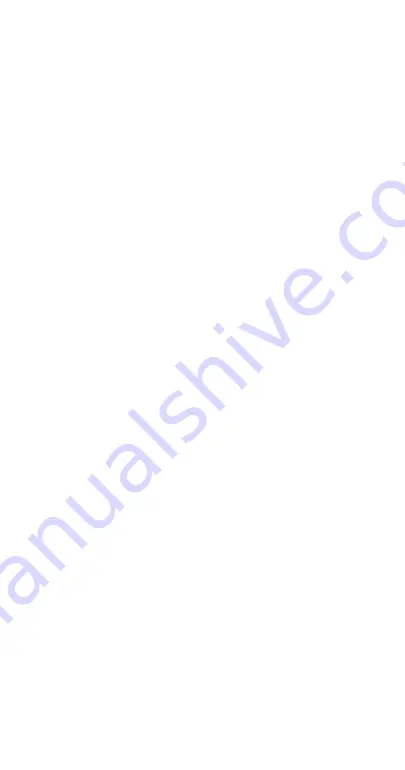
INSTALLATION/VISUAL INSPECTION CHECKLIST
Ice machine is not level
• Level the ice machine
Condenser is dirty
• Clean the condenser
Water filtration is not installed or plugged
• Install a new water filter
Water drains are not run separately and/or are not
vented
• Run and vent drains according to the Installation
Manual
11
2
Summary of Contents for WU-0100A
Page 1: ...Undercounter Ice Machines Technician s Handbook Revision Date 1 24 22...
Page 2: ......
Page 14: ...THIS PAGE INTENTIONALLY LEFT BLANK...
Page 17: ...16 How to Read a Serial Number Full Serial Number...
Page 154: ...WU 0100 WIRING DIAGRAM Self Contained Air cooled 153...
Page 155: ...IC 0170 IU 0170 IC 0220 IU 0220 WIRING DIAGRAM Self Contained Air cooled 154...
Page 156: ...Printed Circuit Bards PCB WU 0100 PCB 155...
Page 161: ...SPACE FOR TECHNICIAN S NOTES...
Page 162: ...SPACE FOR TECHNICIAN S NOTES...
Page 163: ...SPACE FOR TECHNICIAN S NOTES...
Page 164: ...SPACE FOR TECHNICIAN S NOTES...
Page 165: ......