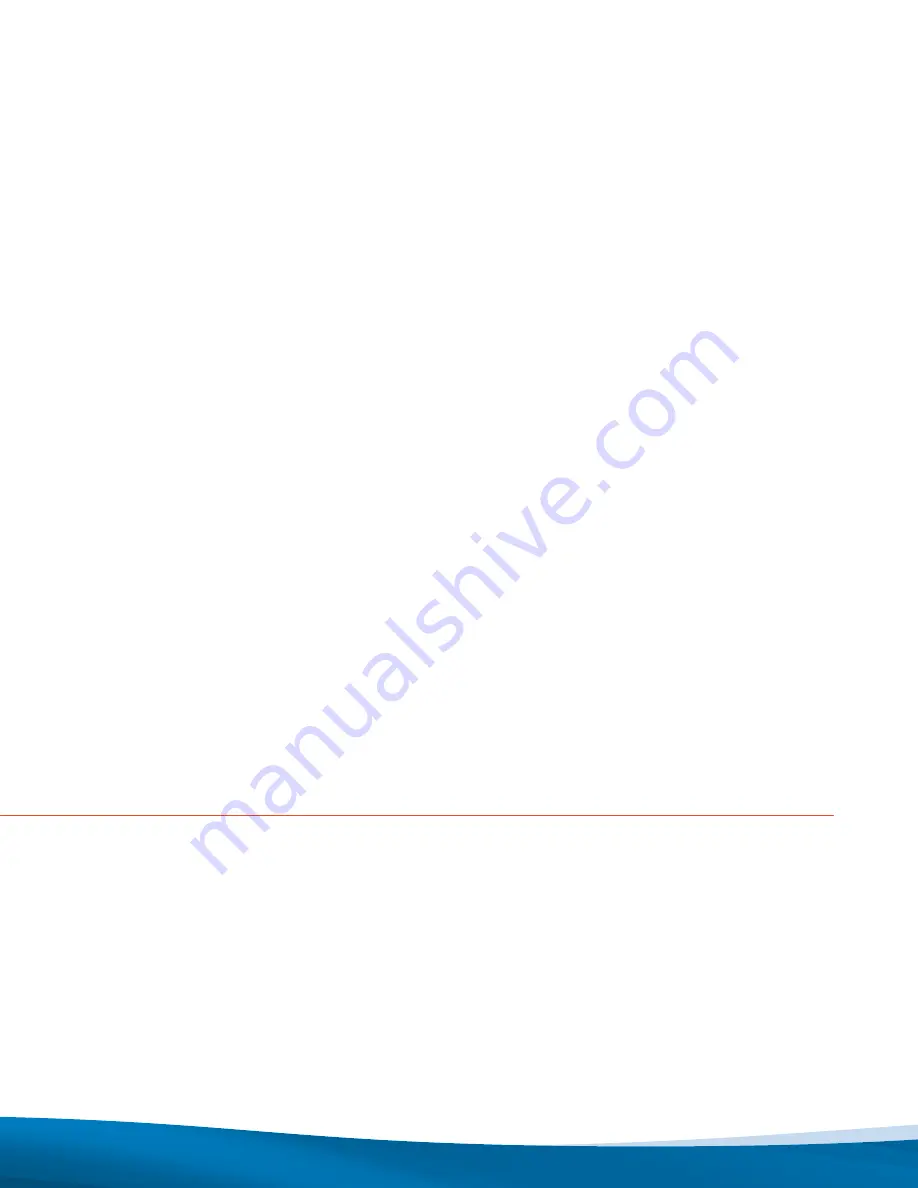
36
A complete test of the system can be accomplished with the connection of a resistive fault between one of the three
lines and ground at a location downstream of one of the feeder current sensors. This simple test will identify the integ-
rity of sensor, feeder module circuits, connections, communications, system module operation, DDR2 resistor OHM-
NI-PM resistor and pulsing without causing a trip to occur on any of the breakers. The only thing it will not test is the
priority of the double-fault trip process. For this two such resistors would be required, with resistor value low enough to
provide more than the 100A trip current required for the selective second ground fault tripping.
DANGER
Never use a piece of wire to create a test fault. It is possible that the protection may not be operational due to mis-
wiring or other problems and cannot clear the fault current resulting in a serious arcing situation which may severely
damage the equipment and cause injury or death.
Secondary injection testing is possible using low current sources to test the feeder modules. It is recommended to use
currents of 1/1000 of the expected circuit current through the zero sequence current sensor. Because there are inter-
locking signals from the system module that prevent feeder module trip and indication, then it is necessary to either
apply a voltage to the N-G terminals of the system module, or simply pull one of the DDR2 fuses to drive the system
module into the alarm condition thus enabling the feeder modules to provide indication and digital trip functionality.
Note: Should the injection current induced during this procedure exceed 100mA then the feeder module will trip on the
analog backup circuit without any indication at all.
Service
I-Gard offers comprehensive training, commissioning and inspection assistance by qualified engineers. For assis
-
tance with installation, set-up or testing, please call I-Gard toll free at 1-888-737-4787 (1-888-RESISTR). There are no
user-serviceable parts in the DSP, therefore all service should be referred to qualified factory representatives, other
than direct replacement of entire modules to I-Gard. Please visit the I-Gard website at www.i-gard.com for information
regarding field service representatives in your area.
Note: Please ensure that proper authorization is obtained from I-Gard before returning any equipment.
8. COMMUNICATIONS
Installation
To allow communications to a remote terminal or network, a 4-wire RS-485 communications jack and Ethernet con
-
nector are provided at the side of the DSP-TDM display module. The 5-pin connector supplied has screw terminals
and allows disconnection without breaking the RS-485 daisy chain. A ground connection is supplied for grounding the
shield of the 4-wire cable. The protocol supported is MODBUS RTU. The baud rate can be changed in the DSP-TDM
set-up from 9600 to 256000 as desired. The frame set-up is 5 to 8 bit, parity NONE, EVEN, ODD, MARK or SPACE
and 1, 1.5 or 2 stop bits. The I/D number for the DSP-TDM must be entered in the set-up within the range of 1 to 255.
Cable should be standard 4-wire with two twisted-pairs and a grounding shield for electro-magnetic coupling protec-
tion. The shield of the cable between nodes should not be continuously grounded, but each section of cable should
be grounded at GND pin of J3. When installing cable, avoid star connections and make connections flow from node to
node. Cable length of 1-2 kilometers or more should be easily accommodated.
should be disconnected prior to removing covers or enclosures and where live conductors may otherwise be exposed.
Failure to observe these precautions may result in death or severe personal injury and damage to equipment. Before
placing an intentional ground fault on the power system, check that a fault does not already exist. Any test ground fault
equipment must be rated for full system voltage and be fused for protection.
Summary of Contents for DSP-OHMNI
Page 1: ...C EG30EM Instruction Manual V2 June 2020 DSP OHMNI ...
Page 11: ...9 Figure 1b DSP DCM Wiring Figure 1c System Module DSP DSM Wiring ...
Page 12: ...10 Figure 1d Power Supply DSP DPS Wiring Figure 2 Preferred Feeder Module DSP DFM Wiring ...
Page 45: ...43 Figure 41 DSP DPS System Module Connection ...
Page 46: ...44 Figure 43 DSP DLM Logging Module Connections Figure 44 DSP TDM Display Module Connections ...
Page 47: ...45 Figure 45 Typical DSP DRM Installation Connections ...
Page 50: ...www i gard com Phone 905 673 1553 Toll Free 1 888 737 4787 Fax 905 673 8472 sales i gard com ...