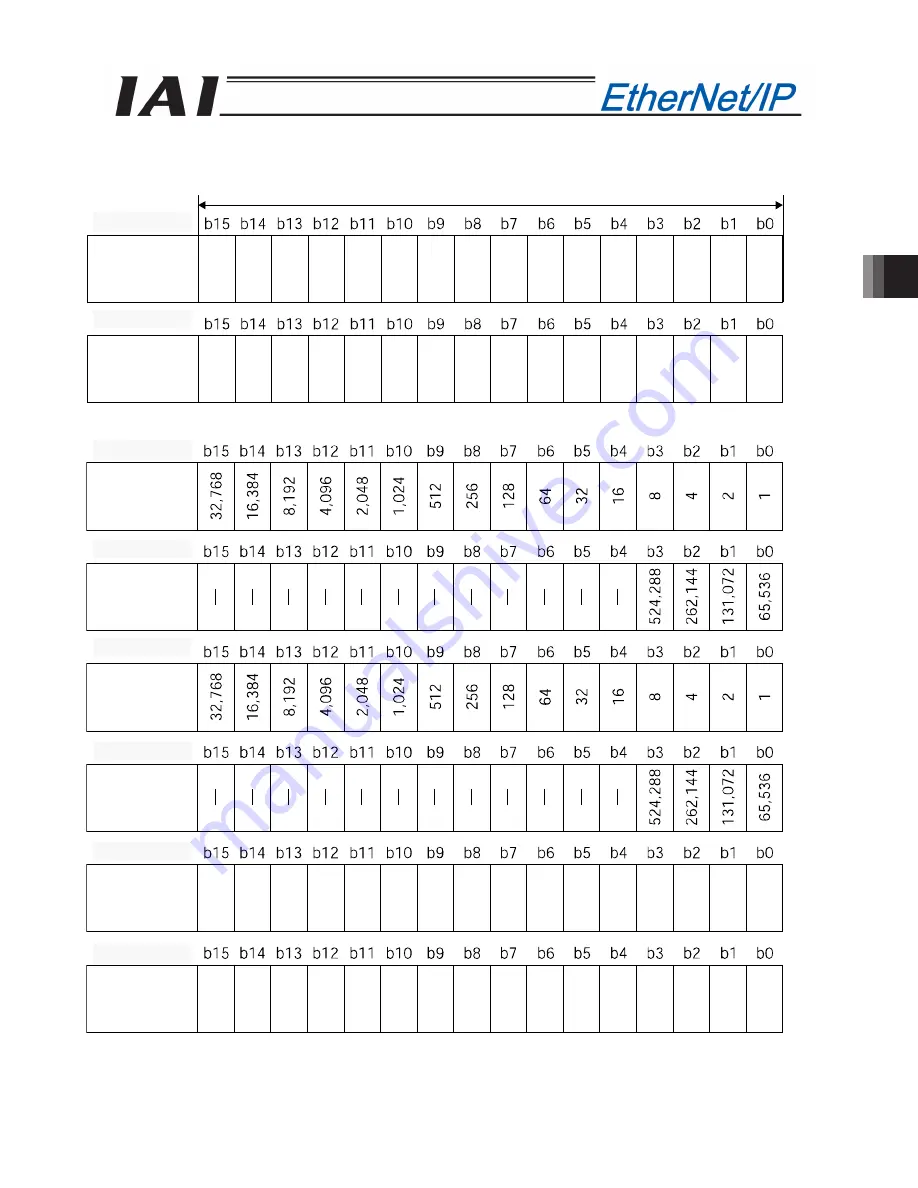
4. SCON-CA
191
PLC output
Address (* “n” indicates the node address of each axis.)
When the target position is shown using the negative figure, it is expressed using the complement of 2.
When the zone boundary is shown using the negative figure, it is expressed using the complement of 2.
n+4
ޔ
n+5
n+6
ޔ
n+7
n+8
ޔ
n+9
n+10
ޔ
n+11
n+12
ޔ
n+13
n+14
ޔ
n+15
Positioning
band
(lower word)
Positioning
band
(upper word)
Speed
(lower word)
Speed
(upper word)
Zone
bo
(lower word)
Zone
bo
(upper word)
n+14, n+15
n+12, n+13
n+10, n+11
n+8, n+9
n+6, n+7
n+4, n+5
1 word = 2 bytes =16 bits
n+0
ޔ
n+1
n+2
ޔ
n+3
Target
position
(lower word)
Target
position
(upper word)
n+2, n+3
n+0, n+1