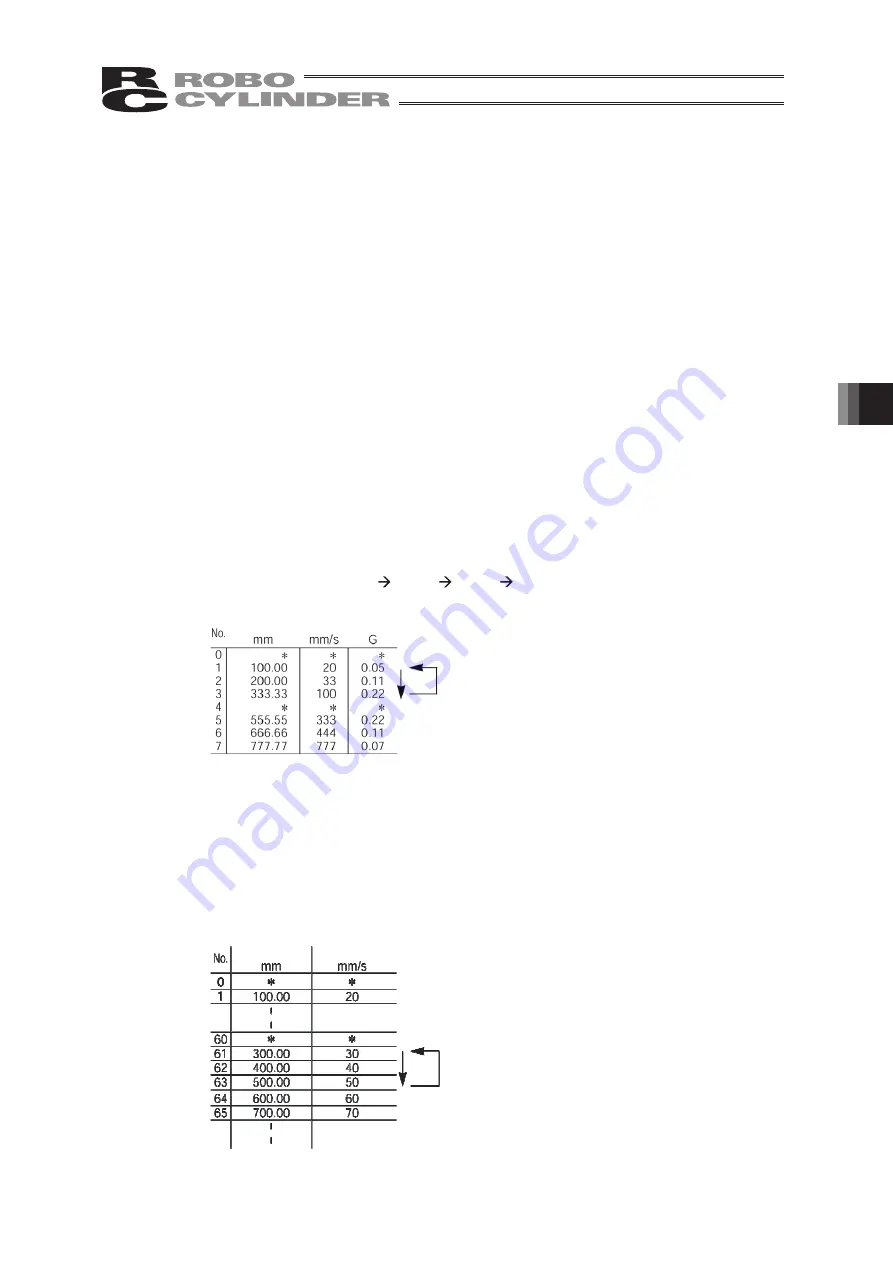
66
67
6.
Operation:
Mode
Flow
Chart
6.5.6 Move
You may move towards a position registered in the position data table (1 step move)
and continuously move through the continuous position data.
In this section, the move will differ from jog and increment move used with the arrow key.
This will be moved towards a position that was registered in the position data table within the
Use this move for test operation etc.
(1) Move
1 step move from the current location to the assigned position number registered
in the position table.
(2) Continuous Continuous operation from the assigned position data number to the continuous
position data number until an empty location is reached.
* What is Continuous?
In the case of the position data similar to the table below, when a Continuous
command is executed from the position No., the place where data exists
continuously (to the position before unregistered data (*)) will operate as one group
No. 3
(Example: Position No.2
No. 1
No.2 and so on).
Posi.
Vel. Acc./Dcc.
In the case of the Teaching Pendant, continuous movement is performed only
through 64 positions such as position No. 0-63 and No. 64-127.
As shown in the example below, continuous movement continues by returning to
position No. 61 after No. 63 (returning to the first position No. where position data is
No movement is made from position No. 63 to No. 64.
Position
Velocity
continuously input).
controller.
Summary of Contents for Robo Cylinder CON-T
Page 1: ...Teaching Pendant Instruction Manual Tenth Edition CON T CON TG CON TGS IAI Corporation ...
Page 2: ......
Page 4: ......
Page 8: ......
Page 18: ... ...
Page 24: ...14 4 Functions and Specications of Teaching Pendant 4 2 External View External Dimensions ...
Page 97: ...87 6 Operation Mode Flow Chart Examples of PCON CY Controller On following page ...
Page 98: ...88 6 Operation Mode Flow Chart From previous page On following page ...
Page 99: ...89 6 Operation Mode Flow Chart From previous page On following page ...
Page 100: ...90 6 Operation Mode Flow Chart From previous page ...
Page 117: ......