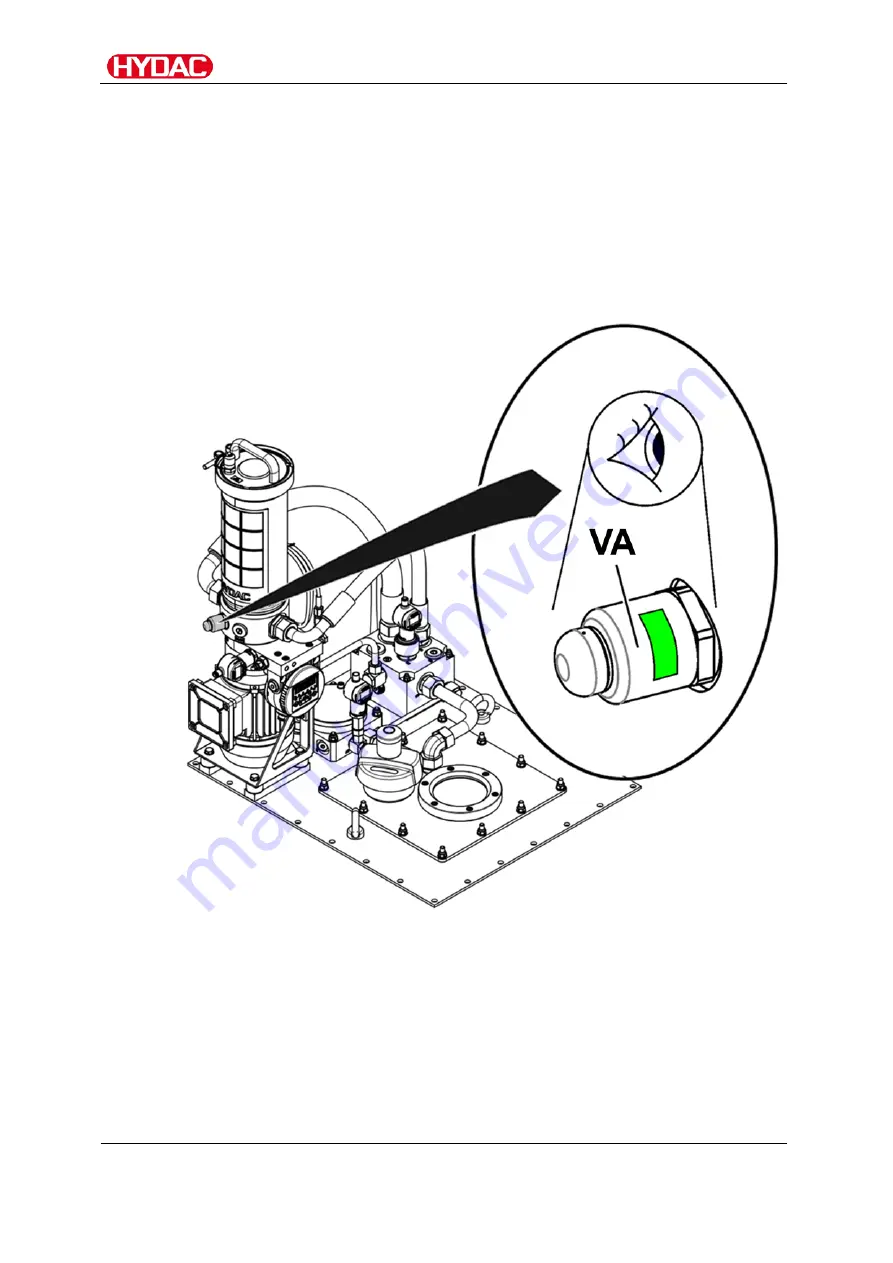
Performing Maintenance
OXiStop OXS-LID
en
Page 70 / 112
MoWa OXS-LID 3992764e en-us 2018-08-10.docx
2018-08-10
Checking the visual clogging indicator on the bypass flow filtration unit
The OLF 5 bypass flow filtration unit is equipped with an optical or electric
clogging indicator for monitoring the degree of contamination.
Replace the filter element when the red marking becomes visible in the
clogging indicator. For details, refer to chapter "Replace the filter element on
the OLF 5 bypass flow filtration element" on page 71.