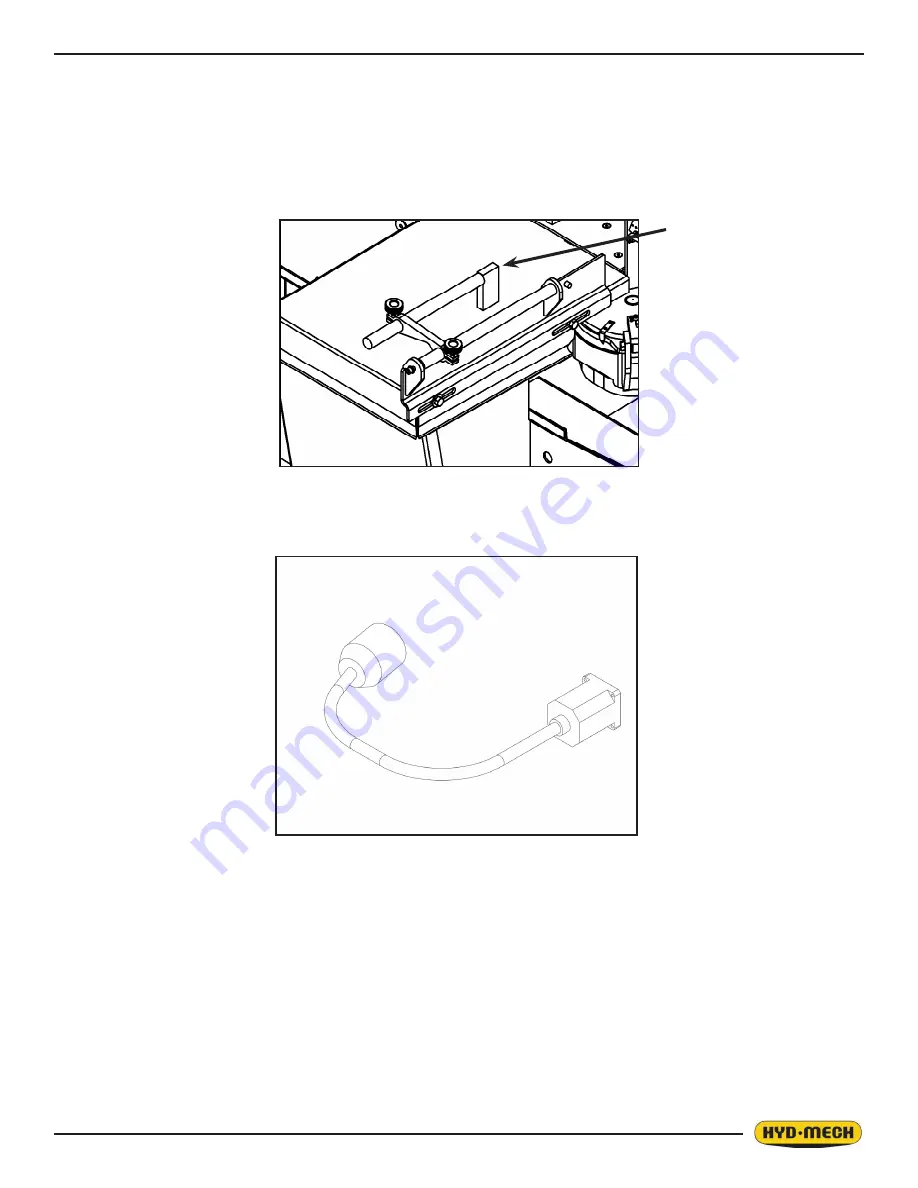
2.7
WORK STOP
The work stop is used to set a consistent cut length from 0 to 34 inches. The photo shows the stop at a short length, which
is adjusted with one or both of the locking handles. The bar with the actual stop attached to it can be removed, turned 80
degrees end for end, and inserted for longer lengths. The work stop may also be swung out of the work area when it is not
required.
WORK LAMP
Part # 37789
Work stop assembly
Summary of Contents for S20 SERIES III
Page 2: ......
Page 16: ......
Page 24: ......
Page 36: ......
Page 38: ......
Page 39: ...5 1 FOR HYDRAULIC SCHEMATICS AND PLUMBING DIAGRAMS SEE PDF ON ATTACHED CD SECTION 5 HYDRAULIC ...
Page 40: ......
Page 41: ...6 1 FOR MECHANICAL ASSEMBLY DRAWINGS SEE PDF ON ATTACHED CD SECTION 6 MECHANICAL ASSEMBLIES ...
Page 42: ......
Page 43: ...7 1 FOR OPTIONAL ASSEMBLY DRAWINGS SEE PDF ON ATTACHED CD SECTION 7 OPTIONS ...
Page 44: ......
Page 46: ...8 2 S20 Series III Layout ...
Page 47: ...8 3 S20 Series III Foot Print ...
Page 48: ......
Page 50: ......