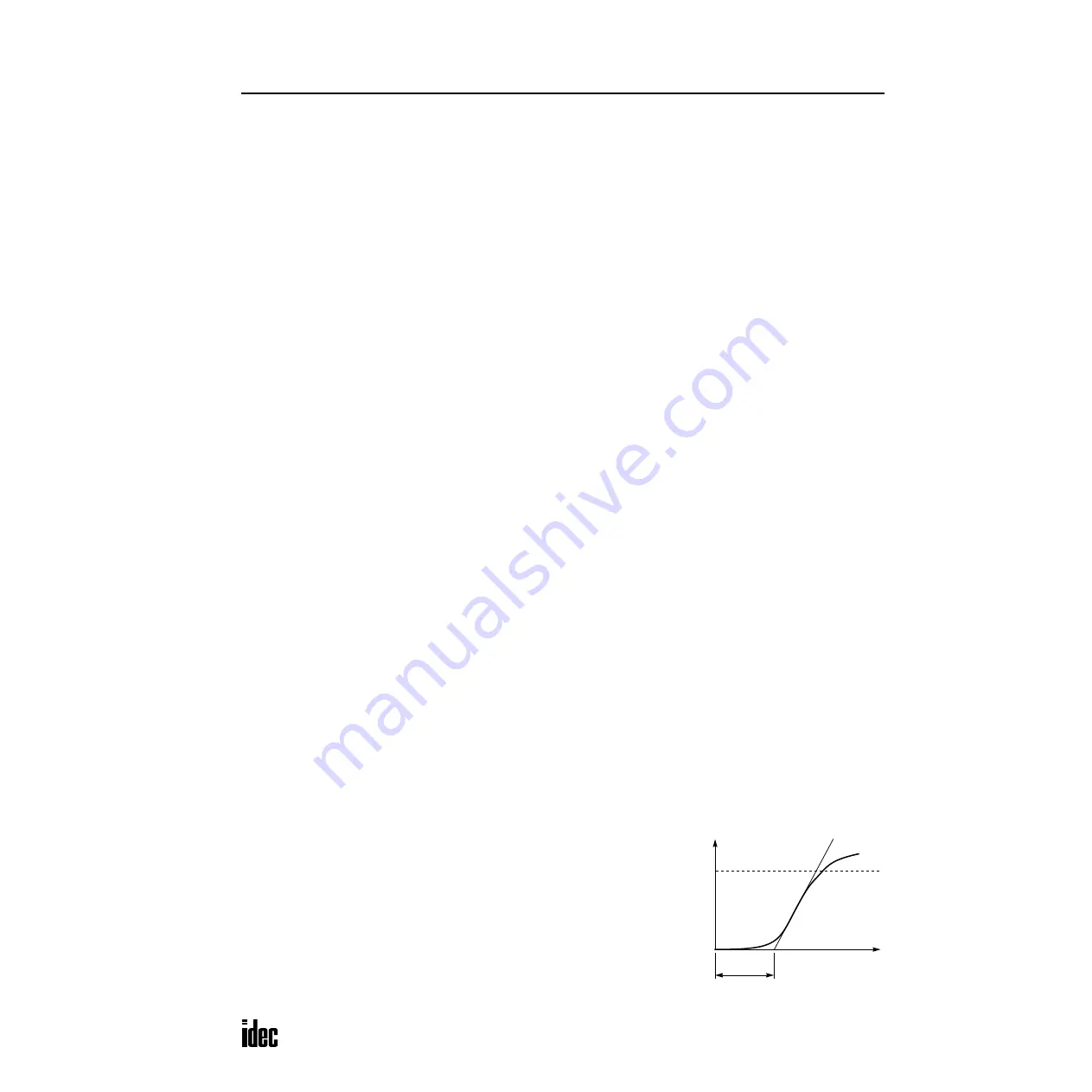
20: PID I
NSTRUCTION
O
PEN
N
ET
C
ONTROLLER
U
SER
’
S
M
ANUAL
20-9
Set the AT sampling period to a long value to make sure that the current process variable is smaller than or equal to the pre-
vious process variable during direct control action (S2+0 is on) or that the current process variable is larger than or equal to
the previous process variable during reverse control action (S2+0 is off).
S1+20 AT Control Period
The AT control period determines the duration of the ON/OFF cycle of the control output (S2+6) during auto tuning. For
operation of the control output, see Control Period on page 20-7.
When using auto tuning, set a required value of 1 through 500 to specify an AT control period of 0.1 sec through 50.0 sec
to the data register designated by S1+20. When S1+20 stores 0, the AT control period is set to 0.1 sec. When S1+20 stores
a value larger than 500, the AT control period is set to 50.0 sec.
S1+21 AT Set Point
While auto tuning is executed, the AT output manipulated variable (S1+22) is outputted to the output manipulated variable
(S1+1) until the process variable (S1+0) reaches the AT set point (S1+21). When the process variable (S1+0) reaches the
AT set point (S1+21), auto tuning is complete and the output manipulated variable (S1+1) is reduced to zero. When PID
action is selected with operation mode (S1+3) set to 1 (AT+PID), the PID action follows immediately.
When the linear conversion is disabled (S1+4 set to 0), set a required AT set point of 0 through 4000 to the data register
designated by S1+21. When S1+21 stores a value larger than 4000, the AT set point is set to 4000.
When the linear conversion is enabled (S1+4 set to 1), set a required AT set point of –32768 through 32767 to the data reg-
ister designated by S1+21. The AT set point must be larger than or equal to the linear conversion minimum value (S1+6)
and must be smaller than or equal to the linear conversion maximum value (S1+5).
In the direct control action (see page 20-10), set the AT set point (S1+21) to a value sufficiently smaller than the process
variable (S4) at the start of the auto tuning. In the reverse control action, set the AT set point (S1+21) to a value sufficiently
larger than the process variable (S4) at the start of the auto tuning.
S1+22 AT Output Manipulated Variable
The AT output manipulated variable specifies the amount of the output manipulated variable (0 through 100) during auto
tuning. When using auto tuning, set a required AT output manipulated variable of 0 through 100 to the data register desig-
nated by S1+22. When S1+22 stores a value larger than 100, the AT output manipulated variable is set to 100.
While auto tuning is executed, the specified value of the AT output manipulated variable (S1+22) is outputted to the output
manipulated variable (S1+1), and the control output (S2+6) is turned on and off according to the AT control period
(S1+20) and the AT output manipulated variable (S1+22). To keep the control output (S2+6) on during auto tuning, set 100
to S1+22.
Auto Tuning (AT)
When auto tuning is selected with the operation mode (S1+3) set to 1 (AT+PID) or 2 (AT), the auto tuning is executed
before starting PID control to determine PID parameters, such as proportional gain (S1+7), integral time (S1+8), derivative
time (S1+9), and control action (S2+0) automatically. The
OpenNet Controller
uses the step response method to execute
auto tuning. To enable auto tuning, set four parameters for auto tuning before executing the PID instruction, such as AT
sampling period (S1+19), AT control period (S1+20), AT set point (S1+21), and AT output manipulated variable (S1+22).
Step Response Method
The
OpenNet Controller
uses the step response method to execute
auto tuning and determine PID parameters such as proportional
gain (S1+7), integral time (S1+8), derivative time (S1+9), and con-
trol action (S2+0) automatically. The auto tuning is executed in the
following steps:
1.
Calculate the maximum slope of the process variable (S1+0)
before the process variable reaches the AT set point (S1+21).
2.
Calculate the dead time based on the derived maximum slope.
3.
Based on the maximum slope and dead time, calculate the four
PID parameters.
Process Variable (S1+0)
Dead Time
Maximum Slope
AT Set Point (S1+21)
Phone: 800.894.0412 - Fax: 888.723.4773 - Web: www.clrwtr.com - Email: [email protected]