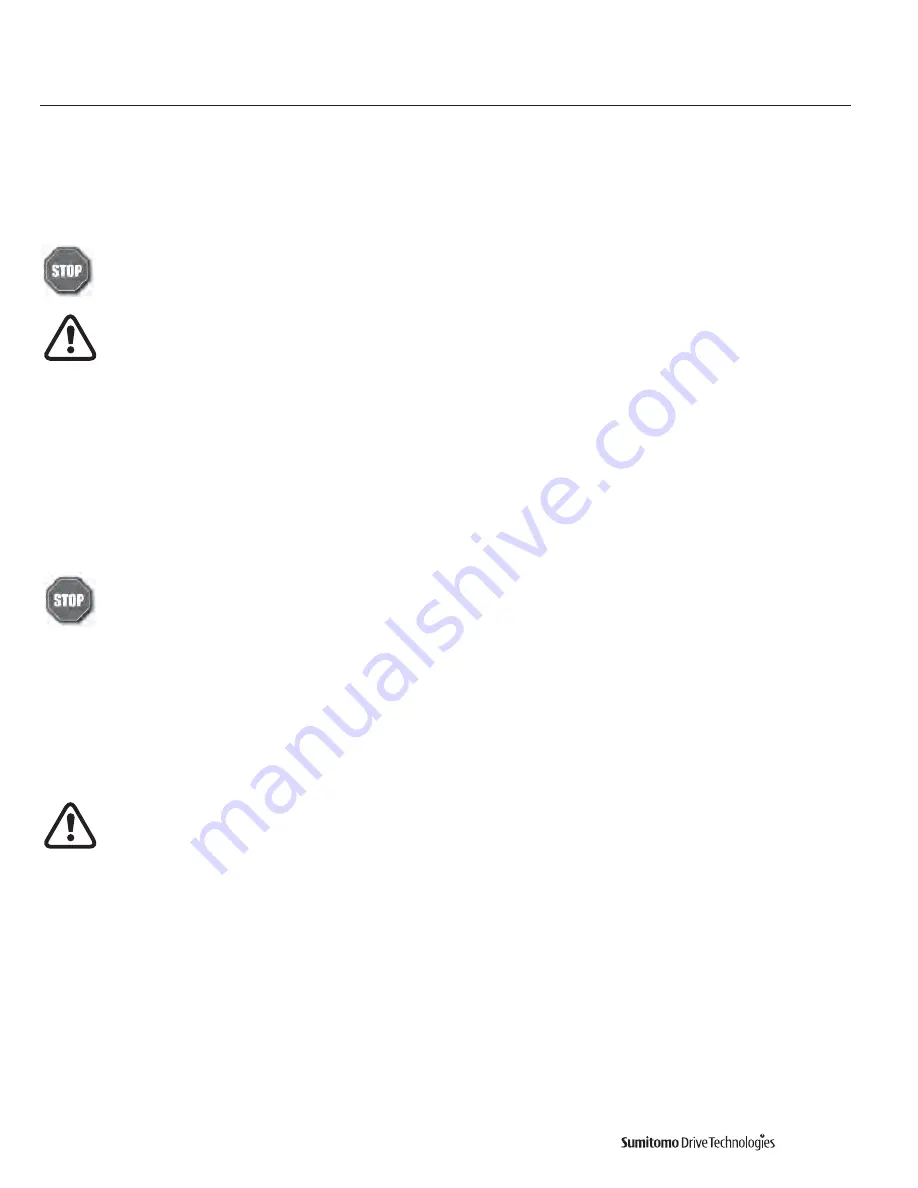
Cyclo® BBB4
2
Operation & Maintenance Manual
Cyclo® BBB4
Important Notes
Safety Symbols
These safety symbols appear throughout this manual to indicate
important warnings:
DANGER:
Incorrect handling of the unit and/or
failure to follow the instructions may cause physical
damage, serious personal injury, and/or death.
CAUTION:
Incorrect handling of the unit and/or
failure to follow the instructions may cause physical
damage and/or personal injury.
Safety Precautions
Review and adhere to the instructions in this manual to ensure:
• trouble-free Cyclo® BBB4 operation
• your rights to make a warranty claim.
Read this manual and all accompanying documents thoroughly
before use. Understand the machine, information on safety, and
all precautions for correct operation. Sumitomo recommends
making this manual easily accessible for reference at the machine
location.
•
Only properly trained personnel
should
transport, install, align, wire, inspect, operate, and
maintain the unit.
• When the unit is to be used in a system for
transport of human beings, a secondary safety
device should be installed to guard against
accidents that may result in injury, death, or
damage to the system.
• When the unit is to be used for an elevator, install a
safety device on the elevator side to prevent it from
falling; otherwise, serious injury, death, or damage
to the elevator may result.
CAUTION:
• Operate the unit only within its design and
performance specifi cations; otherwise, injury or
damage to the system may occur.
• Keep hands and all foreign objects from the
internal moving parts of the unit; otherwise, injury
or damage to the system may occur.
• Take damaged units off -line immediately and do
not resume operation until properly repaired.
• Modifi cations or alterations of any kind to the unit
will void the warranty and all subsequent claims.
• Do not remove the rating plate.
Disposal
Please refer to local, state, and federal regulations governing
disposal of:
Steel Scrap:
• Housing (Ductile and Gray Cast Iron)
• Gears
• Shafts
• Bearings
Lubricants:
• Gear Oil
• Grease
Summary of Contents for FAST-WAY Si-Low 210 A1
Page 3: ...1 1 2 2 3 3 4 4 A A B B C C D D Si Low 210 A1 1...
Page 4: ...IDEAL MANUFACTURING INC 440 460 VOLT THREE PHASE...
Page 5: ...IDEAL MANUFACTURING INC 240 VOLT THREE PHASE...
Page 38: ......
Page 39: ......
Page 40: ......
Page 41: ......
Page 42: ......
Page 43: ......
Page 44: ......
Page 45: ......
Page 46: ......
Page 47: ......
Page 48: ......
Page 49: ......
Page 50: ......
Page 51: ......
Page 52: ......
Page 53: ......
Page 54: ......
Page 55: ......
Page 56: ......
Page 57: ......
Page 58: ......
Page 59: ......
Page 60: ......
Page 61: ......
Page 62: ......
Page 63: ......
Page 64: ......
Page 65: ......
Page 66: ......
Page 67: ......
Page 68: ......
Page 69: ......
Page 70: ......
Page 71: ......
Page 72: ......
Page 73: ......
Page 74: ......
Page 75: ......
Page 76: ......
Page 77: ......
Page 78: ......
Page 79: ......
Page 80: ......
Page 81: ......
Page 82: ......
Page 83: ......
Page 84: ......
Page 85: ......
Page 86: ......
Page 87: ......