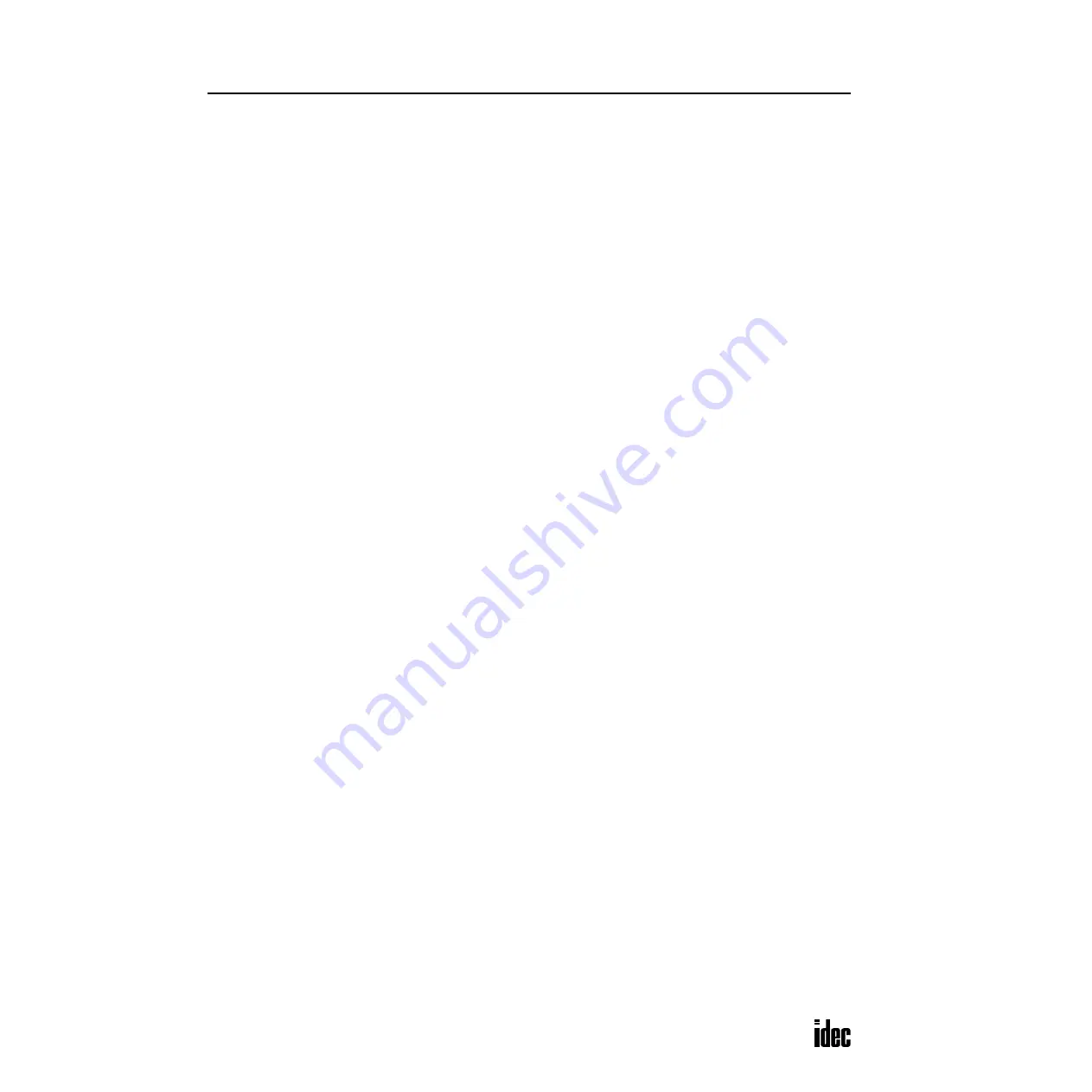
18: P
ROGRAM
B
RANCHING
I
NSTRUCTIONS
18-6
O
PEN
N
ET
C
ONTROLLER
U
SER
’
S
M
ANUAL
Phone: 800.894.0412 - Fax: 888.723.4773 - Web: www.clrwtr.com - Email: [email protected]
18: P
ROGRAM
B
RANCHING
I
NSTRUCTIONS
18-6
O
PEN
N
ET
C
ONTROLLER
U
SER
’
S
M
ANUAL
Phone: 800.894.0412 - Fax: 888.723.4773 - Web: www.clrwtr.com - Email: [email protected]