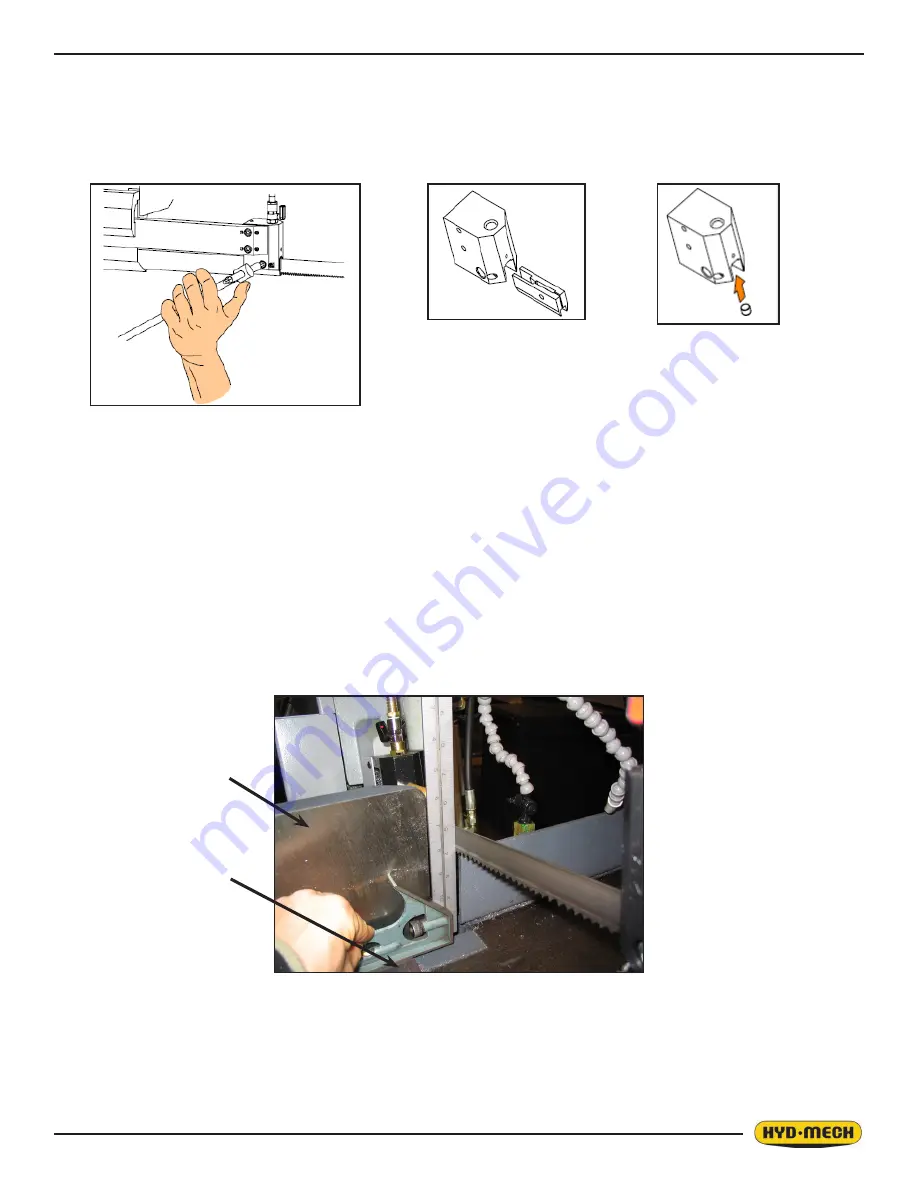
3.5
CARBIDE REPLACEMENT
The blade guide blocks are equipped with one top carbide and two side carbide inserts each. The working life of carbide
guides is practically the same as that of the machine itself. However, if required they can be replaced by removing the
plate fixing screw as shown.
BLADE PERPENDICULARITY
The perpendicularity of the blade to the work table and proper blade tension are vital for achieving straight cut. This
adjustment is carried out using a workshop square, which should be placed against the side of the blade while resting on
the work table in the middle of the guide arm span. The square edge should contact the blade uniformly along the whole
blade width. Follow the procedure below if the guides need to be adjusted to achieve the proper blade perpendicularity.
. Disconnect machine from power.
2. Open the vise.
3. Position the square on the clean work surface of the infeed table against the blade close to the datum jaw at a
point where the blade teeth do not prevent contact.
The top carbide is press fit into the guide block. If the
top carbide needs replacement the whole guide block
has to be changed.
Datum Jaw
Infeed Table
Summary of Contents for S20 SERIES III
Page 2: ......
Page 16: ......
Page 24: ......
Page 36: ......
Page 38: ......
Page 39: ...5 1 FOR HYDRAULIC SCHEMATICS AND PLUMBING DIAGRAMS SEE PDF ON ATTACHED CD SECTION 5 HYDRAULIC ...
Page 40: ......
Page 41: ...6 1 FOR MECHANICAL ASSEMBLY DRAWINGS SEE PDF ON ATTACHED CD SECTION 6 MECHANICAL ASSEMBLIES ...
Page 42: ......
Page 43: ...7 1 FOR OPTIONAL ASSEMBLY DRAWINGS SEE PDF ON ATTACHED CD SECTION 7 OPTIONS ...
Page 44: ......
Page 46: ...8 2 S20 Series III Layout ...
Page 47: ...8 3 S20 Series III Foot Print ...
Page 48: ......
Page 50: ......