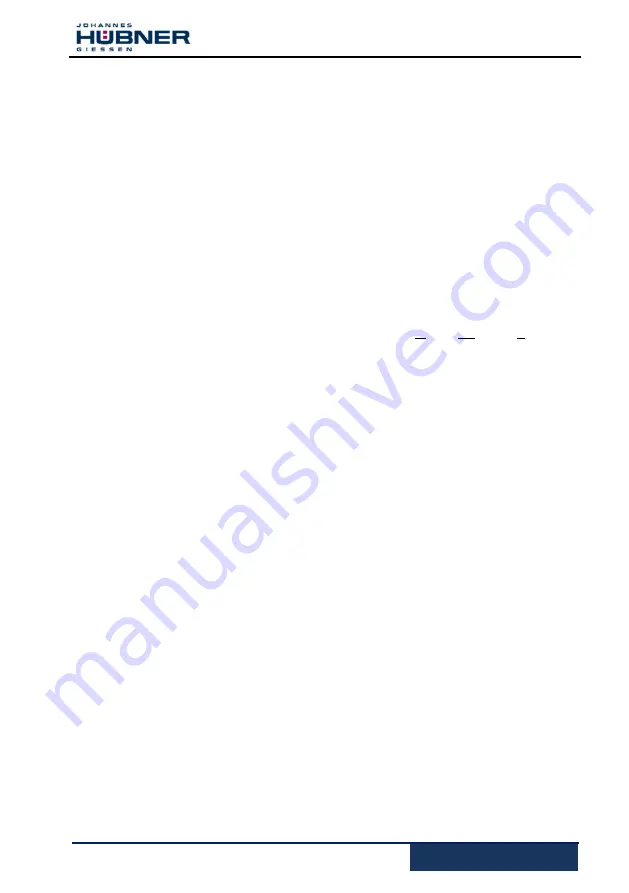
Incremental Encoder FG 41
9
1.3.1 Main Features
The entire system electronics has a discrete design. Neither microcontrollers nor
programmable logic elements are contained in the system electronics. There is no interpolation
or signal multiplexing. All signal lines are led separately within the electronics.
1.3.1.1 Variant 1 (FG 41 SIN/COS)
Incremental interface with analog output signals SIN±, COS± and Ref±; output level
1 Vss.
The safety-evaluated measuring system is designed for the implementation of safety-related
functions in relation to speed and direction of rotation. In the downstream fail-safe processing
unit an ideal error detection also occurs through evaluation of the annulus relationship
“SIN(x)2 + COS(x)2 = 1”.
The Ref± reference signals are not evaluated from a safety viewpoint and may not be used for
safety-oriented purposes.
1.3.1.2 Variant 2 (FG 41 TTL/HTL)
Incremental interface with digital square-wave output signals 0°,
0°
, 90°,
90°
und N,
N
, output
level in TTL or HTL logic.
The safety-evaluated measuring system is designed for the implementation of safety-related
functions in relation to speed and direction of rotation.
An internal signal monitor constantly checks the annulus relationship
"SIN(x)
2
+ COS(x)
2
= 1". Safety-relevant errors are indicated by switching of the signal outputs
to tri-state. The K0± reference signals are not evaluated from a safety viewpoint and may not
be used for safety-oriented purposes.
1.3.2 Principle of the safety function
System safety results when:
–
the scanning channel is single fault safe thanks to its own diagnostic measures and circuit
measures
–
the control checks that the received incremental data meet the expected tolerance window
according to the application.
–
for variant 1, the control also checks the annulus relationship
SIN(x)
2
+ COS(x)
2
= 1; if the result is outside the tolerance range, the incremental data
must be evaluated as unsafe. In this way the control achieves an ideal error detection.
–
when errors are detected the control introduces appropriate safety measures defined by
the system manufacturer
–
the system manufacturer ensures, through correct mounting of the measuring system, that
the measuring system is always driven by the axis to be measured and is not overloaded.
A fault exclusion is required for mounting the measuring system to the drive function.
–
the system manufacturer carries out a proven test during commissioning
–
the downstream fail-safe processing unit evaluates the measuring system differentially