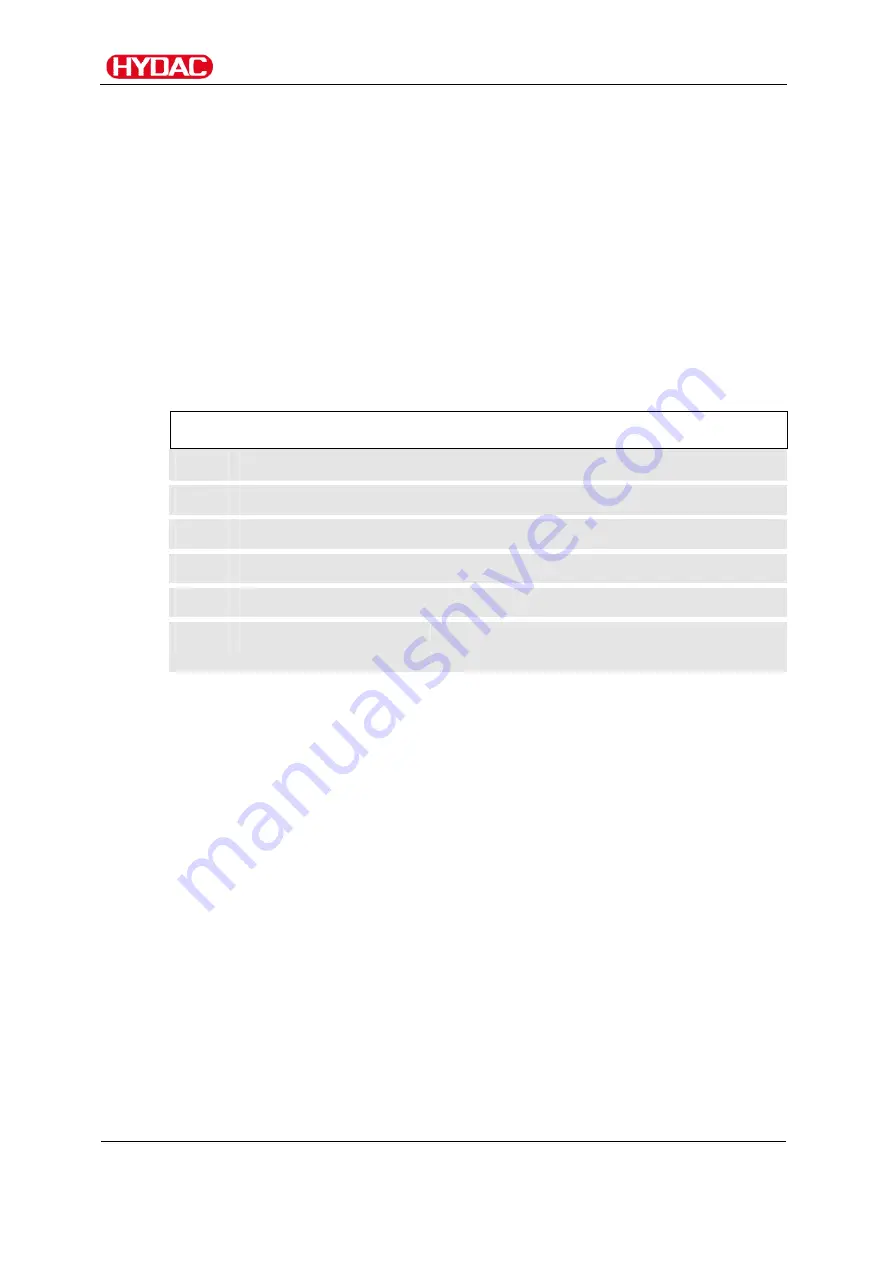
Hydraulic connection of the CMP
CMP1000
en(us)
Page 25 / 44
MoWa CMP 3528418d en-us 2015-01-06.doc
2015-01-06
Notes on pipes and hoses
In order to keep the pressure loss as low as possible, use as few threaded
connections as possible.
The pressure loss in a hydraulic line depends upon:
Flow
rate
Kinematic
viscosity
Pipe
dimensions
Fluid
density
The pressure loss can be estimated for hydraulic oils as follows:
∆
p
≈
6.8 * L / d
4
* Q * V * D
∆
p
= Pressure differential in [bar]
L
= pipe length [m]
d
= internal pipe diameter [mm]
Q
= Flow rate [l/min]
V
= Kinematic viscosity [mm²/s]
d
= Density [kg/dm³]
Mineral oil-based hydraulic fluid has a
density of ~ 0.9 kg/cm³.
This applies to straight pipe runs and hydraulic oils. Additional threaded
connections and pipe bends increase the pressure differential.
Keep the height difference between the unit and the oil level in the tank as
low as possible.
Hoses must be suitable for suction pressures of at least -0.5 bar.
Constrictions in the connections and lines should be avoided. This could
compromise suction output and cause cavitation .
Note that the nominal size of the connected hoses/piping must be at least as
large as the cross-section of the INLET connection.
Make sure that no tension or vibrations are carried over to the pump or filter
housing when the pipes are connected. Use hoses or expansion joints if
necessary.