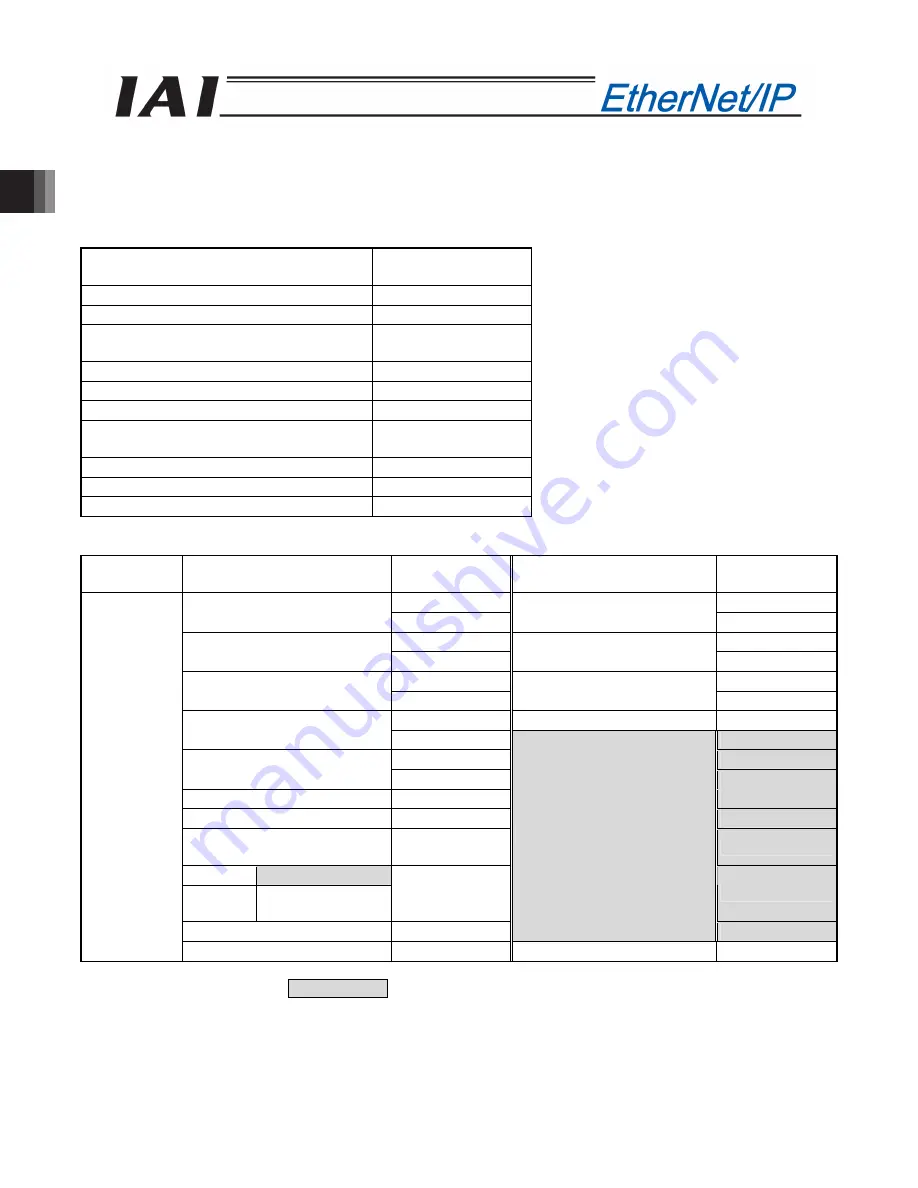
2.
ACON-C/CG, PCON-C/CG
40
2.6.5
Full Direct Value Mode (Number of Occupied Bytes: 32)
This is the operation mode with all the values (target position, speed, etc.) set up directly using values from
PLC. Set each value in the I/O area.
The robot cylinder's effective main functions that can be controlled using this mode, are as shown in the
following table.
ROBO cylinder function
{
: Direct control
x: Disable
Home-return operation
{
Positioning operation
{
Speed and acceleration / deceleration
setting
{
Pitch feed (inching)
{
Pressing operation
{
Speed change during the movement
{
Operation at different acceleration and
deceleration
{
Pause
{
Zone signal output
{
PIO pattern selection
x
(1) PLC address configuration (* "n" indicates the first address of each axis.)
Parameter
No.84
ACON/PCON side
input register
PLC side output
address (bytes)
ACON/PCON side
output register
PLC side input
address (bytes)
n, n+1
n, n+1
Target position
n+2, n+3
Current position
n+2, n+3
n+4, n+5
n+4, n+5
Positioning band
n+6, n+7
Command current
n+6, n+7
n+8, n+9
n+8, n+9
Speed
n+10, n+11
Current speed
n+10, n+11
n+12, n+13
Alarm code
n+12, n+13
Zone bo
n+14, n+15
n+14, n+15
n+16, n+17
n+16, n+17
Zone boundary -
n+18, n+19
n+18, n+19
Acceleration
n+20, n+21
n+20, n+21
Deceleration
n+22, n+23
n+22, n+23
Pressing current-limiting
value
n+24, n+25
n+24, n+25
ACON
Occupied area
PCON
Load current
threshold
n+26, n+27
n+26, n+27
Control signal 1
n+28, n+29
Occupied area
n+28, n+29
3
Control signal 2
n+30, n+31
Status signal
n+30, n+31
(Note) The areas denoted by Occupied area cannot be used for any other purpose.
Also, exercise caution to avoid node address duplication.