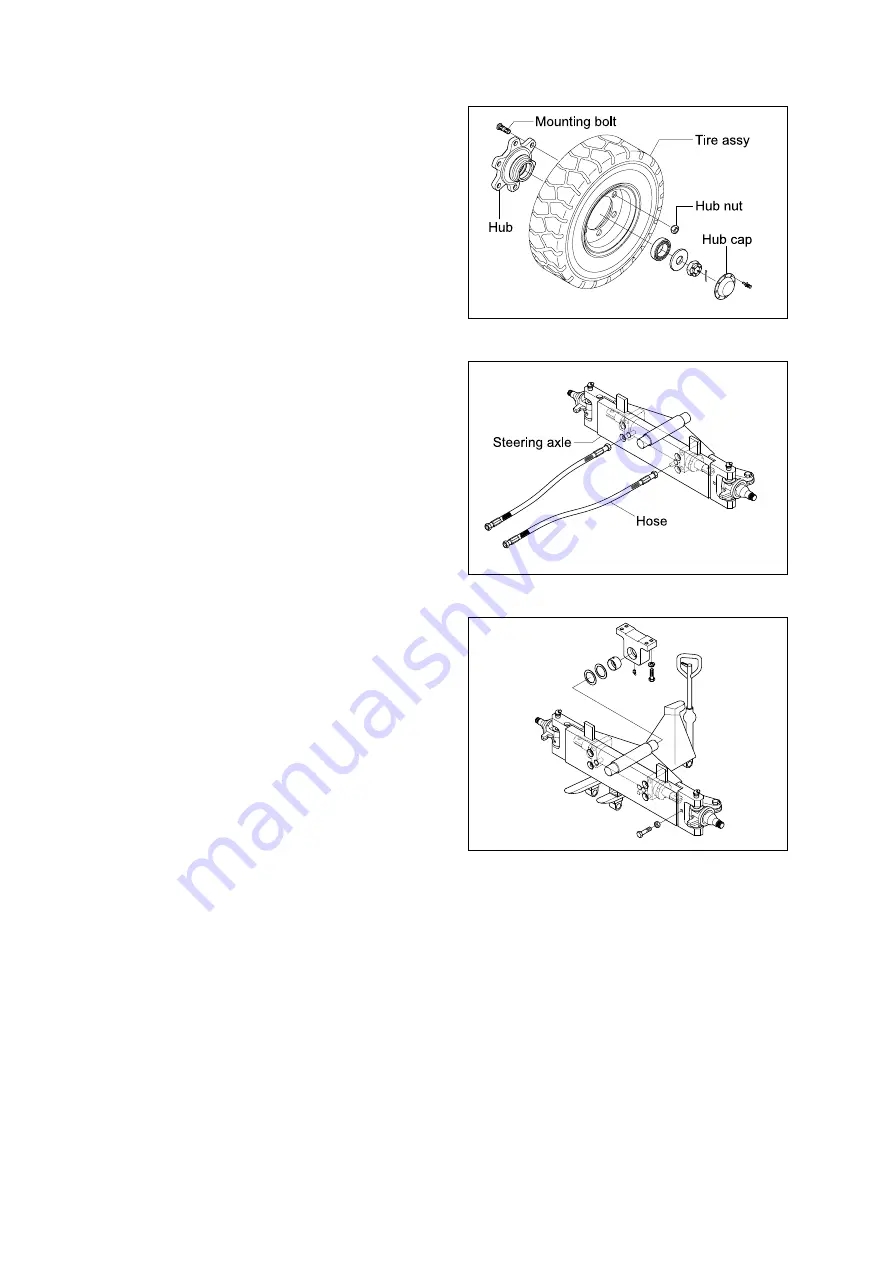
2-19
Rear wheel
Remove mounting bolt and hub nut with
socket wrench and then carefully take out
the tire assembly.
(2)
D503RE31
Hose
(3)
D503RE32
Mounting bolt
Put a block under the steering axle,
support on a truck, an raise the frame with
a crane. Remove the mounting bolts
installing to the frame, and pull out to the
rear.
There are shims between the support and
steering axle to prevent play.
(4)
D503RE33
https://www.forkliftpdfmanuals.com/
Summary of Contents for HDF 50-7S
Page 2: ...https www forkliftpdfmanuals com ...
Page 282: ...7 3 2 HDF50 70 7 https www forkliftpdfmanuals com ...
Page 283: ...7 3 MEMORANDUM https www forkliftpdfmanuals com ...
Page 316: ...https www forkliftpdfmanuals com ...
Page 318: ...https www forkliftpdfmanuals com ...
Page 330: ...https www forkliftpdfmanuals com ...
Page 353: ...3 1 SERVICE TOOLS 1 Special tool 3 2 https www forkliftpdfmanuals com ...
Page 360: ...https www forkliftpdfmanuals com ...
Page 378: ...https www forkliftpdfmanuals com ...
Page 408: ...https www forkliftpdfmanuals com ...
Page 428: ...https www forkliftpdfmanuals com ...
Page 506: ...ELECTRICAL SYSTEM 12 28 Installing alternator S6S Y3T62HF https www forkliftpdfmanuals com ...
Page 508: ...https www forkliftpdfmanuals com ...