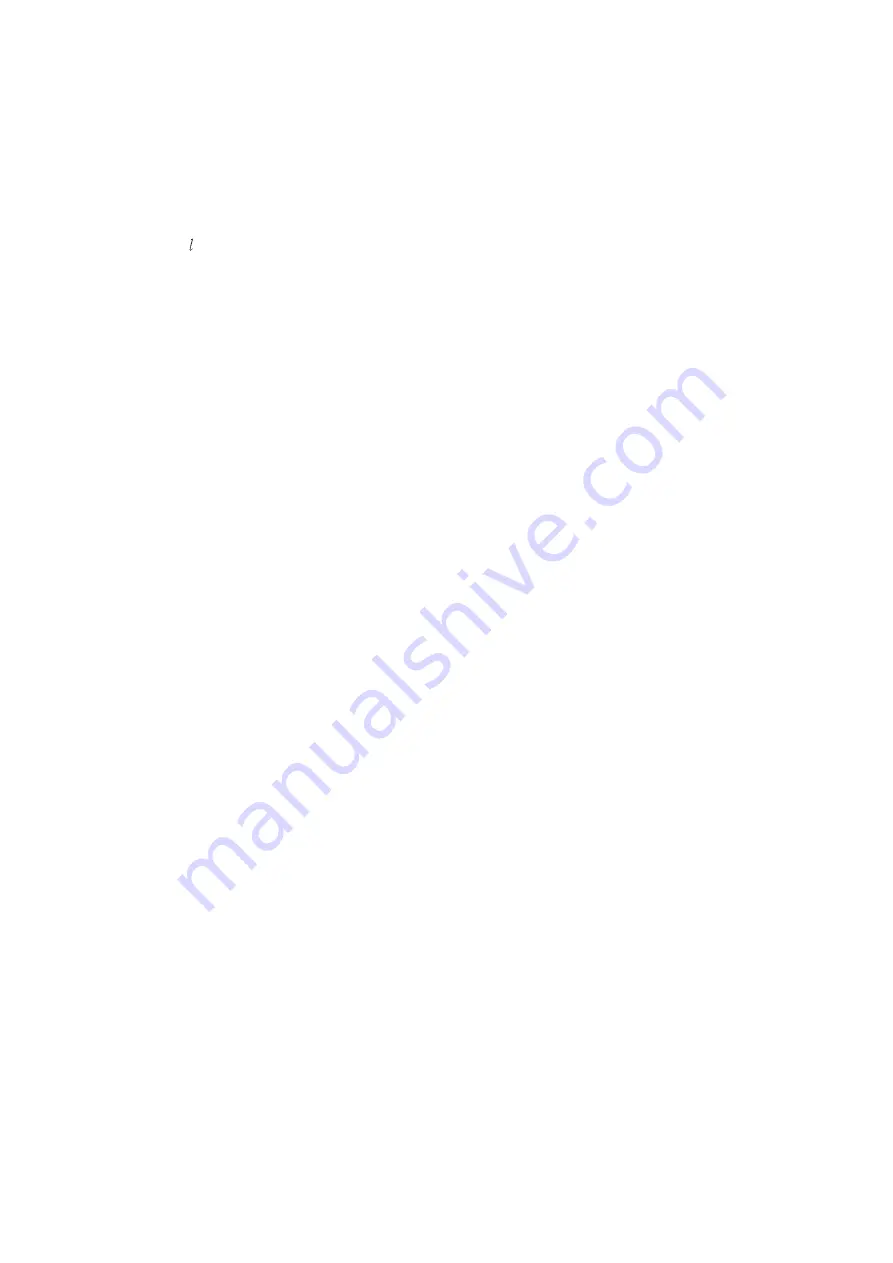
3-11
Transmission control, see schedule of measuring points, Oil circuit diagram and Electro-hydraulic
control unit see page 3-2, 3-10.
The transmission pump, necessary for the oil supply of the converter, and for the transmission
control, is sitting in the transmission on the engine-dependent input shaft.
The feed rate of the pump is
Q = 85 /min, at n
Motor
= 2000 min
-1
This pump is sucking the oil via the coarse filter out of the oil sump and delivers it via the fine filter -
the filter can also be fitted externally from the transmission - to the main pressure valve.
If because of contamination, resp. damage, the through-flow through the fine filter is not ensured,
the oil will be directly conducted via a filter differential pressure valve(bypass valve
¡
p = 5.5+3bar)
to the lubrication.
In this case, an error indication is shown on the display.
The five clutches of the transmission are selected via the 6 proportional valves P1 to P6(P1 will not
be under current at the 3-speed version, i.e. without function).
The proportional valve(pressure regulator unit) is composed of pressure regulator(e.g. Y6), follow-
on slide and vibration damper.
The control pressure of 9 bar for the actuation of the follow-on slides is created by pressure
reducing valve. The pressure oil(16+2bar) is directed via the follow-on slide to the respective clutch.
Due to the direct proportional selection with separated pressure modulation for each clutch, the
pressure to the clutches, which are engaged in the gear change, will be controlled. In this way, a
hydraulic intersection of the clutches to be engaged and disengaged becomes possible.
This is creating spontaneous shftings without traction force interruption.
At the shifting, the following criteria will be considered :
- Speed of engine, turbine, central gear train and output.
- Transmission temperature.
- Shifting mode(up-,down-, reverse shifting and speed engagement out of Neutral).
- Load condition(full and part load, traction, overrun inclusive consideration of load cycles during the
shifting).
The main pressure valve is limiting the max. control pressure to 16+2.5bar and releases the main
stream to the converter and lubrication circuit.
In the inlet to the converter, a converter safety valve is installed which protects the converter from
high internal pressures(opening pressure 11+2bar).
Within the converter, the oil serves to transmit the power according to the well-known hydrodynamic
principle(see Chapter torque converter page 3-3).
To avoid cavitation, the converter must be always completely filled with oil.
https://www.forkliftpdfmanuals.com/
Summary of Contents for HDF 50-7S
Page 2: ...https www forkliftpdfmanuals com ...
Page 282: ...7 3 2 HDF50 70 7 https www forkliftpdfmanuals com ...
Page 283: ...7 3 MEMORANDUM https www forkliftpdfmanuals com ...
Page 316: ...https www forkliftpdfmanuals com ...
Page 318: ...https www forkliftpdfmanuals com ...
Page 330: ...https www forkliftpdfmanuals com ...
Page 353: ...3 1 SERVICE TOOLS 1 Special tool 3 2 https www forkliftpdfmanuals com ...
Page 360: ...https www forkliftpdfmanuals com ...
Page 378: ...https www forkliftpdfmanuals com ...
Page 408: ...https www forkliftpdfmanuals com ...
Page 428: ...https www forkliftpdfmanuals com ...
Page 506: ...ELECTRICAL SYSTEM 12 28 Installing alternator S6S Y3T62HF https www forkliftpdfmanuals com ...
Page 508: ...https www forkliftpdfmanuals com ...