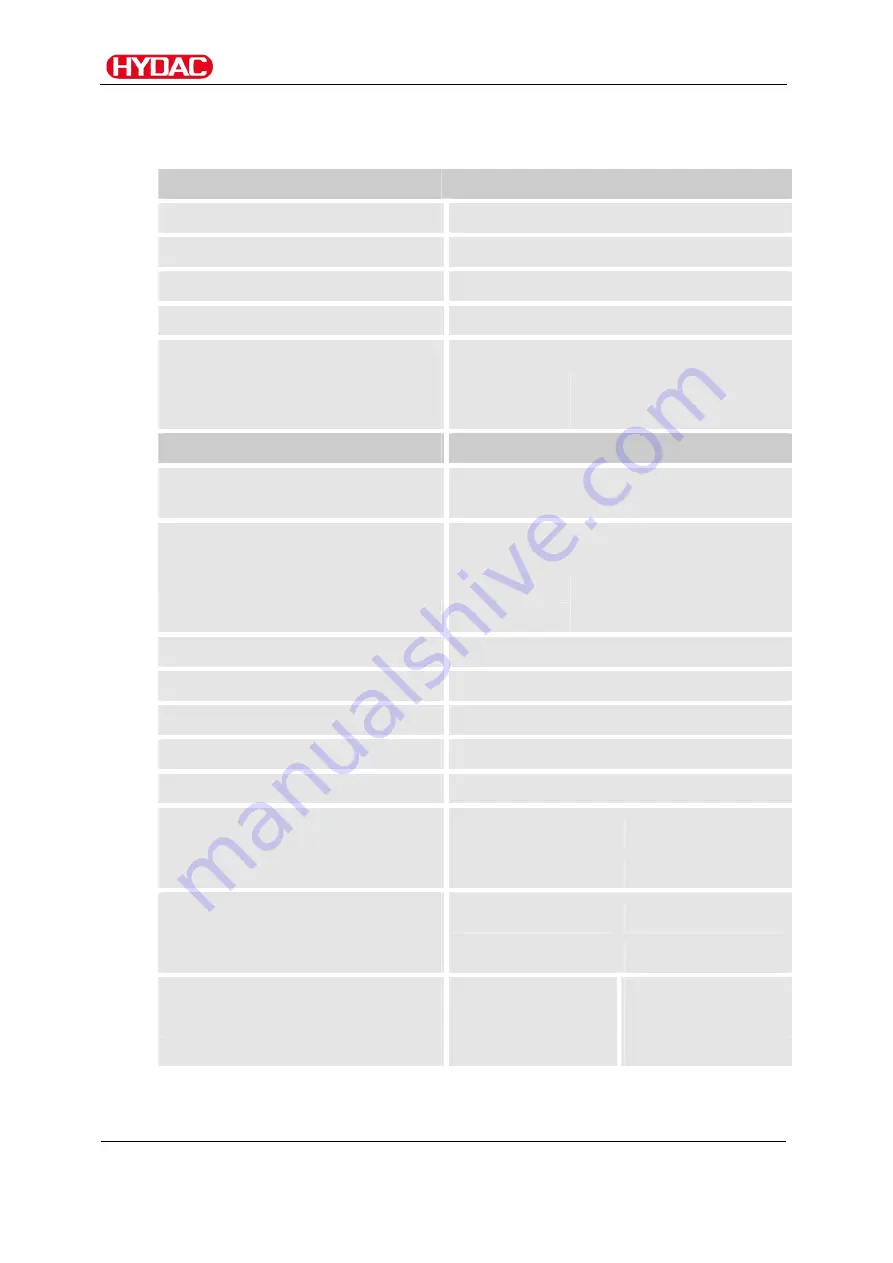
Technical details
CMP1000
en(us)
Page 39 / 44
MoWa CMP 3528418d en-us 2015-01-06.doc
2015-01-06
Technical details
General data
Hydraulic fluid temperature
0 … 70°C / 32 … 158°F
ambient temperature
0 … 50°C / 32 … 122°F
Storage temperature
-40°C … 80°C / -40°F … 176°F
Relative humidity
max. 90%, non-condensing
Weight
CMP1xx0-2 ~25 kg
CMP1xx0-4 ~25 kg
Hydraulic data
Permissible suction pressure at
suction port connection (IN)
- 0.4 bar … 80 bar
Pressure at return port connection
(OUT)
CMP1xx0-2 0.5 bar max.
CMP1xx0-4 5 bar max.
Pump type
Gear pump
Max suction height
500 mm
Sealing material
NBR
Suction port (IN)
G ¼“
Return port connection (OUT)
G ¼“
Permissible operating viscosity
range
CMP1xx0-2
10 … 3000 mm²/s
CMP1xx0-4
10 … 1000 mm²/s
Permissible viscosity range for the
measurement operation
CMP1xx0-2
10 … 1000 mm²/s
CMP1xx0-4
10 … 800 mm²/s
Total flow rate:
50 Hz
60 Hz
CMP1xx0-2
~ 180 ml/min
~ 220 ml/min
CMP1xx0-4
~ 230 ml/min
~ 260 ml/min