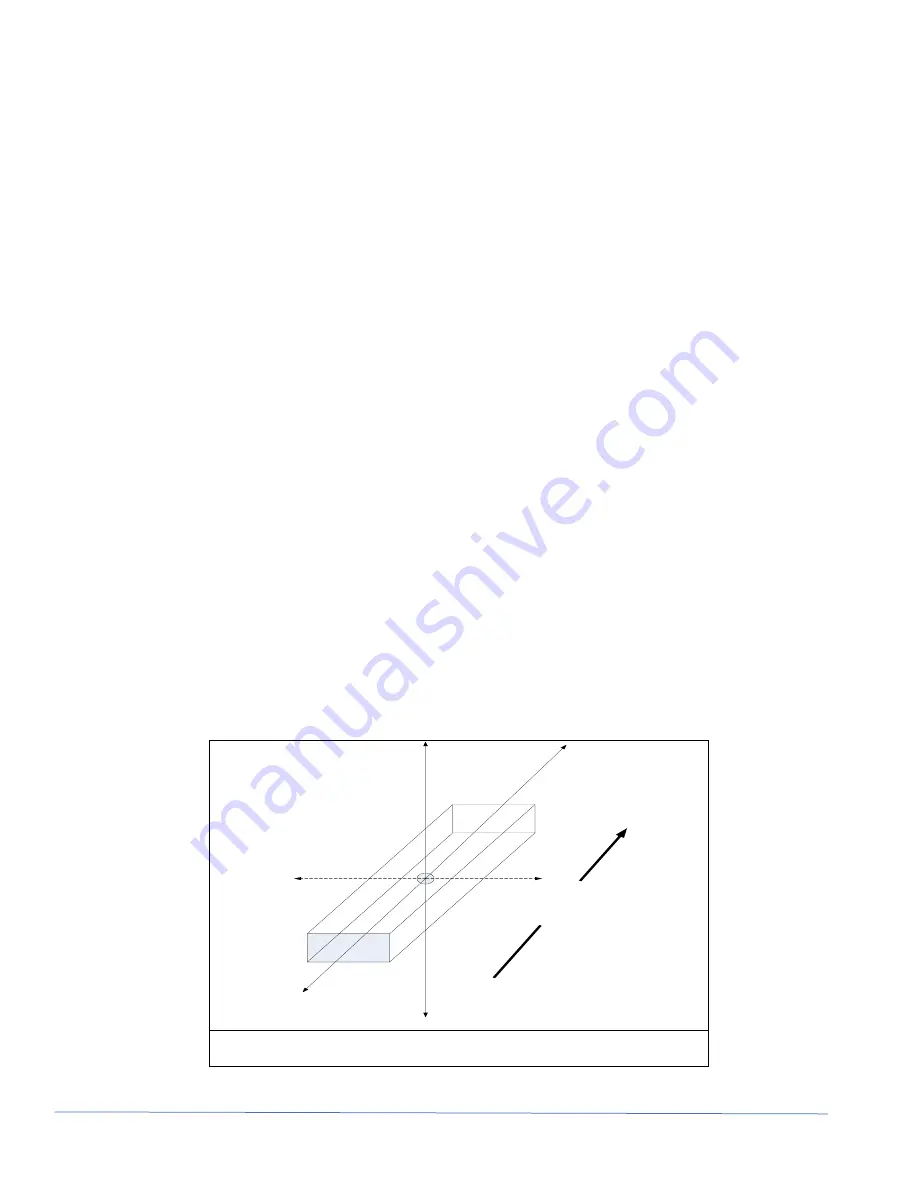
Doc no: 430-041-01
12 of 64
•
The minimum specification for the DT100 SIR box control computer is as follows:
o
Intel i5 processor
o
8 GB Ram
o
USB 3.0
o
A discreet hardware Ethernet port supported by a Realtek PCIE GBE family chipset (not an
FE family chipset) (see bullet point above).
3.2.2. Establishing of Vessel Reference Frame and Sensor Static Offsets
Once all interfacing has been completed and tested, a vessel reference frame should be established. In order
to integrate the sonar vectors with the other sensor outputs, the static offsets between the MRU, the MBES
and the positioning system antennae must be measured accurately and referred to a common reference point
(CRP).
The CRP can be arbitrarily located anywhere on the survey platform, but it is good practice (where possible)
to locate it at the intersection of the roll and pitch axes or at the centre of gravity of the vessel. It must be
chosen so it is readily accessible and in a place from which sensor offsets can easily be measured.
Note: The position of the intersection of the roll and pitch axes is not often obvious. Customarily, the roll axis
is coincident with the water plane (varies with loading conditions) while the pitch axis passes through the
centre of floatation. The ship's builder or general arrangement (GA) drawings should be checked for the
accurate location of these two axes.
Land survey techniques can be used to establish the platform’s sensor static offsets reference frame and this
will ensure the highest degree of accuracy and with a large vessel, this may be the only way to derive such
values. Alternately, steel tape measur
ements may be taken, or the vessel’s GA drawings used to derive the
offsets. The convention for X, Y and Z (+ and -) are dependent on the navigation software used (refer to the
navigation software documentation). The most common convention is illustrated in Figure 3-4 General
convention for sensor static offsets.
Land survey techniques may also be used to establish a rotational offset in the horizontal plane (yaw),
between the vessels fore and aft line and that of the heading reference and MBES transducer. Prior to this
operation (if used), it is essential that the gyro be warmed up and settled. The rotational offset between the
heading reference and the MBES projection transducer will also be established during the patch test (see
Section 4.2), but this should be a fine adjustment only.
Figure 3-4 General convention for sensor static offsets
Pl
at
fo
rm
F
or
wa
rd
-X
+X
-Y
+Y
+Z
-Z
CRP
Summary of Contents for DT101Xi
Page 35: ...Doc no 430 041 01 35 of 64 APPENDIX A DT101Xi DT102Xi SPEC SHEETS DT101Xi...
Page 36: ...Doc no 430 041 01 36 of 64...
Page 37: ...Doc no 430 041 01 37 of 64...
Page 38: ...Doc no 430 041 01 38 of 64...
Page 39: ...Doc no 430 041 01 39 of 64 DT102Xi...
Page 40: ...Doc no 430 041 01 40 of 64...
Page 41: ...Doc no 430 041 01 41 of 64...
Page 42: ...Doc no 430 041 01 42 of 64...
Page 52: ...Doc no 430 041 01 52 of 64 Figure 6 7 Jumpers for Heading and PPS Selection...
Page 56: ...Doc no 430 041 01 56 of 64 Figure 6 8 Power Supply Voltage Option...