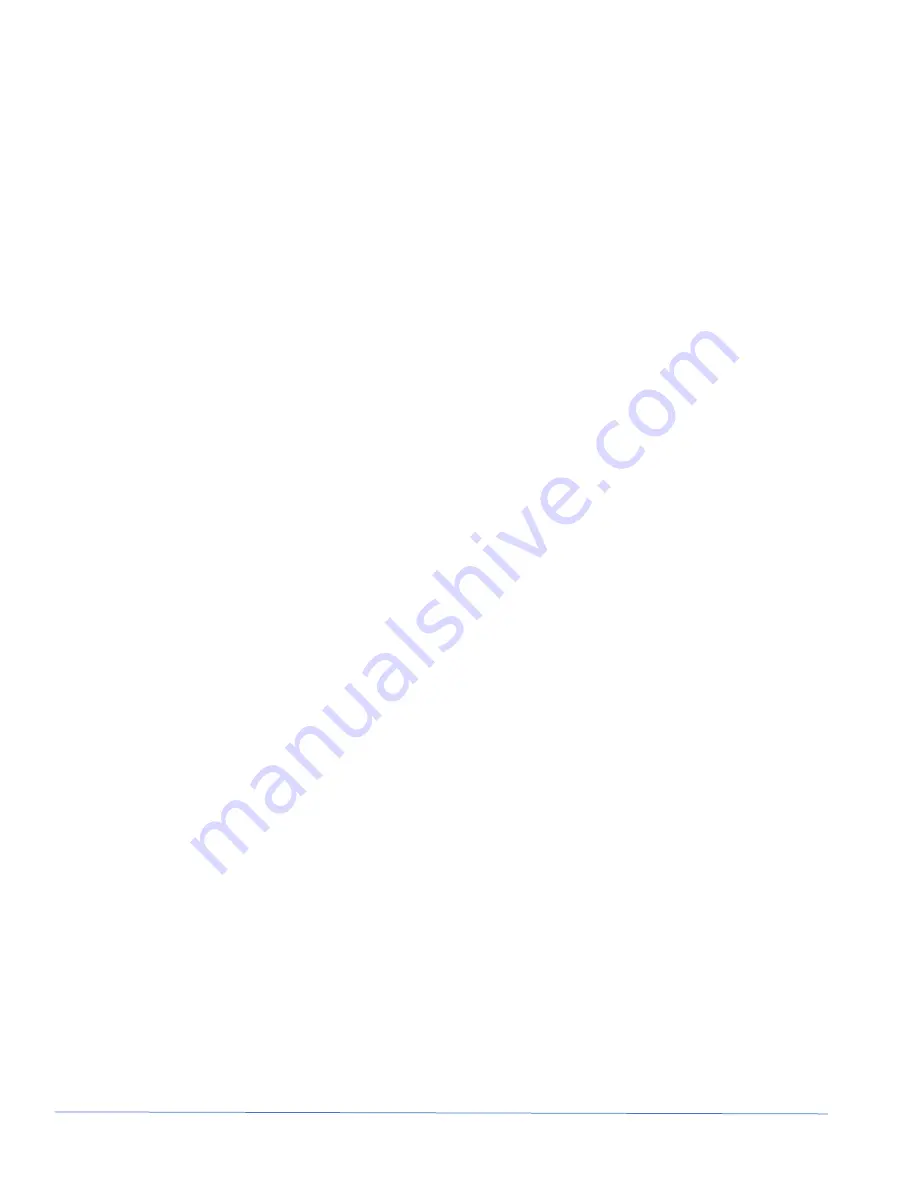
Doc no: 430-041-01
9 of 64
3. Preparation
3.1. The vessel
Scenarios around the use and choice of vessel differ significantly depending on an array of factors, however
if a vessel of opportunity is sought, the following factors should be considered:
•
Stability. A vessel with the ability to experience minimal movement in the six degrees of freedom
(pitch, roll, yaw, surge, sway and heave) is always advantageous.
•
Vibration. Vibration will invariably translate into artefacts in the data logged. Vibration mitigation (such
as resilient mounts) should be considered if possible.
•
Bracket mounting options. If a pole mount is to be used to mount the transducer, there must be a
rigid point of attachment to the vessel that minimizes pole movement. Braces should be used if
possible, to ensure no movement of the pole is observed when survey speed is reached. There
should be no propeller / thruster wash over the transducer and no cooling water outlet close by that
could adversely affect the SVS reading.
•
Masts. Line of sight (LOS) to GNSS satellites as well as RTCM transmitters is essential and suitable
locations for these antennas is required. They should have unobstructed LOS and not be subject to
excessive vibration nor exhaust / funnel discharge.
•
Power. A suitable source of power is essential. The power should be clean, uninterrupted, overload
protected and the source be capable of supplying sufficient voltage at the required amperage (i.e.
wattage). The Sensor Interface Relay (DT100 SIR) unit provides power for the integrated MRU and
SV sensor (if fitted) as well as the sonar head so no additional power is required for the Imagenex
supplied equipment. Power is also made available on the GNSS (GPS), Heading and Sound Velocity
ports (at user selectable 12 and 24 VDC See APPENDIX C 6. Power). These power supplies can
supply 20 Watts and this should not be exceeded. Additional power may be required for the heading
reference, GNSS system and the computers running the navigation and MBES control software as
well as external SV sensors and MRUs (if required). The SIR box requires 100
– 240 VAC or
12
– 36 VDC and consumes 35 Watts (nominal) or 80 Watts (maximum)
of power. It is recommended
that devices such as surge protectors, Uninterrupted Power Supplies (UPS) and / or invertors be
used to ensure clean and reliable power.
•
Access to vessel centre of gravity (COG). Although not essential, it is recommended practice to install
the MRU as close as possible to the COG of the vessel. Since measurements to this point are
required during the navigation software set-up to establish the vessel reference frame, it is
advantageous to have this location accessible, at least during mobilization.
•
Work area. There should be a work area set aside from the normal vessel operation that affords the
Surveyor a suitable work environment that is quiet and free from distractions. Good housekeeping
should be practiced to ensure that hardware, wiring etc. are not disturbed during operations.
3.2. Survey Planning
3.2.1. Mobilization
A common sense and good seamanship approach is required to ensure a reliable and quality mobilization.
The following bullet points highlight some considerations:
•
Cable runs. Cables should be installed such that they are not subjected to mechanical stress, do not
exceed their minimum bend radii, are not of excessive length and do not pose a risk to personnel.
The maximum cable length for the DT101
Xi
and DT102
Xi
is 100 m through Ethernet Cat 5e, although
longer runs are available using additional hardware. The cable between the MBES and the SIR box
should never be allowed to be stepped on. Where possible, glands should be used to transit
bulkheads and the water tight integrity of the vessel should never be compromised.
•
DT101
Xi
and DT102
Xi
both use underwater wet-mateable 8 conductor SubConn connectors. It is
recommended that connectors be thoroughly cleaned using a spray-based cleaner like Isopropyl
alcohol; or liquid soap and hot water. Acetone, gasoline or similar products are not recommended.
Summary of Contents for DT101Xi
Page 35: ...Doc no 430 041 01 35 of 64 APPENDIX A DT101Xi DT102Xi SPEC SHEETS DT101Xi...
Page 36: ...Doc no 430 041 01 36 of 64...
Page 37: ...Doc no 430 041 01 37 of 64...
Page 38: ...Doc no 430 041 01 38 of 64...
Page 39: ...Doc no 430 041 01 39 of 64 DT102Xi...
Page 40: ...Doc no 430 041 01 40 of 64...
Page 41: ...Doc no 430 041 01 41 of 64...
Page 42: ...Doc no 430 041 01 42 of 64...
Page 52: ...Doc no 430 041 01 52 of 64 Figure 6 7 Jumpers for Heading and PPS Selection...
Page 56: ...Doc no 430 041 01 56 of 64 Figure 6 8 Power Supply Voltage Option...