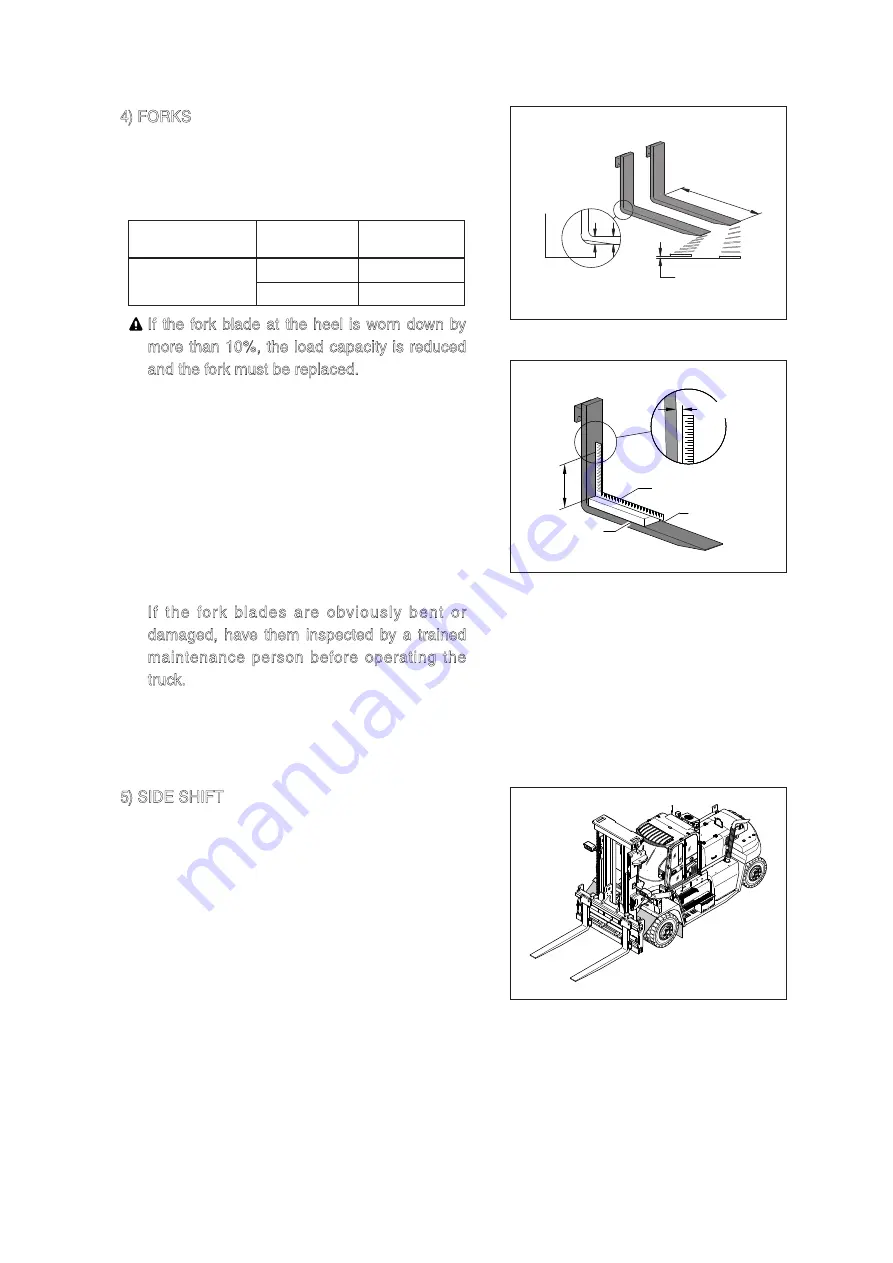
7-16
FORKS
Inspect the load forks for cracks, breaks, bending,
and wear. The fork top surfaces should be level
and even with each other. The height difference
between both fork tips refer to below table.
4)
Carpenter square
Blade
Metal block
Shank
12.5mm MAX
500mm
110D9OM151
If the fork blade at the heel is worn down by
more than 10%, the load capacity is reduced
and the fork must be replaced.
Inspect the forks for twists and bends. Put a 50
mm (2 in) thick metal block, at least 100 mm (4 in)
wide by 600 mm (24in) long with parallel sides, on
the blade of the fork with the 100 mm (4 in) surface
against the blade. Put a 600 mm (24 in)
carpenter's square on the top of the block and
against the shank. Check the fork 500 mm (20 in)
above the metal block to make sure it is not bent
more than 12.5 mm (0.5 in) maximum.
If the fork blades are obviously bent or
damaged, have them inspected by a trained
maintenance person before operating the
truck.
Inspect the fork locking pins for cracks or
damage. Reinsert them and note whether they fit
properly.
ö
Height difference
10% of "A" is
max. wear
allowed
A
B
300D9OM150
SIDE SHIFT
When operating the lever for the side shift and the
hanger bar which the forks and the backrest are
mounted on it, operator can accurately insert the
forks under pallets or stack loads correctly without
moving the fork lift.
5)
160D9LOM154
Model
Fork length (B)
(mm)
Height
difference (mm)
160D-9L, 180D-9B
below 1500
3
above 1500
6