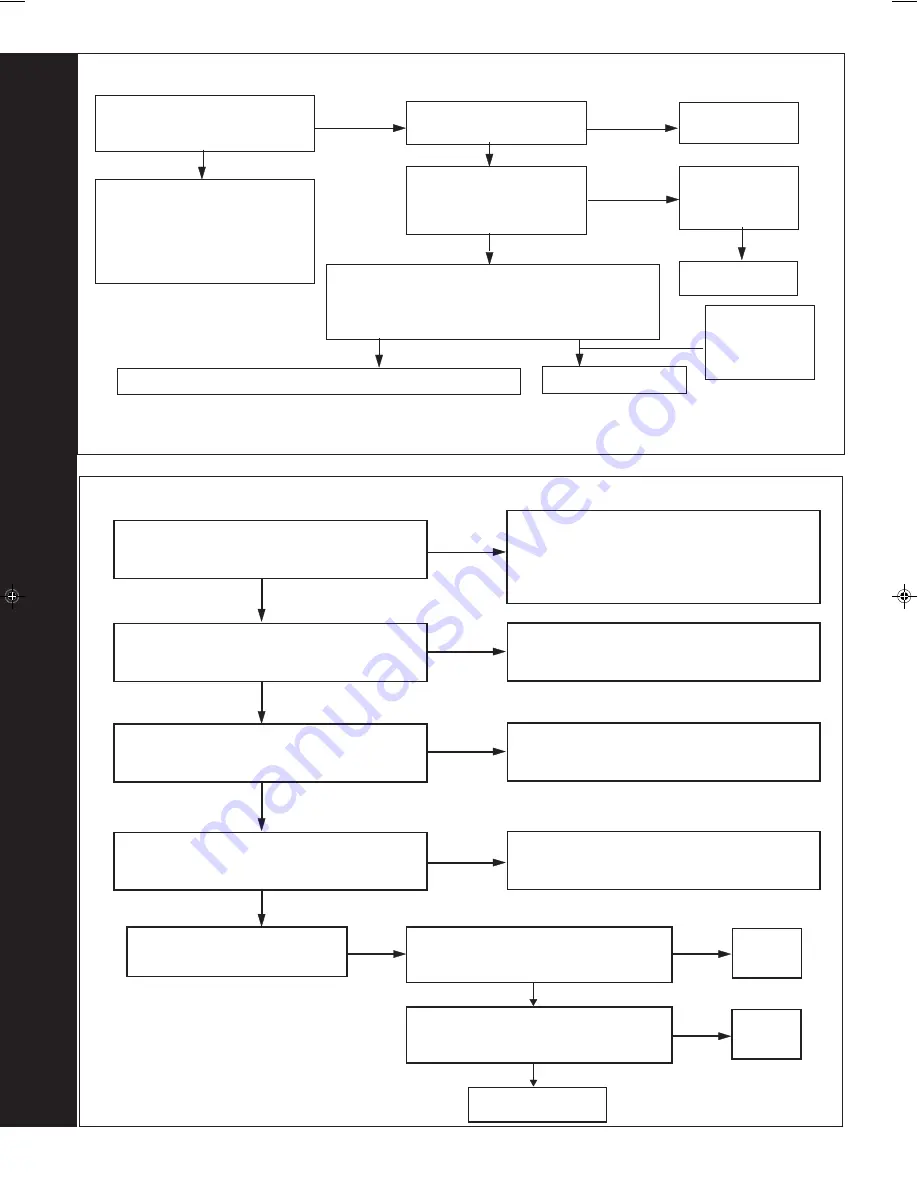
66
istor system store -
Installation and Servicing
FAULT FINDING
F
AUL
T FINDING F
AUL
T FINDING F
AUL
T FINDING F
AUL
T FINDING F
AUL
T FINDING
97 L.....F....... (FLAME DETECTION)
Check the ignition electrode and associated harness
for: continuity, visual condition
,
position
(Refer to Frame 69).
Are these functioning correctly ?
Check gas valve
wiring for
continuity
YES
Check the detection electrode and
associated harness for:
continuity, visual condition, position
(
Refer to Frame 70
).
Replace if necessary.
If the boiler reset button is
pressed does the boiler ignite
for a short time then extinguish?
Is 200V DC supply
available at the gas valve ?
(see Note)
NO
YES
YES
Is 17mbar gas pressure
available at the boiler inlet ?
Replace PCB
Check gas supply
and rectify fault
Replace ignition electrode and associated harness as necessary
NO
Replace gas valve
YES
NO
NO
98 L.....E
or
H.....E...... (BOARD ERROR)
Check for an excess voltage between neutral
and earth. Is the value below 50V?
Check earth connection to the boiler. If
value is still in excess of 50V consult a
Qualified Electrician to check the
household electrical supply & circuitry.
Note.
Due to the wave form of the rectified voltage, the reading will vary depending on the type of meter used to measure the
value (some may measure the possible peak voltage of 339V). In general terms a reading greater than 150V indicate
that the correct voltage is supplied to the gas valve.
Check syphon
and condensate
drain pipework
for blockage
LE ONLY
: Check continuity of OH thermostat.
Is this correct?
Correct wiring or replace thermostat
HE ONLY
: Check earth wire is connected to
detection lead. Is this correct?
Correct wiring or replace detection lead
Check all earths for continuity
Correct connections
Internal fault within the PCB
Press and hold reset button for 2 seconds.
Does boiler operate correctly?
OK
Turn boiler off and wait for 5 seconds. Turn
boiler on. Does boiler operate correctly?
OK
Replace PCB
NO
NO
NO
NO
NO
NO
YES
YES
YES
YES
YES
YES
Summary of Contents for istor HE260
Page 2: ...2 istor system store Installation and Servicing...
Page 73: ...73 istor system store Installation and Servicing...
Page 74: ......
Page 76: ...Gas Safe Register ID Number...
Page 78: ...78 istor system store Installation and Servicing...
Page 79: ...79 istor system store Installation and Servicing...