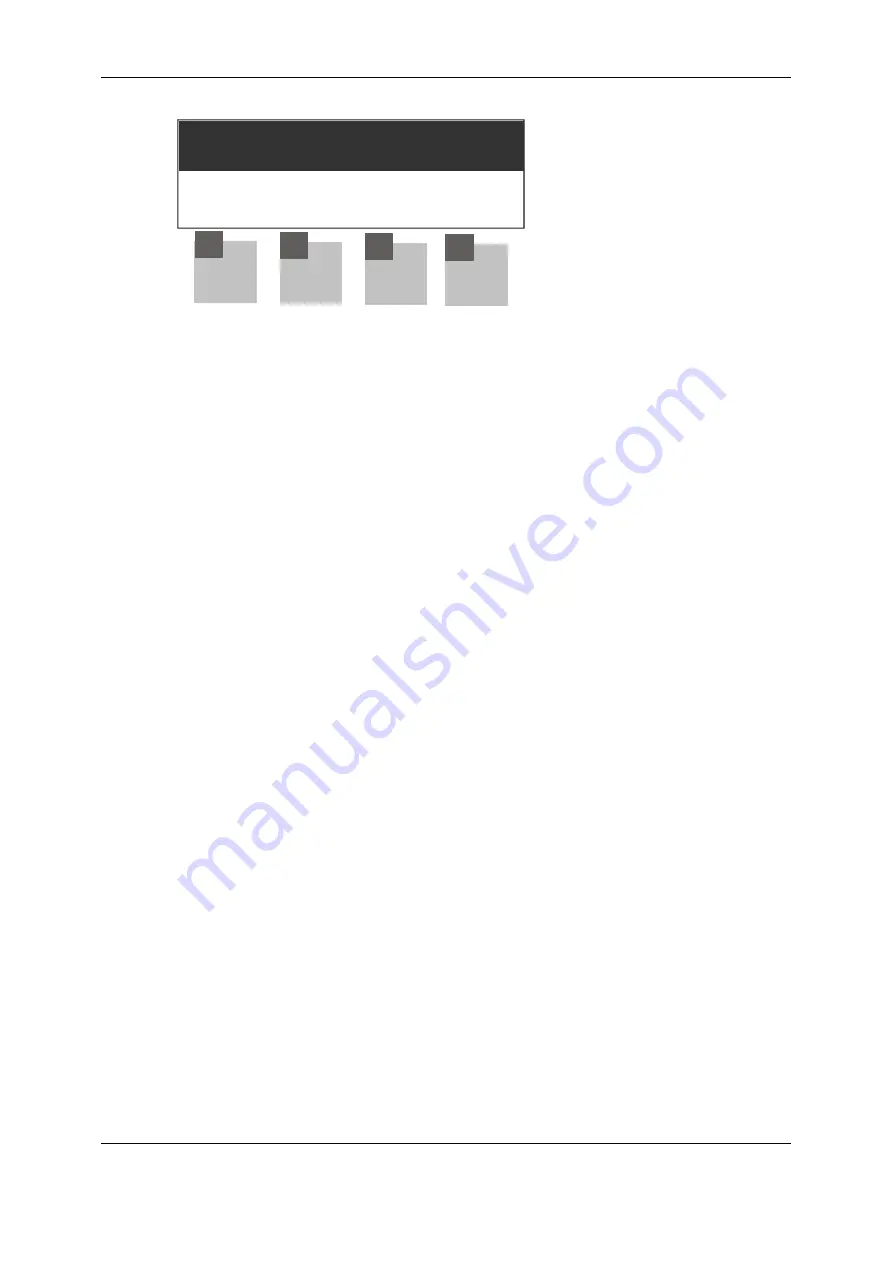
FluidAqua Mobil – FAM 10/15 +AS1000
Starting up the FAM
HYDAC Filtertechnik GmbH
en
Page 31 / 80
Start screen
F1
F2
F3
F4
F1 = Start FAM
F2 = Stop
F3 = Reset (after malfunction)
F4 = Switch to MENU1
Ready for operation, please press Start
Operating mode: D Filter
MENU1
START
START
= Is displayed only in the operating status "Ready for op-
eration".
After this key has been pressed, the current operating
status on the display switches to "Starting phase" and
the "RF+D" screen appears.
STOP
= Is shown during the starting phase and during automatic
operation.
RESET
= Is displayed only when there is a fault
The most recently selected operating mode will always be shown in the start screen.
BEWA FAM10 3417360 en.doc
2008-06-06