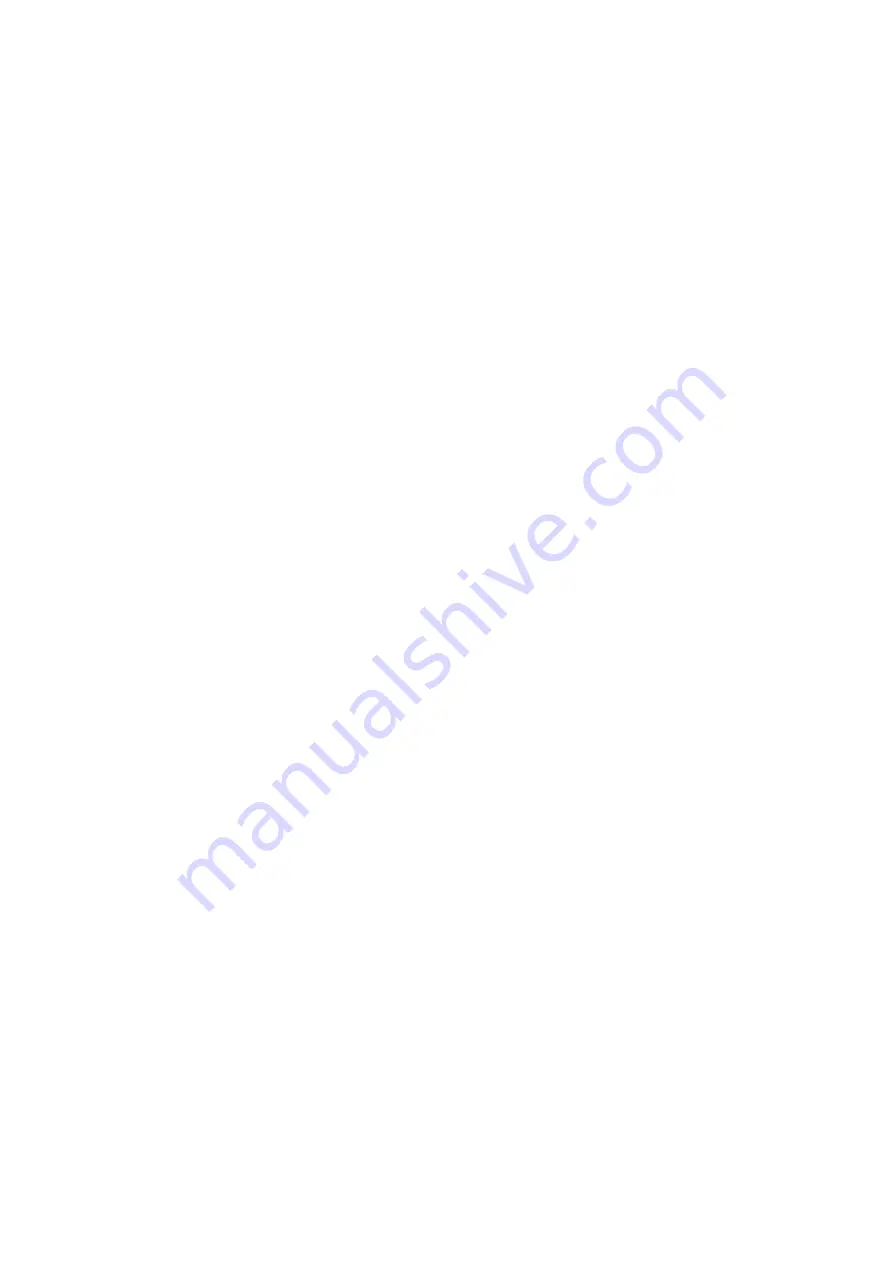
AS1041TC-CL
Page
15
Important Installation Details
The control valve, fittings and/or bypass are designed
to accommodate minor plumbing misalignments but
are not designed to support the weight of the system
or the plumbing.
Do no use Vaseline, oils, other hydrocarbon lubricants
or spray silicone anywhere. A silicone lubricant may
be used on black o-rings but is not necessary.
Avoid
any type of lubricants, including silicone, on the
clear lip seals.
The nuts and caps are designed to be unscrewed or
tightened by hand or with the special plastic wrench.
Do not use a pipe wrench to tighten or loosen nuts or
caps. Do not place a screwdriver in the slots on caps
and/or tap with a hammer.
Do not use pipe dope or other sealant on threads.
Use teflon tape on threaded inlet, outlet and drain
fittings.Teflon tape is not necessary on the nut
connection or caps because of o-ring seals.
After completing any valve maintenance involving
the drive assembly of the drive camp assembly
and pistons, unplug power source jack from the
circuit board (black wire) and plug back in
. This
resets the electronics and establishes the service
piston position. The display should flash and then
reset the valve to the service position if necessary.
All plumbing should be done in accordance with local
plumbing codes. The pipe size for the drain line
should be a minimum of 12mm inside diameter.
Solder joints near the drain must be done prior to
connecting the drain line flow control fitting. Leave at
least 150mm (6”) between the drain line control fitting
and solder joints when soldering pipes that are
connected on the drain line control fitting. Failure to
do this could cause interior damage to the drain line
flow control fitting.
When assembling the installation fitting package (inlet
and outlet), connect the fitting to the plumbing system
first and then attach the nut, split ring and o-ring.
Heat from soldering or solvent cements may damage
the nut, split ring and o-ring. Solder joints should be
cool and solvent cements should be set before
installing the nut, split ring or o-ring. Avoid getting
primer and solvent cement on any part of the o-rings,
bypass valve or control valve.
Position the softener within 1½ metres of a 10 amp
GPO. The transformer is connected into the plug
socket on the back of the valve control panel. Do not
drop the transformer or have the cable too taut. The
transformer is only suitable for
internal use only
.
The softener must be weather protected.
For full understanding of the water softener we
recommend that the instruction manual be fully read
before installation and commissioning of the softener
by undertaken.
IMPORTANT:
A
NUMBER
OF
VALVE
COMPONENTS ARE LOCKED INTO POSITION
WITH
EASILY
REMOVABLE
CLIPS
.
ENSURE ALL LOCKING CLIPS ARE CORRECTLY
IN POSITION BEFORE PRESSURISING THE
SOFTENER. ENSURE THAT IT IS POINTED OUT
TO ALL RELEVANT PERSONNEL THAT THE
LOCKING CLIPS MUST NOT BE REMOVED
WHILST THE SYSTEM IS UNDER WATER
PRESSURE.
Note: All electrical connections must be connected
according to local codes.
Install grounding strap on metal plates.
Bypass Valve
The bypass valve is typically used to isolate the
control valve from the plumbing system’s water
pressure in order to perform control valve repairs or
maintenance. The WS1 bypass valve is particularly
unique in the water treatment industry due to its
versatility and state of the art design features. The
full flow bypass valve incorporates four positions,
including a diagnostic position that allows service
personnel to work on a pressurised system while still
providing untreated bypass water to the facility or
residence. Its completely non-metallic, all plastic
design allows for easy access and serviceability
without the need for tools.
The bypass body and rotors are glass filled Noryl (or
equivalent) and the nuts and caps are glass filled
polypropylene. All seals are self-lubricating EPDM to
help prevent valve seizing after long periods of non-
use. Internal o-rings can easily be replaced if service
is required.
The bypass consists of two interchangeable plug
valves that are operated independently by red arrow-
shaped handles. The handles identify the flow
direction of the water. The plug valves enable the
bypass valve to operate in four positions.
1.
Normal Operation Position
: The inlet and outlet
handles point in the direction of flow indicated by
the engraved arrows on the control valve. Water
flows through the control valve during normal
operation and this position also allows the control
valve to isolate the media bed during the
regeneration cycle. (Figure 1)
2.
Bypass Position
: The inlet and outlet handles
point to the centre of the bypass, the control
valve is isolated from the water pressure
contained in the plumbing system. Untreated
Summary of Contents for AST1041TC-CL
Page 3: ...AS1041TC CL Page 3...
Page 7: ...AS1041TC CL Page 7 Note Maximum number of days that can be selected is 99...
Page 23: ...AS1041TC CL Page 23 SPARE PARTS AND SERVICING INSTRUCTIONS...
Page 32: ...AS1041TC CL Page 32 flow diagram backwash Flow Diagram Down flow Brine...
Page 33: ...AS1041TC CL Page 33 flow diagram downflow brine Flow Diagrams Rinse and Fill...
Page 34: ...AS1041TC CL Page 34 flow diagram rinse flow diagram fill WS1 Wrench Order No V3193 01...
Page 41: ...AS1041TC CL Page 41...